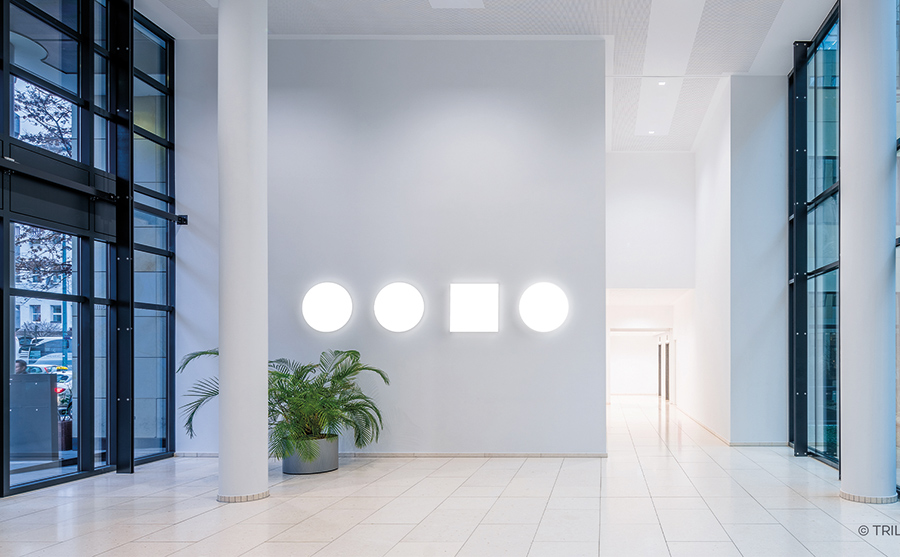
Olisq from TRILUX as a wall-mounted light: The lights of this series, with diffusers made of ACRYLITE®, spread a bright, homogeneous and glare-free light. © TRILUX.
When lighting public buildings and offices, the goal is to brighten rooms while using as little energy as possible and blending in with the architecture. Moreover, European construction projects are increasingly calling for lighting to comply with the Ecodesign Directive, which requires that lights can be repaired by replacing defective parts and that all components are reusable at the end of service life.
TRILUX, a provider of professional lighting solutions in Germany, integrated sustainability into the design of its Olisq series. ACRYLITE® from Röhm was chosen for the light diffuser due to its optical properties, longevity and recyclability. “ACRYLITE provides consistent quality and satisfies the increasingly stringent requirements placed on light quality, energy efficiency and sustainability when illuminating buildings,” according to Inga Keur, product manager wall and ceiling luminaires at TRILUX.
Olisq is designed for public buildings such as educational and health care facilities, production sites or office buildings. The series is comprised of three designs (round, square and rectangular) and nine sizes, making it easy to design entrances, rooms and corridors throughout the building. In the standard design, the tray is made of ACRYLITE 7H molding compound. TRILUX also produces a version made of impact modified ACRYLITE Resist zk40 for areas where increased impact resistance is appropriate, for example in school hallways and sports facilities, or as protection against vandalism in stairwells of parking garages.
In addition to the optical qualities, sustainability is important in lighting design. According to TRILUX, Olisq has a long service life of up to 100,000 hours and is extremely energy efficient with a luminous efficiency of up to 140 lm/W. Plus, its design has been optimized to use as few materials as possible: First, the lighting manufacturer extrudes sheets made of ACRYLITE and forms them into round, square and rectangular trays in a thermoplastic process. To prevent waste, all cuttings are ground up and returned to the production process. “The diffusers can contain up to 40 percent ground material; some of the ground PMMA comes from other TRILUX series,” explained Sebastian Dombrowski from project management manufacturing engineering at TRILUX.
