othing comes before safety at IAPD member companies, including mine. But a review of our procedures led to an uncomfortable realization: Selling polyolefins by the sheet was a time and labor-intensive process. Picking teams in the warehouse spent hours every day repackaging sheets into smaller order quantities. This involved taking a full skid off the racks with a forklift, un-banding it, manually moving the ordered quantity of sheets to the shipping skid, then re-banding the full skid and replacing it in the racks. Repeated handling of these large, unwieldy sheets — which were 4′ x 8′ or 4′ x 10′ and could weigh more than 200 pounds — could lead to rushing, fatigue and other risky safety behaviors that might result in pinched fingers, back injuries or even something worse.
In response, a cross functional team resolved to create a process to prepackage the most common polyolefin items into set pallet quantities at the extruder, decreasing handling and waste. These efficiencies would allow my company and its customers to reap safety and sustainability rewards.
For nearly a year, the team worked out the details. They wrestled with new item numbers, shifts in inventory patterns, changes in the manufacturing process and even the height of the warehouse racks. Every time the team encountered an obstacle, they worked together to develop a solution.
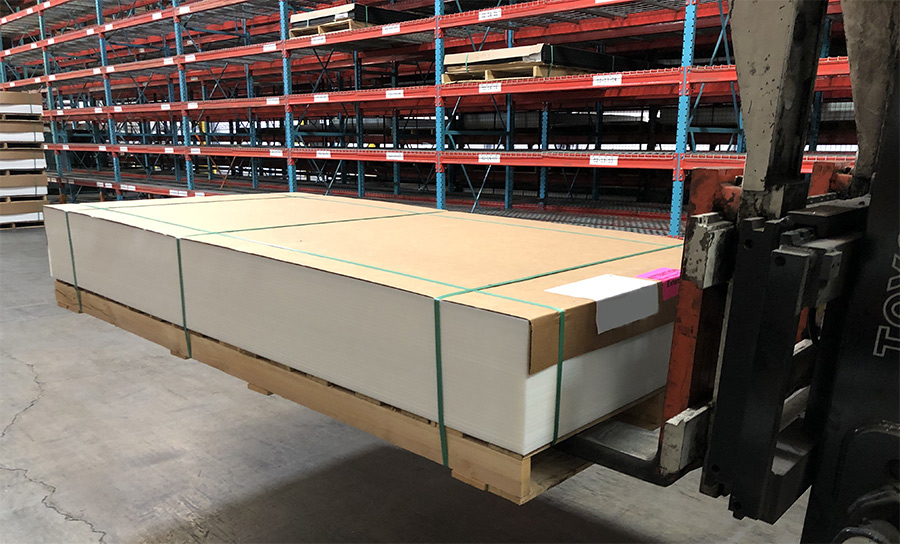
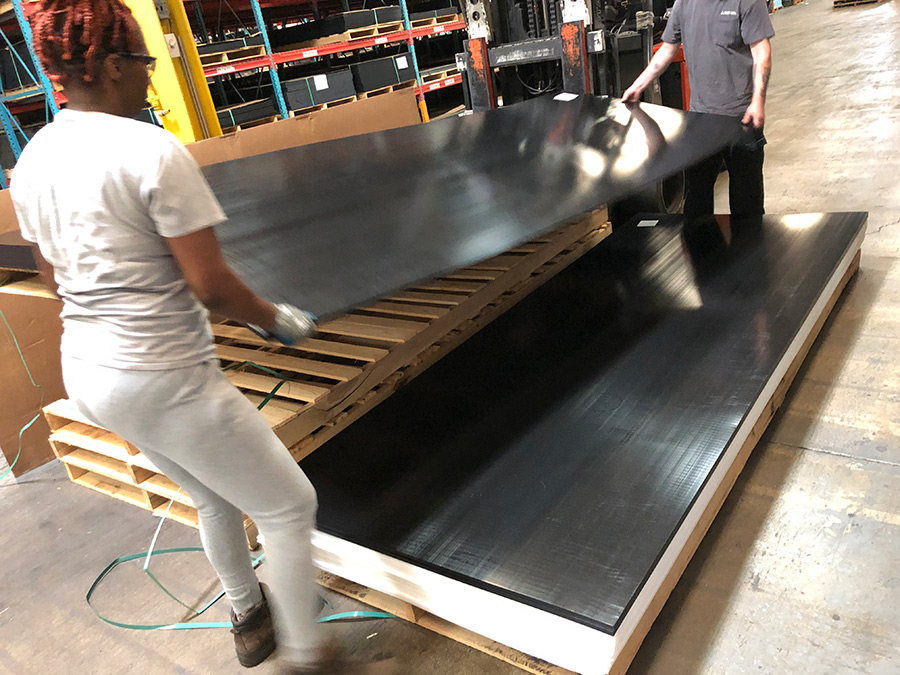
The pallet program launched in 2019 with 10 common gauges of high-density polyethylene (HDPE). It quickly took off, exceeding all expectations. It has since expanded to polypropylene (PP) and ultra-high molecular weight polyethylene (UHMW-PE), with new sizes and products added as internal and external stakeholders alike have embraced the model. The warehouse is so grateful for the efficiencies created that they have become the program’s biggest advocate, frequently leading the charge for new pallet items.
