lastics have a PR problem. The ever-growing amount of throwaway plastics is referred to as the plastic waste crisis. The perception of plastics is (zip)tied to beaches littered with plastic bags, empty plastic bottles and other single-use debris from the polystyrene and polypropylene categories. That was certainly my perception of plastic, anyway, as someone who was far removed from any kind of skin in the plastics game.
Recognizing my own ignorance on the plastic problem, I looked for some impartial research to learn more about the topic. I landed on the audiobook Plastic: A Toxic Love Story by Susan Freinkel. If you haven’t heard of it, I highly recommend it.
Coming from a mindset similar to Freinkel (plastics are bad but I’m willing to be open-minded for the sake of reporting), I appreciated her approach. Let’s just say the book was eye-opening. At the risk of sounding hyperbolic, I’d go so far as to call it mind-blowing.
The next thing I know, I’m discussing the book with friends and family. I couldn’t stop talking about the versatility of plastics, the scientific advancements, the invisible benefits and the misconceptions the public has about these materials. Medical tubing, refrigerators and children’s toys are all plastic! The surprise on their faces revealed they hadn’t realized that, either.
Plastic conversions have happened so often and so quietly that the general public doesn’t even know what’s plastic and what isn’t. That’s when I realized that most people are simply plastic blind. Since we didn’t know which fixtures in our daily lives were made of plastic, that could mean we didn’t see plastic anywhere. The only time we really see it is when it’s discarded as garbage. This “plastic blindness” seemed like a problem that needed solving.
When LinkedIn suggested I look into the copywriter position at Curbell Plastics, Inc., it seemed like fate. I could get into the plastics industry and try to find a way to fix the perception from the inside. If I thought Plastic: A Toxic Love Story was eye opening, imagine my surprise when I began working in plastics.
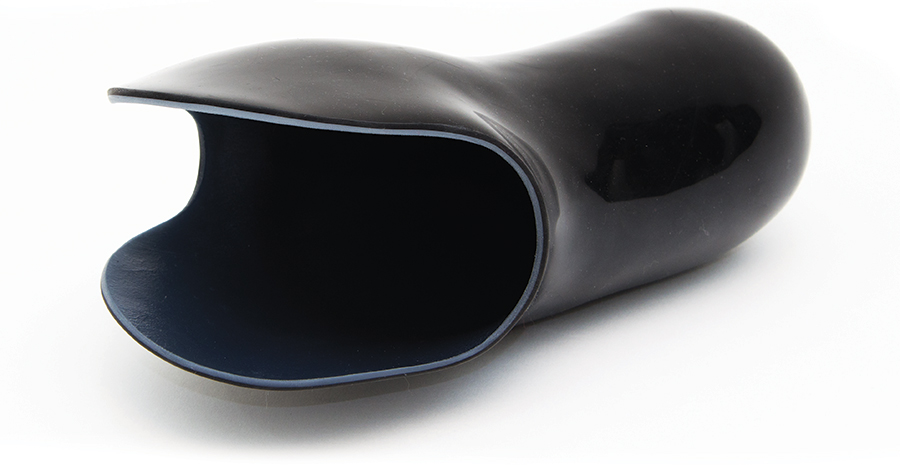
I was surprised to learn that performance plastics provide inherent benefits over other materials in conveyor and processing equipment such as lightening components, dampening noise and protecting employees with transparent machine guards. Then there are the food and beverage specific benefits like FDA-compliant plastics. I never thought about detectable grade plastics’ role in helping to reduce contamination recalls by incorporating food-safe blue colorant, metal powders or X-ray detectable additives into the base polymer matrix. Particle sizes of detectable plastics as small as 2 mm cubes can generally be identified by metal or X-ray detection equipment (2), which, from a consumer point of view, is a comfort. A colleague casually shared that some food and beverage processors choose PEEK because it resists hydrolysis in hot water and steam environments and I didn’t even know chemical breakdown of compounds from steam exposure was an issue. There’s so much science behind these engineering plastics providing so many benefits all while weighing at least half that of comparable metal components (3). Learning more about how our food is made has been a fascinating experience.