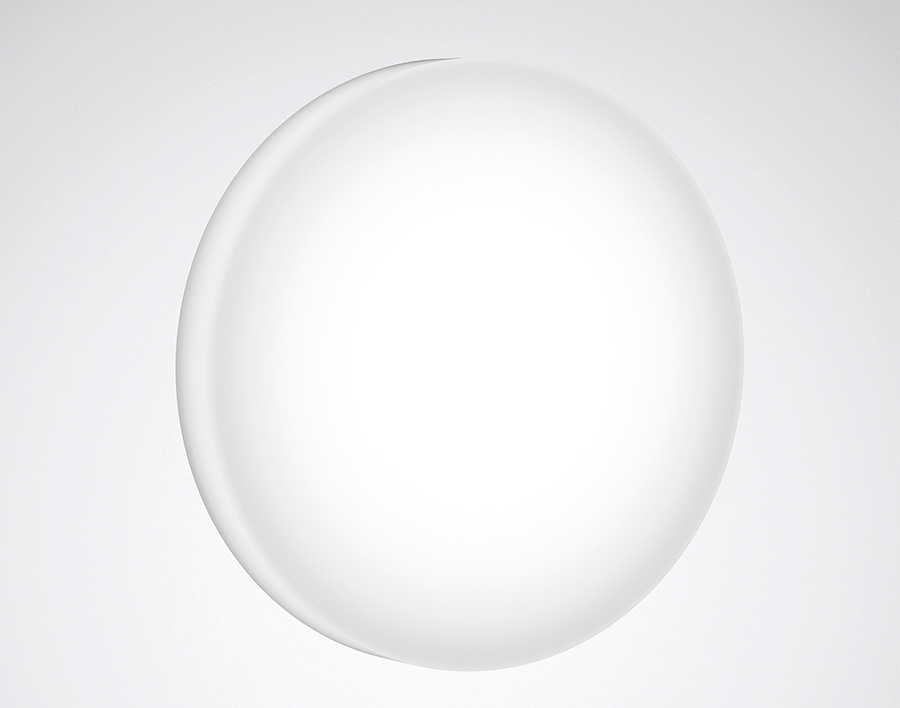
The lights in the Olisq series from TRILUX with trays made of ACRYLITE® – in this image, the round Olisq R – are energy efficient, easy to repair and feature a material-saving design. The tray contains up to 40 percent recycled ACRYLITE®. © TRILUX.
For Sven Schröbel, head of global sustainability management in the molding compounds business unit at Röhm, this is an example of plastics’ potential in the circular economy. “ACRYLITE is sustainable by design. Firstly, because of its longevity in use. And secondly because it is fully recyclable — with virtually the same product quality. This is underscored by the high share of recycled material in sophisticated optical components, such as the diffuser of the Olisq luminaire.”
“We have already sold millions of luminaires from previous models of the Olisq series over the years, all with trays made of ACRYLITE, so there is huge untapped recycling potential here,” Dombrowski said. When developing the new series, the designers added a feature to make them more user-friendly: Because the drilling and feed points match, it is possible to replace the older lights with contemporary Olisq lights without the need to drill new holes or lay new cables.
Olisq itself is sustainable due to the ease with which it can be maintained and repaired: All parts can be mounted, removed and replaced individually without any tools. “And, at the end of its product life cycle, all its components can be separated with other same-type materials and fed to the corresponding materials cycles. ACRYLITE is easy to recycle,” Keur emphasized. As such, Olisq not only complies with the Ecodesign Directive and the eligibility requirements — it also provides the user with a solution that remains cost efficient in the long term. www.acrylite.co.
