These organizations can conduct research, develop and manufacture items such as medical devices and diagnostic equipment, pharmaceuticals, prosthetics, food processing, botanical science and crop technologies, to name a few applications. As innovations and investments continue in these areas, some are growing quickly. Investments in this industry show optimism about future growth. To keep that growth on track, companies are concerned about keeping their supply chain operating efficiently and cost effectively. Many companies outsource manufacturing to other countries, but plastics distributors, with their stocking and fabrication services that can supply multiple levels in the supply chain, have the local edge.
Smaller parts for devices and instruments that are used outside the body or implanted in the body must withstand even more harsh conditions and stringent regulations. Plastics may be subject to sterilization, reagents, bodily fluids and extreme temperatures so they must be the most durable and highest quality plastics. Materials that fit this profile include acrylics, polycarbonate (PC) and PP. Cast acrylic is used for in-vitro diagnostics devices such as blood glucose monitors, self-test devices and devices for detecting infectious agents, to name a few. It is also used for prosthetics and orthopedic appliances, which are exposed to all the above environments.
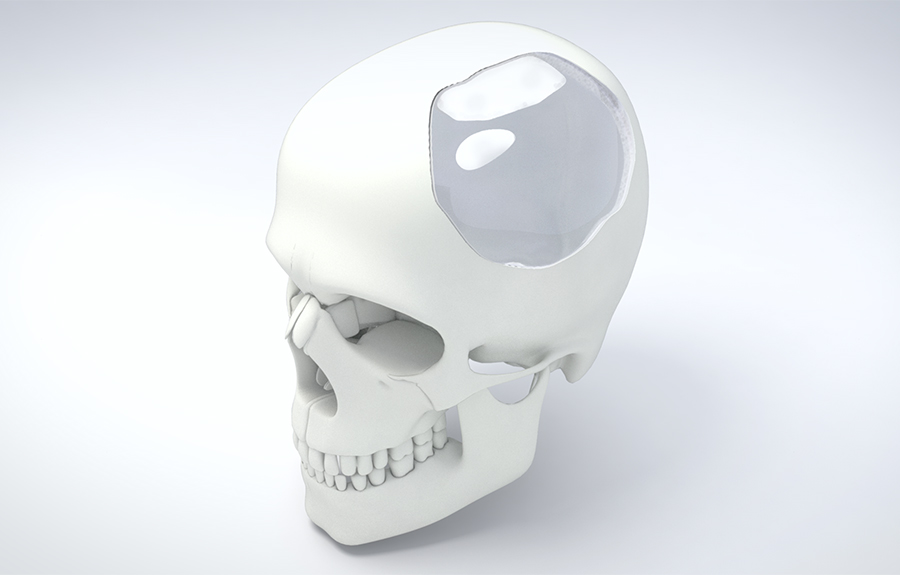
When used as a life sciences plastic, PP sheet is easily formed into surgical trays and sterilization containers because it can withstand high temperatures. It also has excellent chemical, impact and abrasion resistance. It can be an economical alternative to high-density polyethylene (HDPE) or ABS — other popular industrial-grade plastic sheets.
Plastics are used not only in equipment and devices. Pharmaceutical packaging and crop technologies use various film structures; for example, tablet packaging uses duplex and triplex laminated structures with an oxygen and moisture barrier. Some European manufacturers are starting to use polychlorotrifluoroethylene (PCTFE) barrier coated films as a lower cost alternative to PVC.
PP and polyethylene (PE) breathable bags are paired with breather patch material to control transpiration of biologically generated gases through the breathable membrane to sustain consistent growth of spawn or tissue culture in a separate, sterile environment. Some of these applications are for use as an isolated, aseptic (sterile) bio-product environment and allowing needed transpiration of gases would be for tissue culture growth and bioreactors for seed or tissue culture growth.