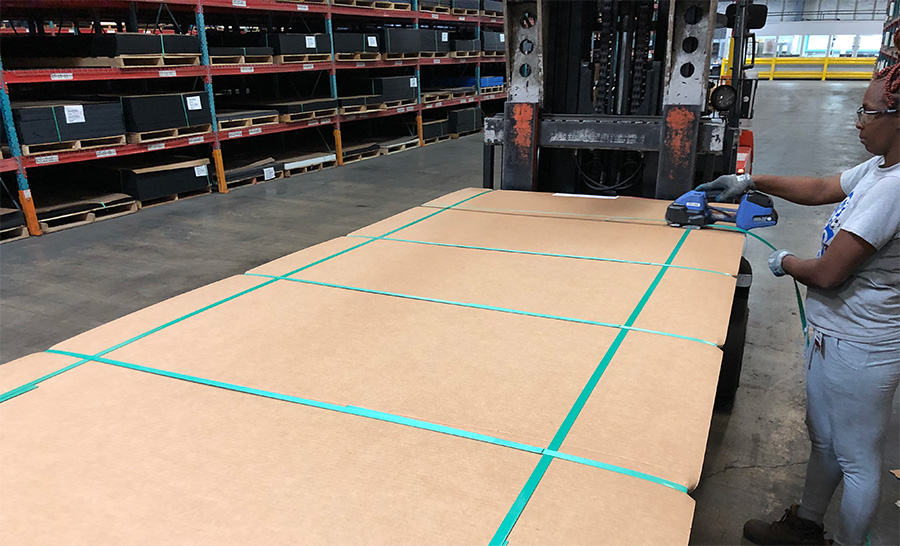
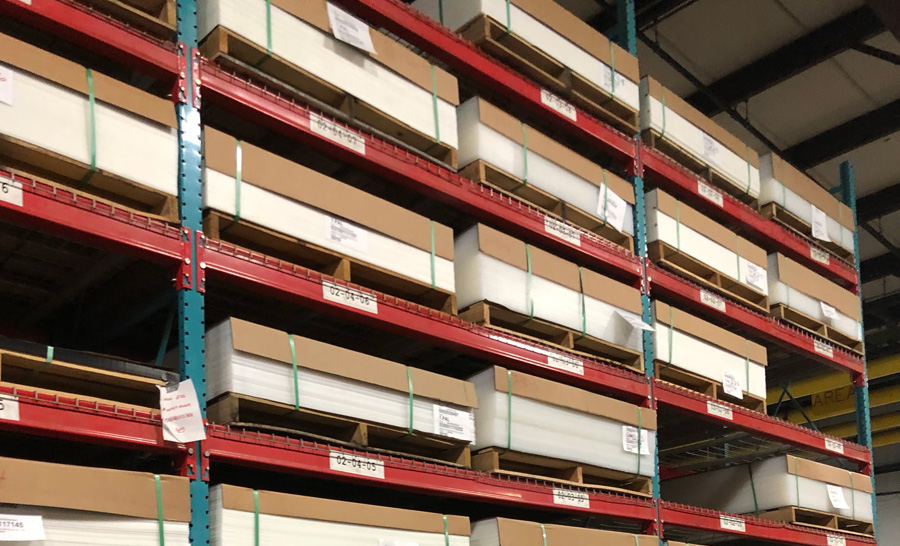
Ron Pierce, distribution manager, reflected fondly on the experience. “The business is always changing; we’re always met with new challenges and the pallet program was a step in the right direction. It was a great collaboration across many different departments: sales, planning, warehouse and manufacturing. It is still proving to be a great success. Many safety factors were eliminated or greatly reduced because of this program, less physical handling, going in and out of racks just to name a few. The time saved pulling pallets as opposed to single sheet handling was greatly reduced. We’re looking forward to extending this program into other product lines. I am very proud to be a part of such a project and what we as a team accomplished.”