Fabrication in signage
igh-density polyethylene (HDPE) is one of the most versatile products in the performance plastics industry. HDPE is relatively stiff, non-porous, easily colorized and is easily fabricated with common saws and routers. Traditionally, it has been used in nearly endless applications in everything from cutting boards, boating trim, chemical tanks and outdoor furniture. More recently, HDPE has been carving out an innovative niche as the rising star in a new, rapidly growing market: Signage.
HDPE is a member of the polyethylene family. Polyethylene is the most widely used plastic in the world and comes in several grades that fall under the performance plastics umbrella. Common variations include low-density (LDPE), high-density (HDPE) and ultra-high molecular weight (UHMW). Each grade has unique strengths and characteristics, such as LDPE’s flexibility and corrosion resistance, UHMW’s low coefficient of friction and HDPE’s excellent strength-to-weight ratio. For comparison, the density, flexural modulus and Izod impact strength of HDPE are all between 40 percent and 150 percent improvements over polyvinyl chloride (PVC) panels.
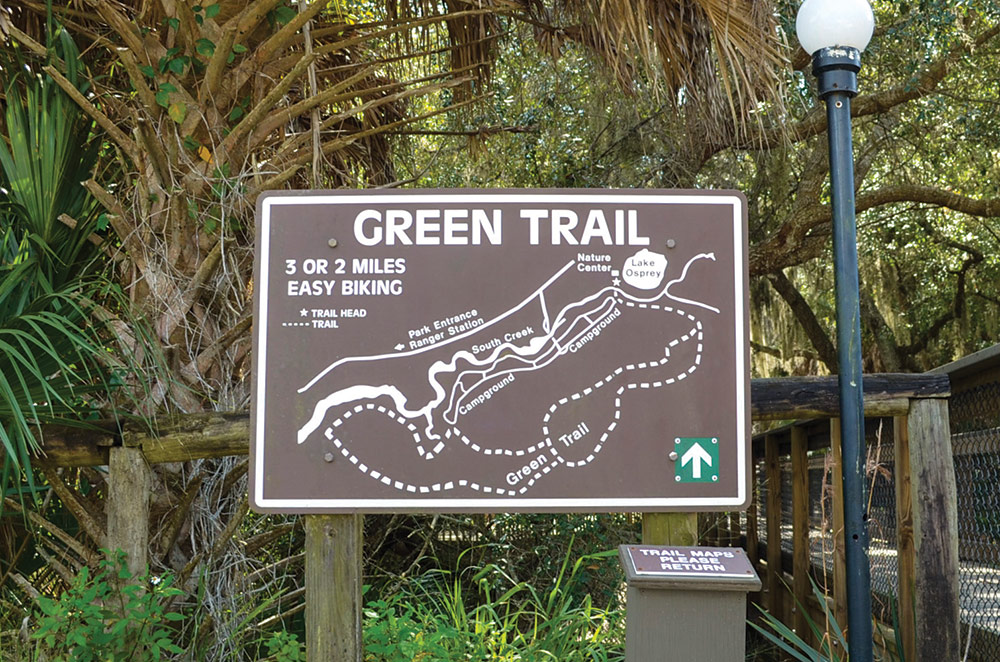
State Park Wayfinding Signs Made with King ColorCore® in brown-white-brown.