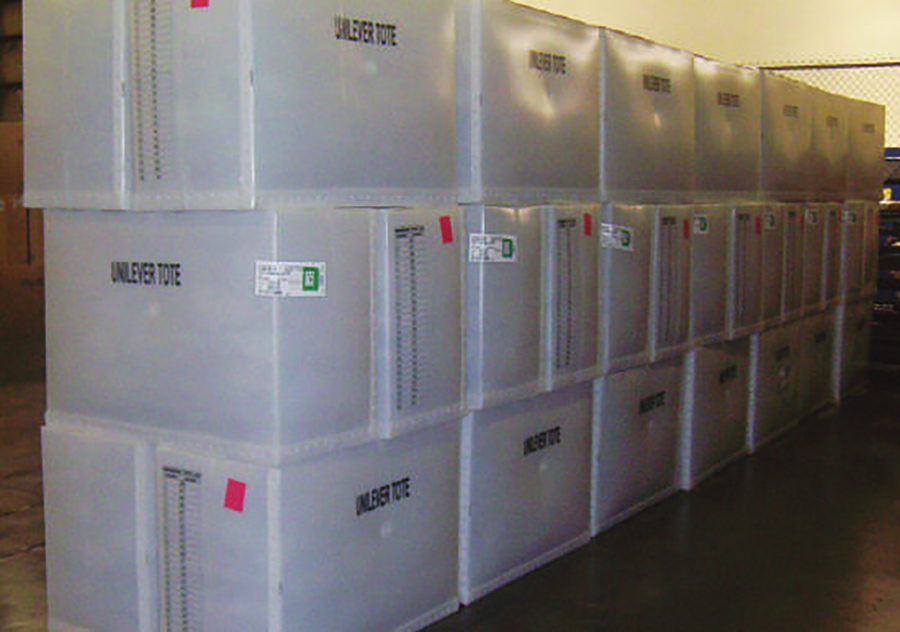
A multi-national food manufacturer was experiencing disruptions in its automated manufacturing system. The corrugated paper boxes used to send empty bottles down the line were jamming the machines and causing the line to shut down. The company needed a more durable solution that could withstand the moisture-rich environment and be reusable. They looked to Liberty Plastics, Inc. for a custom solution that would improve on-time production and deliver measurable savings long term.
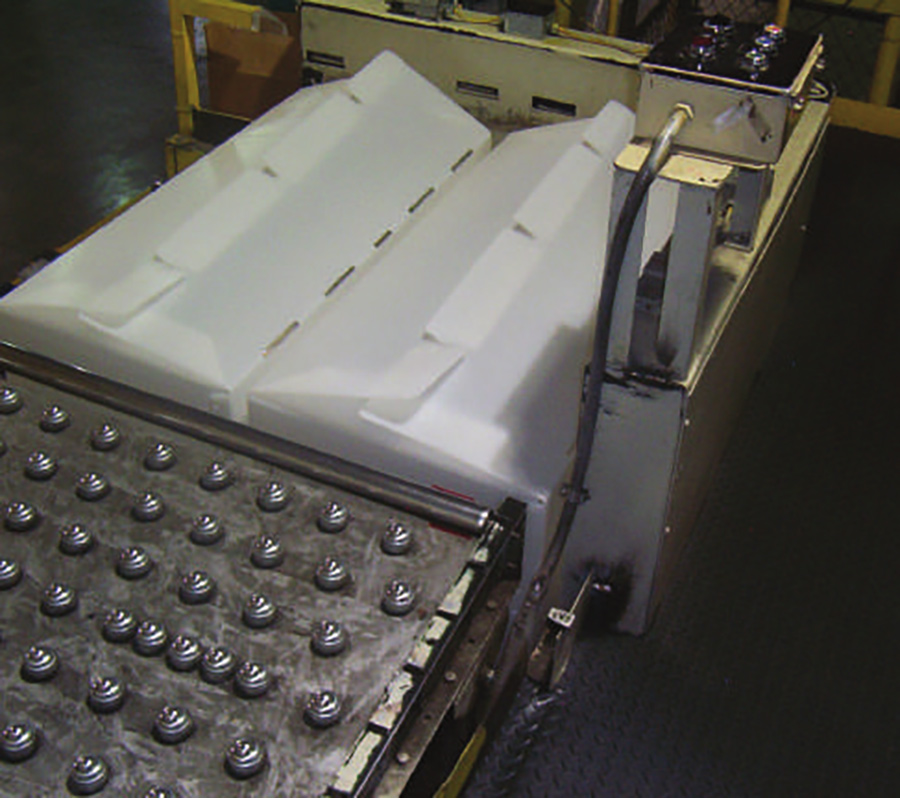
The challenge was to find a new, more durable solution that could withstand 50 turns and deliver measurable improvement to on-time production and costs over time. The solution had to:
- Store flat and quickly pop into shape
- Be made from a material that could withstand wet environments
- Be handled by automated machines
- Withstand 50 cycle turns
- Be made from a recyclable material
The reusable packaging solution developed by Liberty Plastics, Inc. was made from high density polyethylene (HDPE) corrugated material. It achieved 80+ turns. The HDPE corrugated material provided the strength, rigidity, resistance to moisture and durability the customer required. The packaging design uses no glues or staples and is 100 percent recyclable. It features:
- Lifespan of more than 80 turns
- Interior arm and bottom tray design
- Chart printed on side to measure turns
- HDPE corrugated to withstand moisture
- Collapsible design lies flat
The solution exceeded expectations and cost savings. www.libertyplastics.com.
