he very term performance plastics embodies the expectations of the transportation industry. It evokes materials that are lightweight for speed, flexible for design, colorful for beauty, impact resistant and anti-microbial for safety, clear for visibility, as well as water and weather resistant. The transportation market is one of the largest manufacturing segments in North America and there are a wealth of potential plastic sheet and film applications for the OEMs and aftermarket segments.
The opportunities for plastic shapes distributors to gain access to the various transportation market segments continue to increase with such megatrends as anti-microbial conditions, increased light-weighting (particularly for the electronic vehicles segments), sound absorption improvements, safety enhancing requirements and the use of sustainable and recycled materials.
Plastic shapes distributors can offer their stocking and fabrication services to multiple levels in the supply chain in the transportation market. As part of the handling of returned scrap and providing regrind plastic, distributors have another possible value-added service in the toolbox.
- Non-carpet flooring using thermoplastic polyolefin (TPO) or thermoplastic rubber (TPR)
- Body panels using acrylonitrile-butadiene-styrene (ABS) or TPO with ultraviolet (UV) resistant films or additives
- Lighting products using acrylic and polycarbonate (PC) sheet or film
- Sound absorbing components using ethylene-vinyl acetate (EVA)
- Aftermarket uses such as bumper replacement using utility-grade ABS
Specialty vehicles such as ATVs and UTVs also fall into this category, where ABS, TPO and PC/ABS work well for durable, lower volume parts for fenders and doors. Decorative films such as camouflage prints add customization to a part, increasing the breadth of interest for thermoformers.
Then there are the ever-increasing number of electronic vehicles where TPO and multi-layer sheet of polyvinyl chloride (PVC)/acrylic with anti-stat and fire-resistant properties are needed for the battery trays and covers, such as parts for lithium-ion battery packs, nickel-metal hydride (Ni-MH) battery cell enclosures and snap-fit lithium-ion (Li-ion) battery cell packs and for shims used with the batteries. As the autonomous electric-based propulsion systems evolve, the need for materials with multi-electrical (conductivity and insulative) properties increase. Anti-static high-impact polystyrene and anti-static glycol modified polyester terephthalate (PETG) will be needed for parts making up those systems.
- Bus/Rail
- Seating and structural components using ABS, TPO and flame-rated materials PVC/ABS and PVC/acrylic
- Durable flooring is best served by using flexible TPO
- Flame-rated sheet used in shims in SAFT batteries
- Aerospace
- Seating and structural components such as bulkheads, cockpit and galley areas using PVC/ABS, PVC/acrylic and TPO
- Flame-rated sheet used in shims in SAFT batteries
- Cell cast and stretched acrylic are used in military, commercial and general aviation glazing for fixed and rotary wing:
- Aircraft transparencies
- Cabin windows
- Edge-lit illuminated panels
A market that is not quite as widely thought about when it comes to transportation industry is the marine industry. Weather-resistant and durable structural components can be manufactured from foamed ABS, specifically stringers and reinforcements, which is a better solution than plywood. For a truly luxurious look and feel, there is the option for soft-feel PVC over ABS configuration.