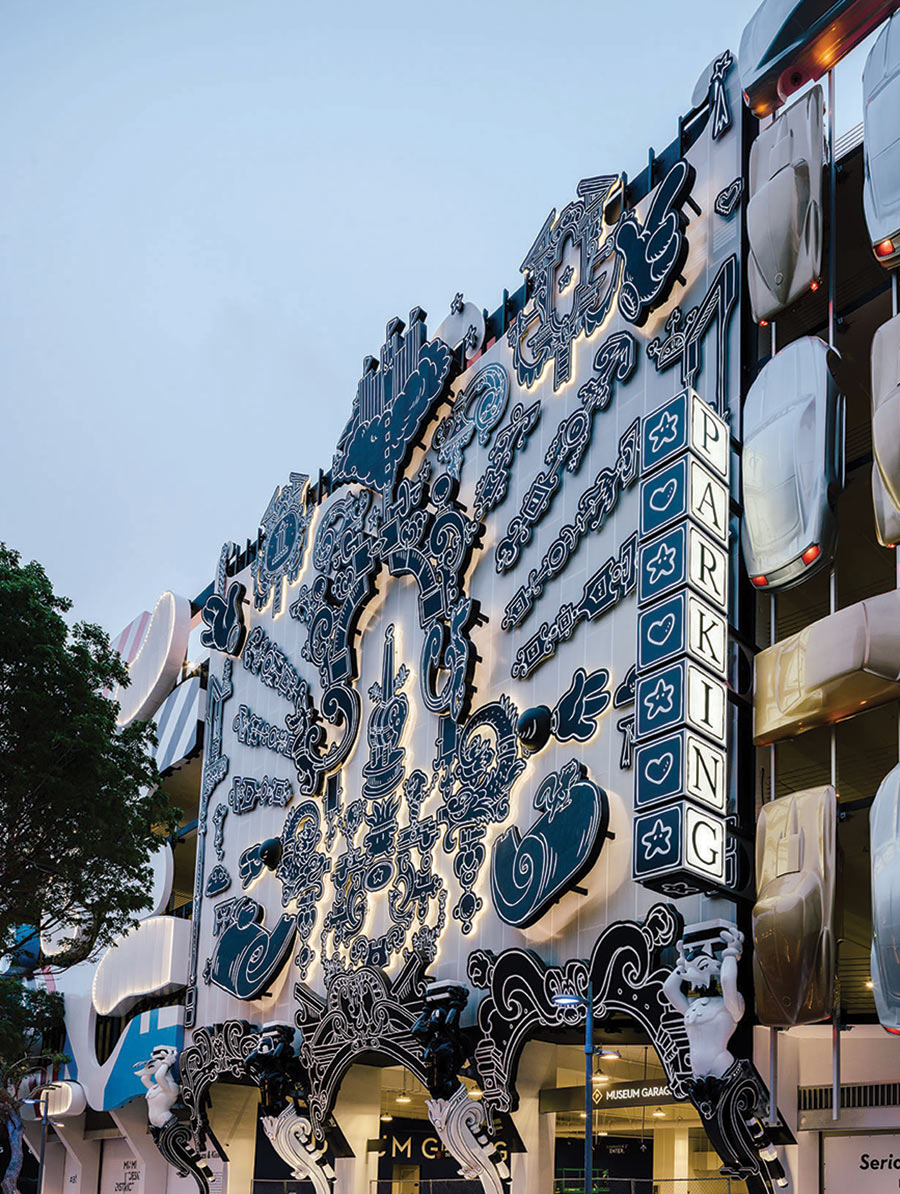
King Plastic Corporation HDPE Black and White Illustrations Made with King ColorCore®.
But what makes HDPE so uniquely great for signage? First and foremost is its ability to stand up to harsh conditions. Unlike competing materials such as wood, foamed PVC and laminates, HDPE will not rust or delaminate and will never need repainting. HDPE is a high-impact-resistant polymer, so it will be able to handle more abuse than conventional sign materials. It is non-porous, which means the material will not absorb water, dirt or grime that would penetrate and degrade other popular sign materials. It is highly resistant to typical sign-defacing agents such as spray paint and glue. If cleaning is necessary, almost anything can be removed with a simple power washer or, if necessary, gentle use of a nylon scrubber. HDPE is also chemically resistant. Most chemicals, except the harshest solvents and acids, will have little effect on the material.
In addition to its sturdiness, HDPE is very easy to colorize. Since it is extruded as a solid sheet, the chosen color will hold all the way through the material. It is available with additional UV protection packages to withstand consistent exposure to direct sunlight for many years without colors fading. Pantone matching is available with most manufacturers.
