The very term performance plastics embodies the expectations of the transportation industry: lightweight for speed, flexible for creative and useful design, colorful for beauty, impact resistant and anti-microbial for safety, clear for visibility, as well as weatherability and corrosion resistance.
The opportunities for performance plastic shapes distributors to gain access to the various transportation market segments continue to increase with megatrends such as increased light-weighting, sound absorption improvements, safety enhancing requirements and the use of sustainable and recycled materials.
Performance plastics are used in a multitude of automotive parts from cars and trucks to the larger agricultural equipment such as tractors and combines. Which types of plastics are used in these vehicles? Some examples include:
- Non-carpet flooring such as trunk and bed liners using thermoplastic polyolefin (TPO) and thermoplastic rubber (TPR)
- Tonneau covers are generally TPO but can also use acrylonitrile-butadiene-styrene (ABS) sheet or polycarbonate/acrylonitrile-butadiene-styrene (PC/ABS) co-extruded sheet
- Body panels of ABS or TPO with ultraviolet (UV) resistant films or additives to enhance weatherability
- Lighting products made with acrylic and polycarbonate sheet or film
- Sound absorbing components using ethylene-vinyl acetate (EVA)
- Aftermarket uses such as bumper replacement using utility-grade ABS
- Flame-rated sheet used in shims in SAFT batteries
- Lenticular embossed sheet can provide visibility as a safety enhancement and interesting decorative effects
Specialty vehicles such as ATVs and UTVs fall under the category as well where ABS, TPO, PC/ABS work well for durable, lower volume parts for fenders and doors. Decorative films such as camo prints add customization to a part, increasing the breadth of interest for formers.
And then there are the ever-increasing number of electric vehicles where TPO and multi-layer sheet of PVC/acrylic with anti-stat and fire-resistant properties are needed for the battery trays and covers, such as parts for battery packs, battery cell enclosures and shims used with SAFT batteries.
As the autonomous electric-based propulsion systems evolve, the need for materials with multi-electrical (conductivity and insulative) properties increase. Anti-stat high-impact polystyrene and anti-stat PETG will be needed for parts making up those systems.
Sustainability is not just about recycling. Many thermoplastic materials have long been more sustainable than many think. In the manufacturing process, regrind use has been refined to use the most regrind possible without loss of the plastic’s structural and performance properties. Scrap that is created when forming parts can often be returned to the thermoplastic sheet manufacturer because most producers and formers have created infrastructures and procedures for returning scrap, which allows for the maximum use of post-industrial regrind.
Additional targets of sustainability are achieved because plastic parts reduce the vehicle’s weight and the durability can increase its useful life.
Plastic sheet provides many opportunities for entry into multiple segments of the automotive market due to the wide range of product materials and configurations available. Better yet, sustainability does not have to be sacrificed to achieve the performance capabilities required to create top quality, long-lasting parts. In addition, plastic sheet is often vacuum formed into parts more efficiently and with less cost than injection molded parts.
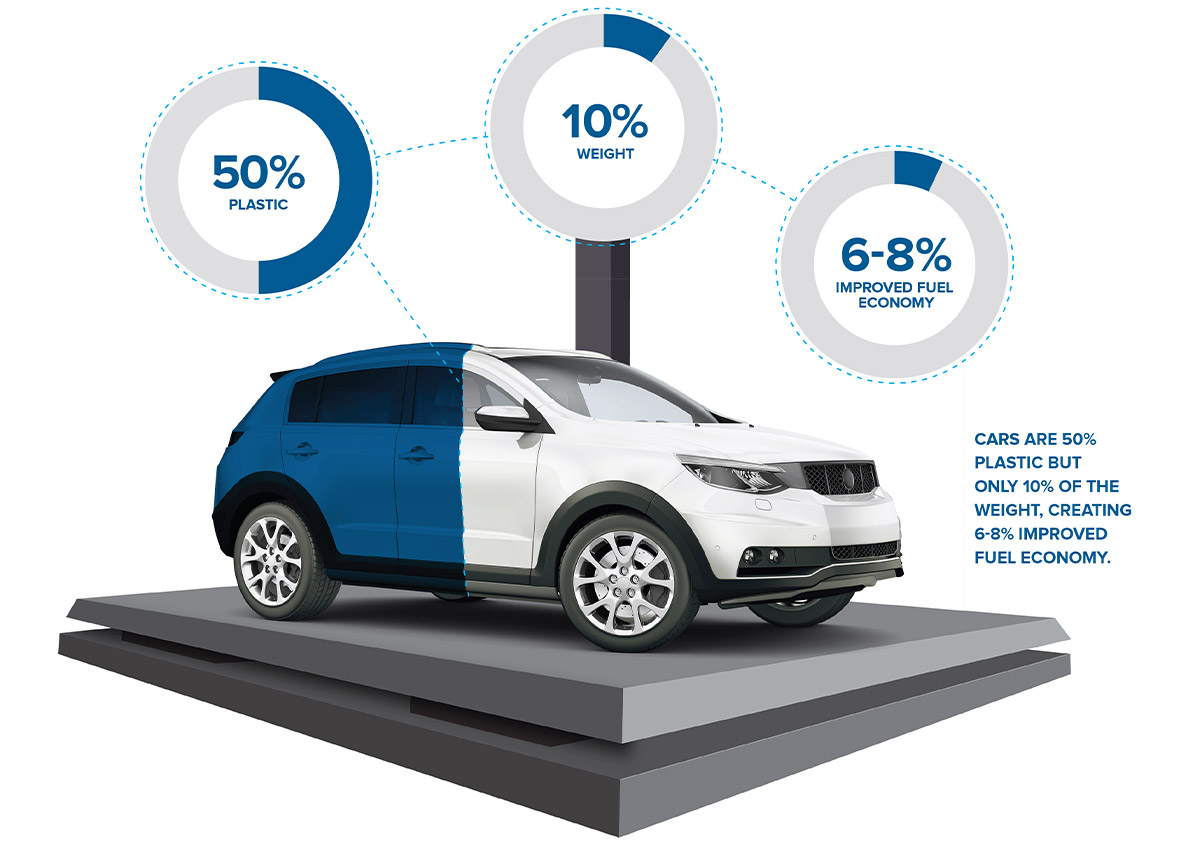