Governments, cities, municipalities, major manufacturing businesses that use large amounts of water are required to clean water before returning it. We call the cleaning process wastewater treatment. In simplest terms a highly engineered system brings wastewater in, cleans it using a process sequence that includes the settling of solids (sedimentation) and biological and chemical treatment prior to the water being returned either to the process consuming water or as an outflow completing the water cycle.
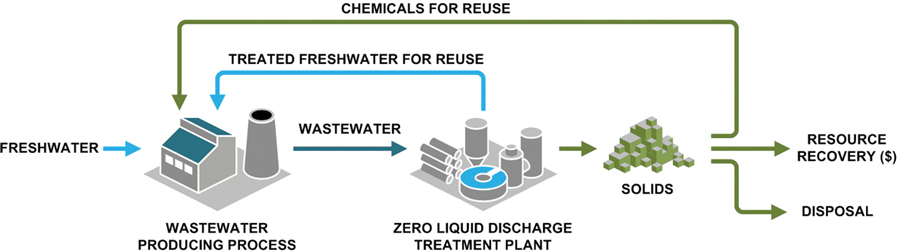
The most common fit for these engineering plastics is in the clarifiers where particulates are removed from water via sedimentation. We have all seen these systems, which can be round or rectangular.
Despite what seems at first glance to be static systems, these clarifiers have many moving parts including: scrapers or flights that drag along the tank bottom; sprockets and chain that move the flights, chain tensioners, shafts and wear shoes that provide wear and abrasion resistance and a collector that skims floatable solids from the surface of the water in the tank.
Below is a typical set up for a rectangular clarifier. All components within the tank are today plastic, eliminating corrosion while reducing the weight and resultant stress on all parts of the system. These parts spend most of the time below the surface of the water and are not visible when the systems are functioning.
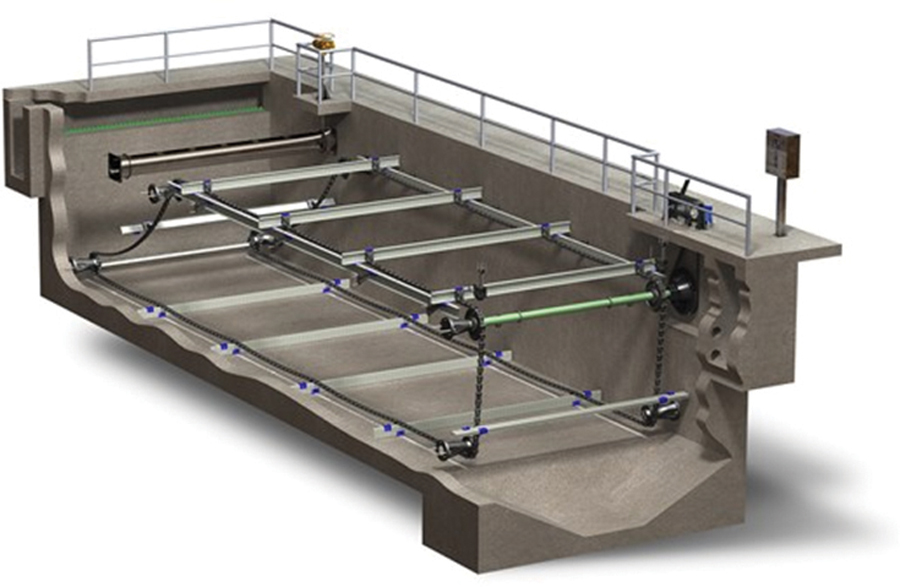
Opportunities for serving this industry exist at OEMs and individual wastewater treatment facilities. Do not be tempted to suggest other materials for such wear parts. Although acetal (POM) or polyester PET may do better than nylon in a wet food industry application, they will not survive the abrasive conditions in these systems. High-density polyethylene (HDPE) or polypropylene (PP) may offer improved cost, inertness and weldability over UHMW-PE but will again not provide the abrasion resistance required by parts operating within such systems.