Fluoropolymer resins are used in high purity components in semiconductors for their resistance to corrosive acids, being inert to common process chemicals and having minimal contamination to flow. Because metal particles contribute the deadliest types of contamination to a semiconductor chip, perfluoroalkoxy (PFA) fluoropolymer resin has provided the best overall material solution.
Other fluoropolymers, such as polyvinylidene fluoride (PVDF), polytetrafluoroethylene (PTFE), ethylene-tetrafluoroethylene (ETFE) and more are used commonly in systems; however, they have greater material or cost issues. These fluoropolymers also have a higher heat deflection temperature, making them suitable for the exothermic reactions that occur during the coating processes.
Other materials include polypropelene in structural tanks and cabinets. Acetals, polyetheretherketone (PEEK) and polyvinyl chloride (PVC)/chlorinated polyvinyl chloride (CPVC) have been used in the mechanical aspects, according to the heats bring release. Polycarbonate is used sparingly, as it does not stand up to some of the harsh chemicals. Often times, clear PVC or polyethylene terephthalate (PET) is used for viewing windows and clear guarding.
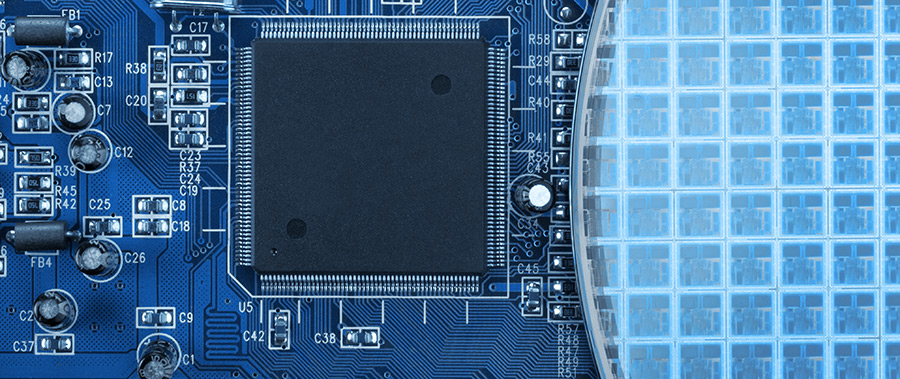
Pipes, valves and fittings are made from some of the same components. Flexible tubing will be ultrapure, usually a fluoropolymer. Waste transfer lines still need to be able to handle the high temperatures and chemical corrosiveness of said waste chemicals. High-purity piping systems make for most of the chemical lines in the semiconductor industry.
The big issue with today’s chip makers involves the increase in production. Because of the supply chain disruptions caused by shortages in semiconductors, chip manufacturers are looking to double their output. This means moving from small batch chemical purification standards to large scale requirements. Increasing the flow of chemicals is not as simple as using larger pipes, chemical tanks, and more wafer handling parts. Larger components will open the door for more contamination, so purity is put to the test.
The semiconductor chip industry hopes to double its output, as it has been for the last few decades. This means ramping up production, keeping systems clean and analyzing the systems for purity. The systems now need to be able to detect imperfections before they get into the process, and thermoplastics such as fluoropolymers are going to continue to play a key role in the industry.