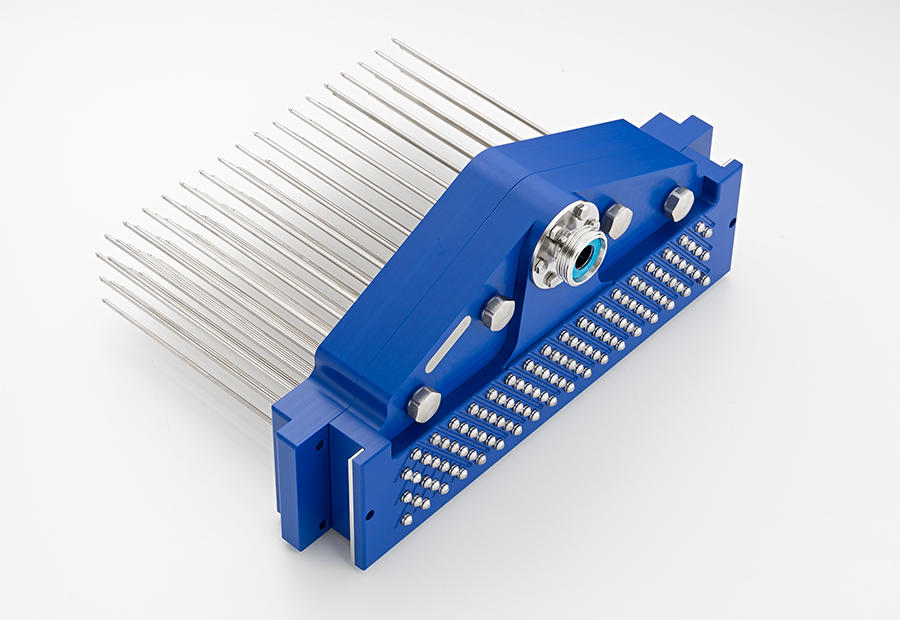
Once you realize how many of our daily tools and toys are made of plastic, it’s hard to maintain that anti-plastic mindset. The core problem is there have been so many quietly executed metal-to-plastic, wood-to-plastic and glass-to-plastic conversions that the public hasn’t recognized the change in materials. Consumers rarely think about light-weighting, friction and wear or weatherability of the items they’re using. The general public has become blind to plastic. It’s time those of us in performance plastics remove the blindfold. Here’s how:
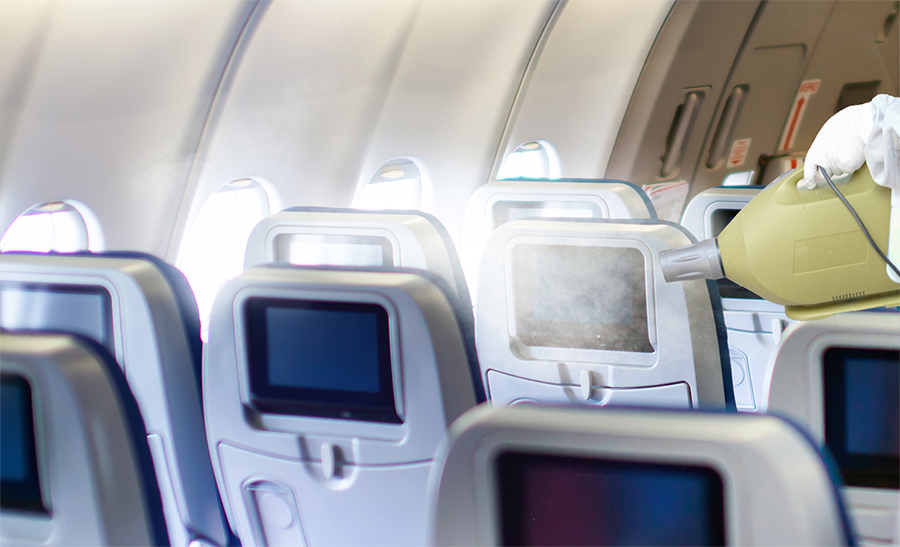
Second, we can connect with our communities. Participate in events, support educational programs and be ready and willing to have conversations about sustainable environmental and business practices. The public has been saturated in bad plastics press and in some cases has even turned a blind eye to considering plastic as a material option. Those of us in performance plastics know better than anyone the consequences of poor material selection. Take whatever opportunities you’re given to help people understand the importance of material selection and open their eyes to sustainable plastics possibilities.
Finally, listen to your emerging workforce. Millennials and Gen Z care deeply about environmental- and business-sustainable practices. We channel our energy into trying to create sustainable change and a better future. Clean energy, reducing our carbon footprint, recycling and reducing waste is top of mind for many of us and we’re looking to corporations to help us achieve those goals. Listen to our concerns about corporate responsibility, plastics’ role in sustainability and the importance of asking customers questions about material needs.
There are so many untapped opportunities for performance plastics. The up-and-coming generations are only going to look at them as viable material options if they’re smart, sustainable options. Help the general public overcome plastic blindness one conversation, one presentation and one opportunity at a time. Point out where performance plastic is used, why it was chosen as a solution and educate everyone about the bright future it can help create. Together we can see what plastic possibilities the future holds.
- Curbell Plastics. LDPE. Curbell Plastics. [Online] [Cited: 6 18, 2021.] https://www.curbellplastics.com/Research-Solutions/Materials/LDPE.
- Detectable Plastics for Food Processing Equipment. Curbell Plastics. [Online] 2021. [Cited: 6 18, 2021.] https://www.curbellplastics.com/Research-Solutions/Resources/Articles/Detectable-Plastics-for-Food-Processing-Equipment.
- Hechtel, Keith. Plastic Materials Proving to Be Good Fit for Aerospace Parts. Curbell Plastics. [Online] [Cited: 6 18, 2021.] https://www.curbellplastics.com/Research-Solutions/Resources/Articles/Plastic-Materials-Are-a-Good-Fit-for-Aerospace.