EnvironmentalCorner
pplication and field engineers in the polymer industry are often asked for advice regarding chemical resistance, weathering performance, regulatory compliance, temperature rating, mechanical strength and physical toughness of materials. Lately, as the world adopts a more sustainable mindset, another question has become increasingly popular: “Is the material I am considering readily recyclable?”
While being educated in many different materials, the polymer family the authors are most familiar with is polyvinylidene fluoride (PVDF), which includes PVDF copolymers. This high-performance thermoplastic is known to have excellent chemical resistance to acids, halogens, hydrocarbons and oxidizing agents, even at high temperatures. The UL® RTI rating of this polymer family for homopolymers and copolymers can be as high as 302oF/150oC. It is also well known for extreme weathering resistance in sunlight exposure, retaining its mechanical properties and even the initial color of a coating or a part for more than 40 years1.
PVDF is a unique fluoropolymer in that it can be processed at relatively low temperatures on the same equipment as common polyolefins such as polyethylene and polypropylene. Common processing methods include profile extrusion, injection molding, compression molding, injection blow molding, 3D printing2 and solution casting.
With these performance attributes and wide range of processing methods, PVDF is an excellent material to consider for durable and sustainable solutions for a more circular economy. With the ability to be processed and reused up to five times, PVDF does not lose any appreciable mechanical or physical properties. While processing, it is common to use up to 20 percent reprocessed material in the manufacture of injection molded and extruded products. There is even a 3D printing company making park bridges out of PVDF reprocessed material3. It is feasible for a manufacturer to use 100 percent reprocessed material for chemical resistance or high temperature exposure applications, provided there were not special purity or regulatory requirements for the parts or items.