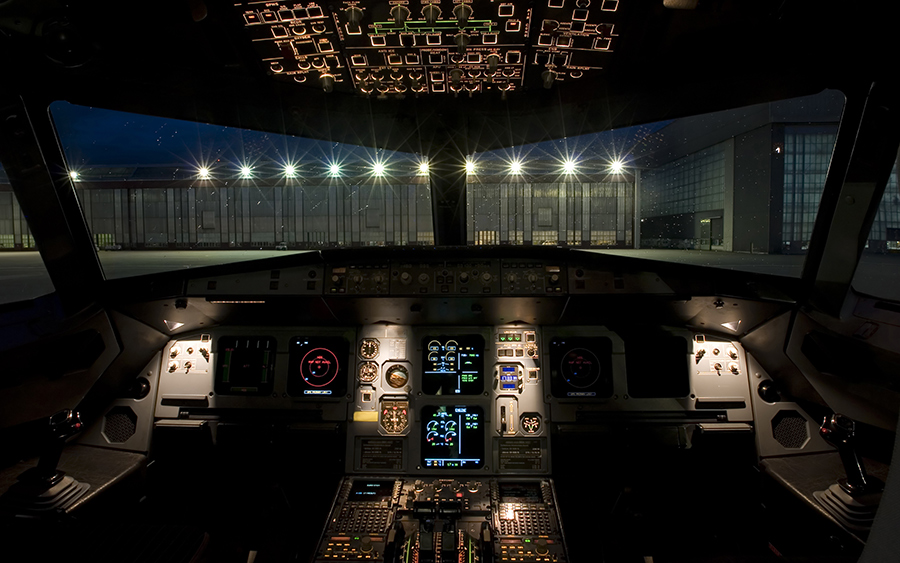
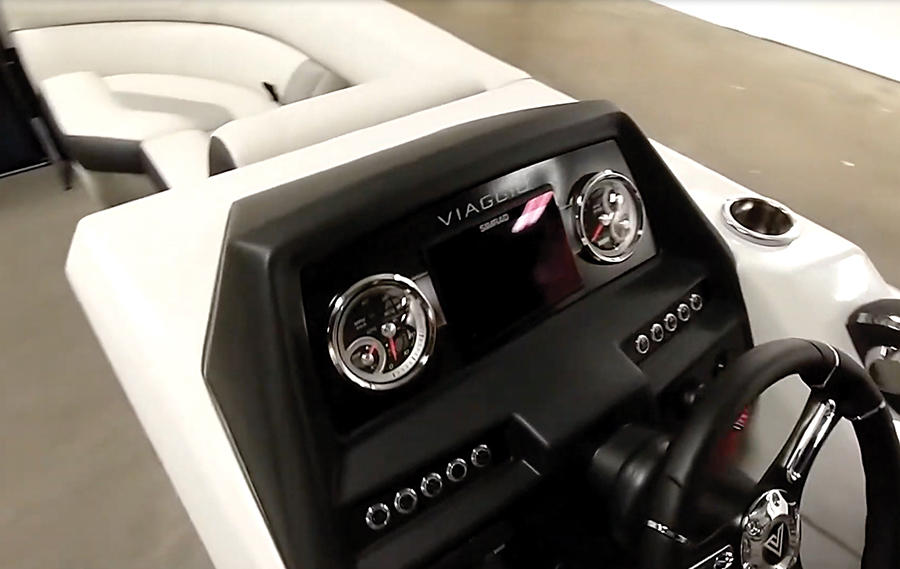
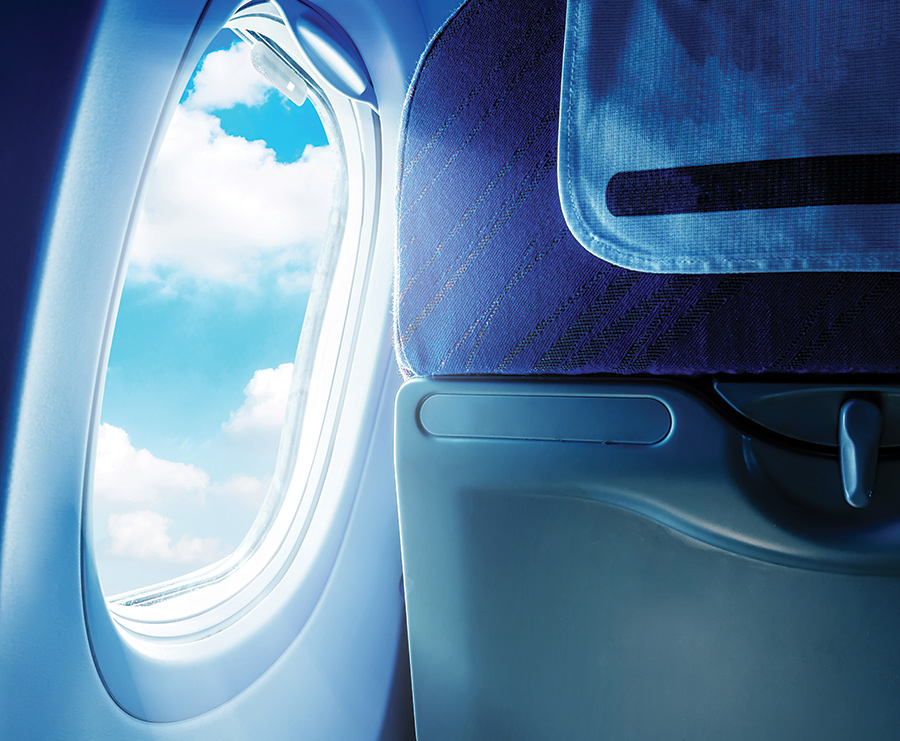
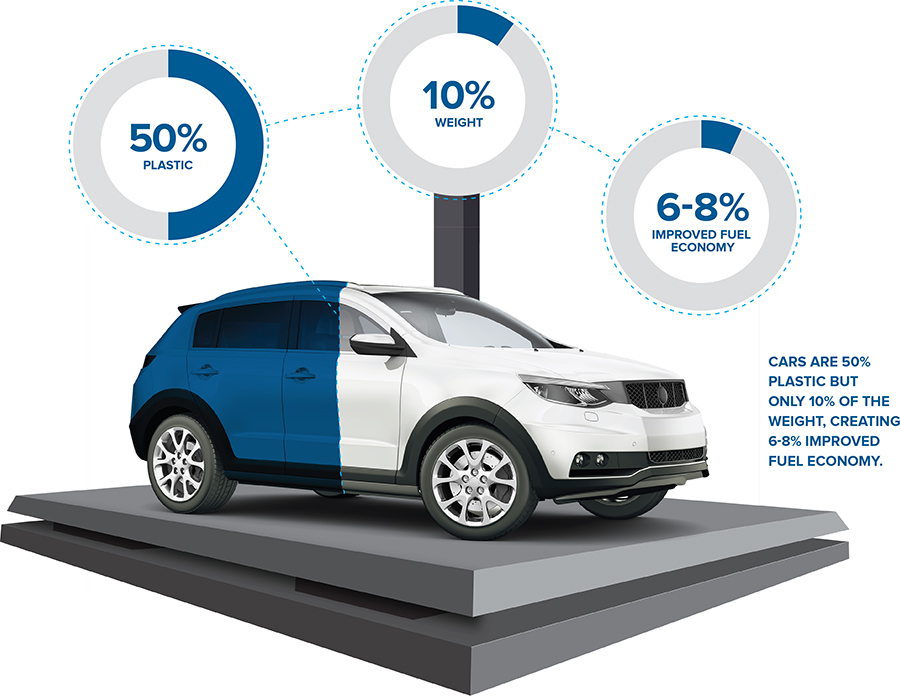
Light weighting the product lessens the environmental burden as well. Consider these numbers:
-
Typically, plastics and plastic composites account for about 50 percent of the volume of a typical vehicle, but only 10 percent of its weight. (www.plasticsmakeitpossible.com/whats-new-cool/automotive/carbon-fiber-reinforced-plastics-role-in-autos-growing/)
Reducing a vehicle’s weight by 10 percent can improve the fuel economy by 6 to 8 percent. (www.energy.gov/articles/545-mpg-and-beyond-materials-lighten-load-fuel-economy)
Combining the social and economic factors are inherent due to plastic’s durability. Automotiveplastics.com points out that “Anti-odor, anti-microbial fabrics and self-cleaning interiors can mean stretching a product’s useful life.” (www.automotiveplastics.com/mobility-trends/sustainability/)