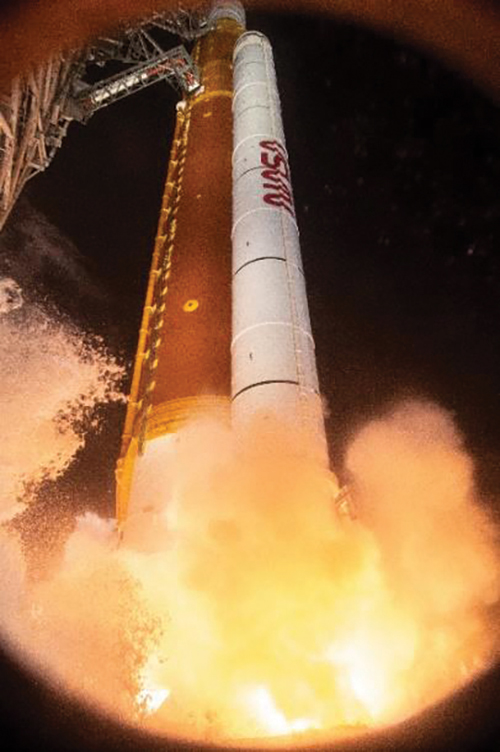
Arkema was selected to protect NASA’s iconic logo on the Artemis 1 Space Launch System (SLS). The coating is powered by Arkema’s Kynar Aquatec® PVDF latex and provides extreme durability to keep NASA’s red “worm” logo on the solid rocket boosters intact while soaring to space.
The historic Artemis 1 SLS lifted off from Kennedy Space Center in Florida, USA on November 16, 2022. It sent the Orion spacecraft approximately 1.3 million miles, orbiting the moon and returning to Earth on December 11. The SLS boosters featuring NASA’s red logo are the largest, most powerful solid propellant boosters ever built for flight. Visit www.youtube.com/watch?v=KJdBRgxsGJY to see a video of this project.
The waterborne clearcoat protecting the logo was created by Arkema’s partner, Acrymax® Technologies Inc. Kynar Aquatec PVDF latex enabled Acrymax Technologies to design a water-based protective coating with exceptional durability in low VOC, air-dry systems.
“We work hand-in-hand with partners like Acrymax Technologies to create custom solutions. Their ability to extend this partnership to NASA and develop a formulation strong enough to withstand the intensity of the most powerful rocket in the world is spectacular in many ways,” said Paul Lavallee, global market manager Kynar® Coatings at Arkema. “Kynar Aquatec PVDF latex is unique in that it delivers such world-leading performance in a user-friendly fashion. No baking or post-treatment is required.” www.arkema.com.