If the material is clean and without contamination, Arkema is proactively offering to buy back scrap materials, cut pieces, off color pieces or even fluid systems that have been installed and subsequently shut down. Since PVDF and PVDF copolymers are used as piping, tubing, valves, fittings and fabricated vessels for high purity water and drinking water, should any of these systems no longer be in use, the exposed PVDF materials should be safe to reuse in the current form. In another example, injection molded PVDF tower packing is used over and over in sulfuric acid and chlorine scrubber systems because it does not lose properties like other polymers when exposed to harsh chemistries and high temperature. The same could be said for tubing products and certain mechanically joined piping systems such as corrosive waste drain products.
Figure 1 shows a photo of dump tower packing that can be used repeatedly, even in difficult chemical service. Figure 2 shows an example of flexible PVDF copolymer tubing that could be easily reused or ground into pieces to be reprocessed to produce another high performing part.
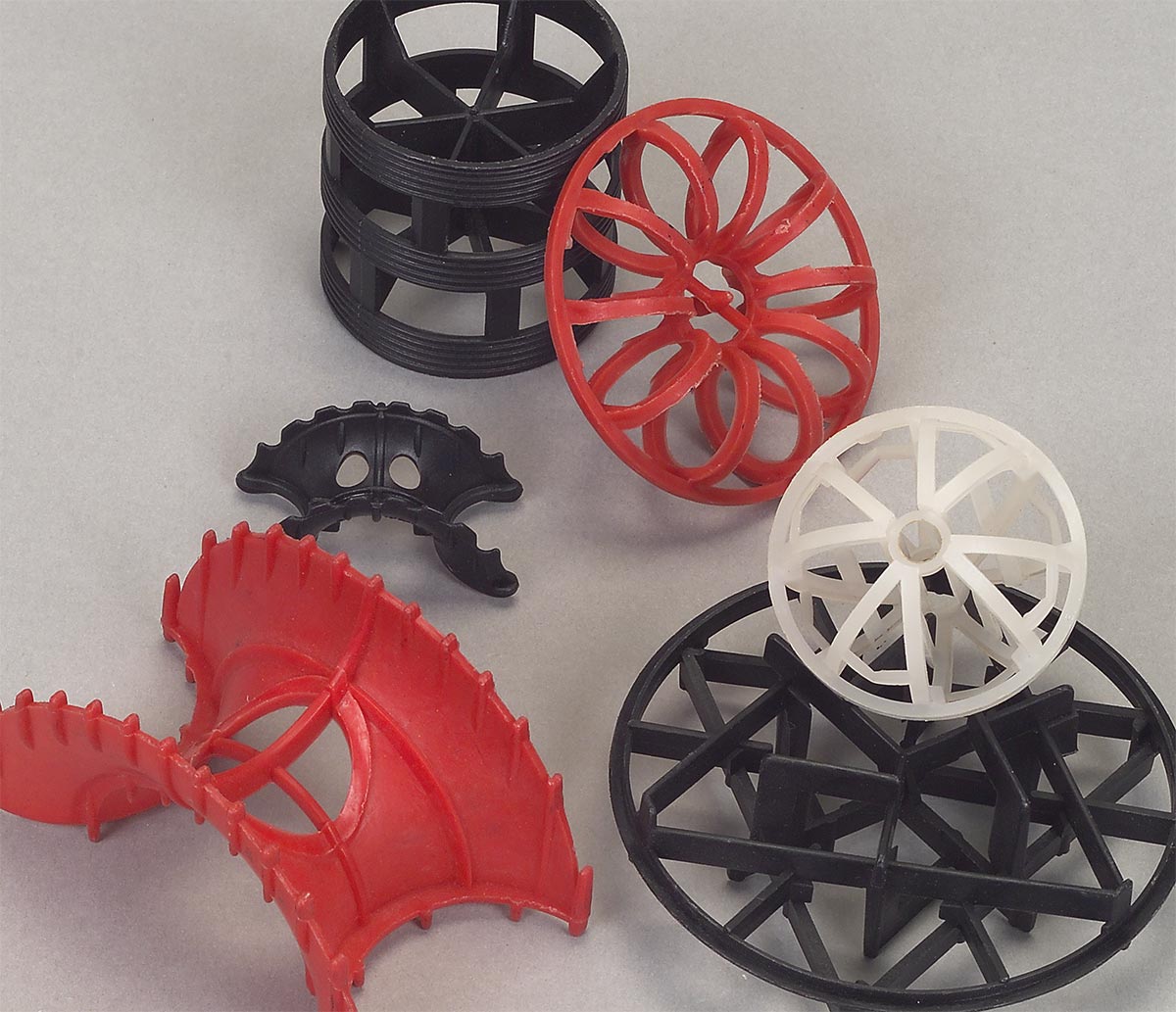
Not only are PVDF homopolymers and copolymers easily recycled in their pure form, PVDF copolymers have been found to be effective as a polymer processing and recycling aid (PPRA) for polyolefin films, cables, pipes and injection molded parts4. Each of these processing methods has a different need, but using a PPRA can increase output, improve surface finish, reduce die build up, reduce extruder pressure, improve flow, steady gauge control and allow processing at lower temperatures. Fluoropolymers and fluoroelastomers have been used for years to impart all of these benefits to polyethylene and polypropylene, but with the new emphasis on recycling as much as possible, the same benefits given to virgin resins are found to be more advantageous in recycling. Processes that would only allow 20-30 percent recycled materials before losing some performance can now be reprocessed using up to 90 or even 100 percent recycled materials to make items such as films, cables, pipes and injection molded parts. In the same work, it was found that materials already containing the PPRA recycle behave almost the same as a virgin material in which polymer processing aid (PPA) was added as a master batch at the extruder5.
