he world of plastics is an expansive one. From thermoplastics to thermosets and everything in between, plastics are everywhere around us. These materials are more than single use — they are enabling technological advancements by providing lighter-weight solutions to replace metals and other heavy materials. Fluoropolymers are one family of plastic materials that have a wide variety of characteristics and applications. Known for their high temperature capabilities, ultra-violet light (UV) resistance, chemical resistance, high purity and good flame and smoke properties, fluoropolymers are often used when service conditions exceed what commodity thermoplastics can handle.
One of these fluoropolymers, polyvinylidene fluorine (PVDF), has many applications. Known for its use in the semiconductor, chemical processing, biotechnology and pharmaceutical industries, PVDF has been used in critical applications for more than 60 years. From piping to tanks to pumps and other process components, PVDF materials are easily fabricated to offer long-standing life in aggressive and challenging environments. However, outside the traditional world of chemical handling, PVDF materials have made their entrance into the colorful world of amusement parks.
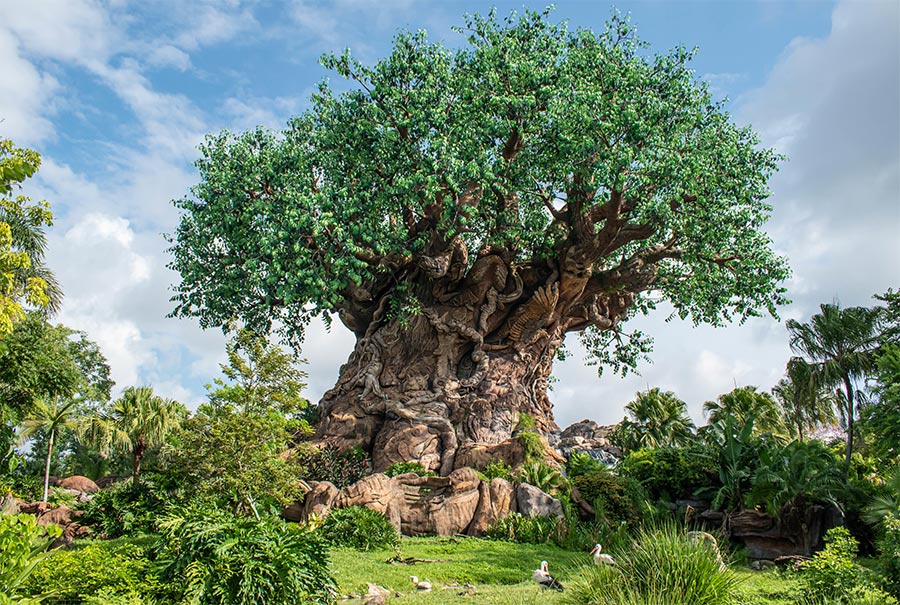
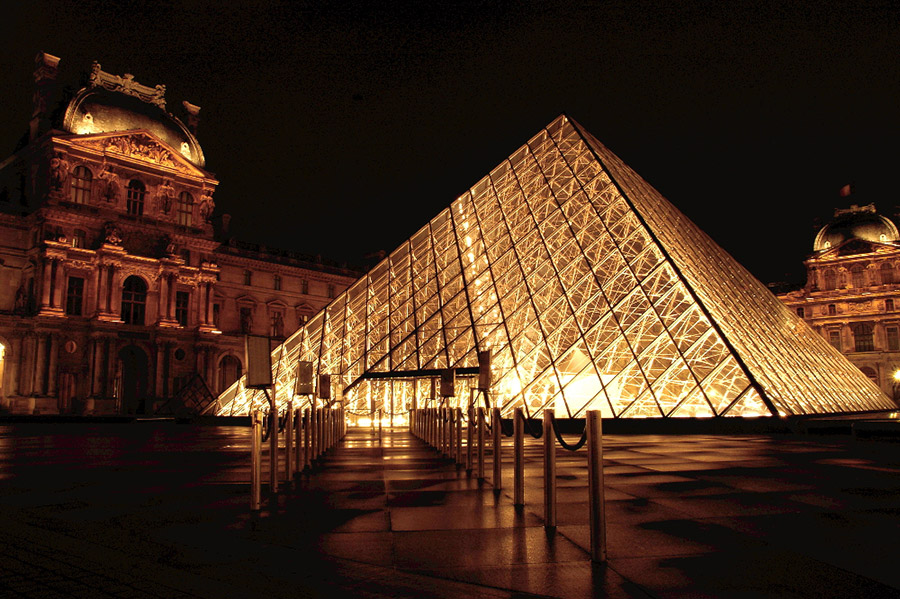
- Mechanical stability and ductility — The artificial scenery must be self-supporting. A material that has enough mechanical stability to withstand force yet is ductile enough for movement and simulating real-life plants is key. Wind and other daily external forces will exert constant stresses on materials, which makes toughness important. PVDF copolymers have the optimal blend of toughness, ductility and mechanical stability to provide stability. The table shows mechanical retention of PVDF copolymers after five and 10 years of accelerated weathering exposure.