HDPE material is also easy to engrave and machine. Most common CNC tooling already used in the signage industry will work with HDPE, but it is often recommended that the fabricator use a high-quality solid carbide bit. Tool manufacturers will usually refer to HDPE material as a “soft plastic” and advertise their tooling respectively, but, Up-cut O-flute router bits are best.
While traditional solid-color HDPE sheets are easy to work with and stand the test of time against harsh conditions, there are a few things that could be improved when it comes to their use in the signage industry. The material is non-porous and resistant to almost all paints and glues. While these are excellent features in the fight against vandalism, they created difficult hurdles for creating stand-out signs. This is why a solution was created in the way of tri-layered coextruded sheets that contain multiple alternating colors. If you’re trying to picture what the tri-layered sheets look like, think of the caps like the black cookies on an Oreo and the core as the white frosting. Each cap is typically matte-finished and roughly .050″ thick. When machined, the vibrant exterior color caps contrast with a neutral interior core to make vibrant stand-out signage.
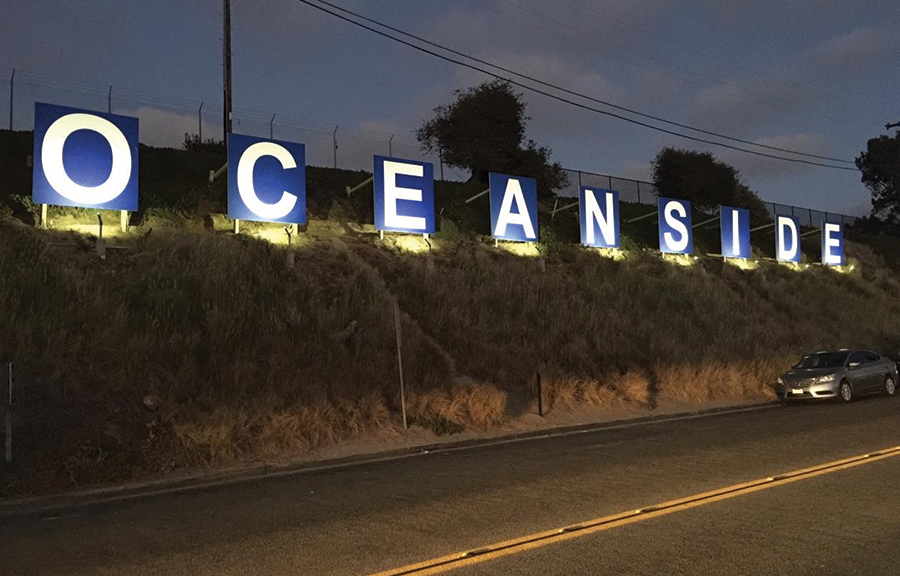
Oceanside Harbor Sign Made with King ColorCore® in blue-white-blue.
Like most architectural HDPE applications, the material really stands out versus the competition in areas of high moisture and UV exposure. Remember, HDPE sheets will not rot, delaminate or require repainting. It can get rained on in the spring, snowed on in the winter and get showered in mud, ice and sunlight with hardly a sign of wear. Some of the more obvious solutions for where to put tri-layered HDPE signs are places like golf courses, playgrounds, national parks and wayfinding signs on hiking trails. But the unique set of characteristics HDPE provides also makes it an excellent option for gyms and locker rooms, where chlorine, sweat and general humidity are often present. It is also a perfect option for applications such as branded picnic tables, carnival games, point-of-purchase (POP) displays, children’s furniture and colorful museum installations. When installing, remember to use corrosion-resistant mechanical fasteners — preferably stainless steel — and make sure to allow for expansion and contraction at a rate of roughly 1/32″ per 40-degree temperature change.
When it’s all said and done, tri-layered HDPE is the clear choice for anyone looking for high quality and durability in their signs. Customers everywhere are quickly learning that the costs associated with painting, repairing and replacing signs far outweigh the slightly increased cost of HDPE in a relatively short period of time. So, the next time you spot a faded sign in disrepair, remember: There is a better option available with an HDPE sheet.