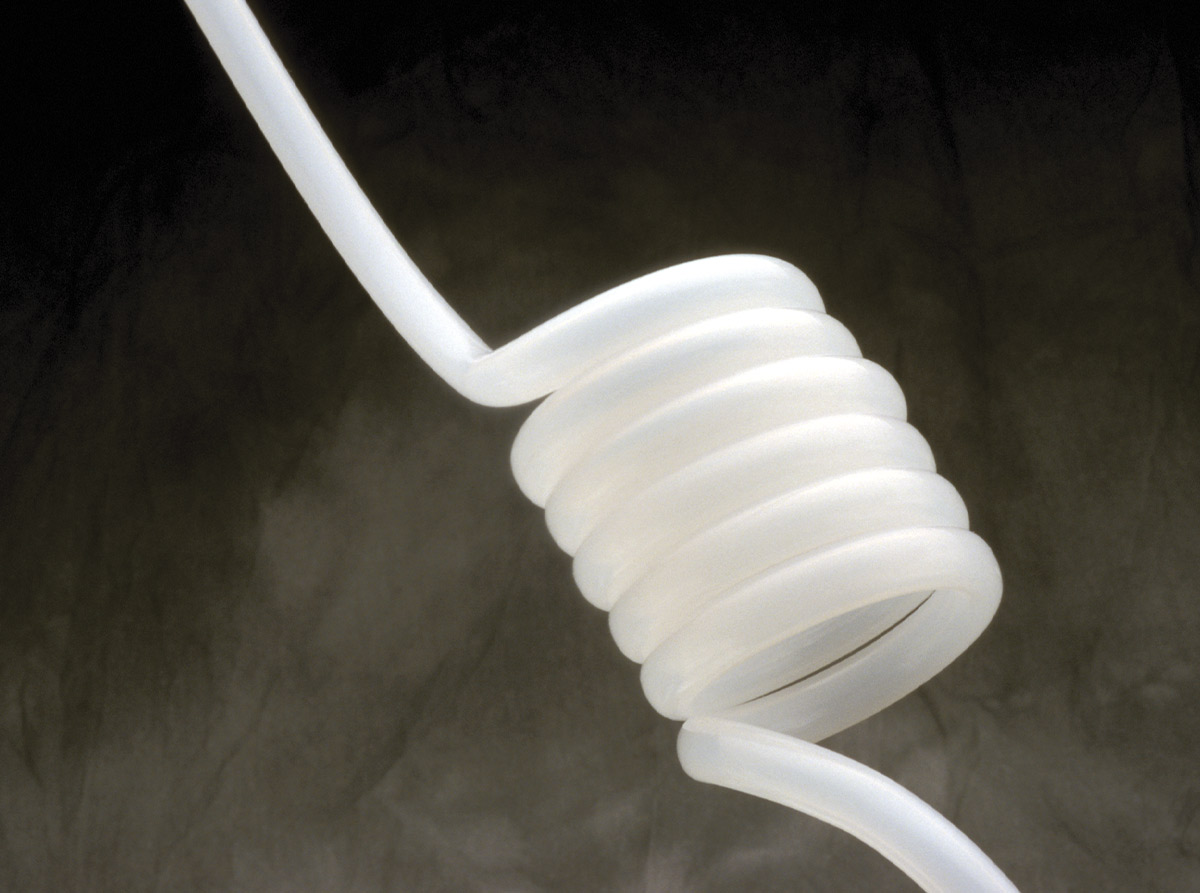

As discussed in this article, the PVDF family of thermoplastic polymers offer numerous benefits. They are readily and easily melt processed by many interchangeable methods for reuse as a high performing material. They keep their properties in severe applications and can even be reused in other severe applications without concern for failure. Finally, they assist in the reprocessing of high-volume polyolefins as a PPRA. If you work with PVDF and are looking for a place for material you can no longer use, consider Arkema’s takeback program to ensure that it goes on to serve a useful purpose in the circular economy.
- A. Palovcak; B.Douglas; “Kynar® Fluoropolymer – A Solution for the Most Extreme Weathering Conditions” Plastictrends March 2017
- Liu, David Shin-Ren, et al, US Patent 10633468 (April 2020)
- https://10-xl.nl/#portfolio
- Lowrie, R.; Henry, J.; DeAngelo, M.; Cavalier, C.; Seiler, D.; “The Effect of Fluorinated Thermoplastic Processing Aids in Film Processing of Recycled Polyethylene Resins” Presented at Compounding World Expo, Cleveland, OH, NOV 2021
- Seiler, D. A; Lowrie, R: Henry, J. ; Cavalier C. ; DeAngelo M.; “Study of the Positive Effects Seen When Using Fluoropolymer Polymer Processing & Recycling Aids (PPRA) in Reprocessed LLDPE” Presented at SPE International Polyolefins Conference, Galveston, TX, FEB 2022