- UV/Weathering resistance — Hurricane-force winds, heavy rains and direct sunlight exposure are common in outdoor theme parks. PVDF materials have incredible resistance to UV and weathering, lasting decades without color fade or property deterioration. PVDF materials are also UL 746C rated. The image below shows the superior performance of a famous PVDF coated building.
5
10
4,397
4,678
6,720
7,537
631
632
98%
105%
105%
105%
5
10
4,111
4,249
6,759
5,876
608
457
97%
100%
101%
76%
5
10
2,839
2,990
7,025
7,165
954
736
99%
104%
141%
109%
5
10
2,472
2,559
6,562
5,417
1,126
793
100%
103%
148%
104%
- Flame and smoke performance — PVDF materials are commonly used in applications where flame and smoke resistance is needed. These materials are also self-extinguishing and are UL® 94 V-0 which are important properties in stopping the propagation of fires. Virgin grades of PVDF have an LOI of 44, but special formulations with added flame and smoke resistant are available. These specialty grades have LOI >95.
- Chemical resistance — Animal droppings, due to acidity, can be quite aggressive to some materials. Cleaning chemicals may also be used in amusement parks. PVDF has a wide range of chemical resistance, making them useful for applications that require robust inertness.
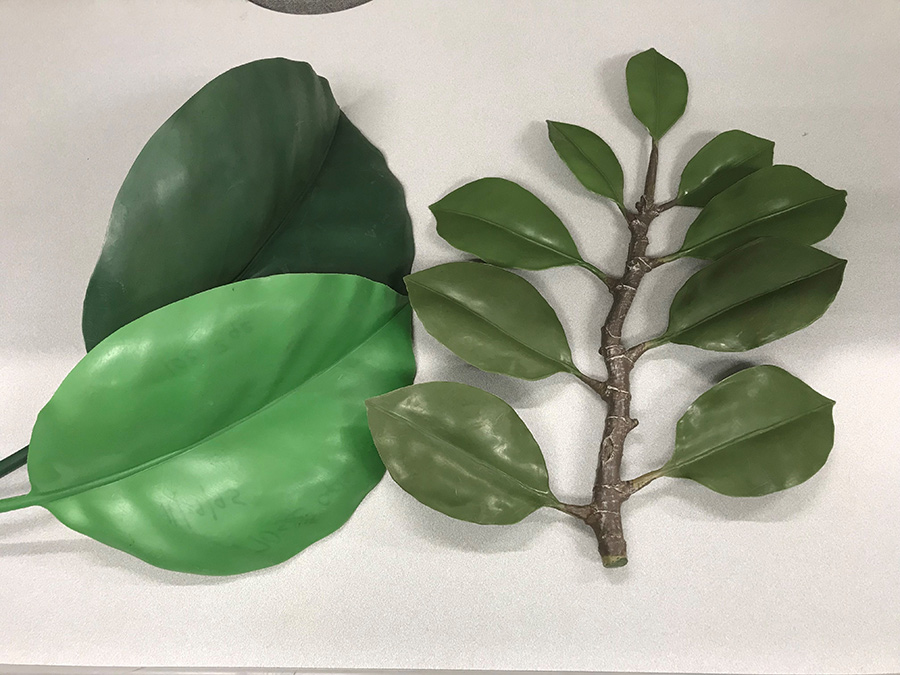
- Processability — For converters making injection molded components, it was important that the PVDF materials be processed safely and easily. Companies using standard injection molding equipment can also process PVDF materials with minimal processing adjustments. Furthermore, the ability to add colorants to make the tree colors more vibrant and dynamic was essential. PVDF materials, while naturally white in color, are commonly colored using special concentrates available in any color. Welding is also very important, as the trees will need to be assembled easily. PVDF materials are easily welded and can even be welded to other grades of PVDF.
The most well-known application for PVDF artificial leaves is Walt Disney World’s “Tree of Life” in Orlando, FL, USA. Thousands of leaves were injection molded using PVDF copolymers, which make the iconic tree a long-lasting past of the part. Additional trees fabricated out of PVDF materials include Disney’s Hong Kong Tree of Life, Winnie the Pooh tree, Dollywood’s Tree and many more!