uring the thermoforming process, heat is applied to a sheet of plastic to make it more workable so that it can be placed into or onto a mold and take on the desired shape. Thermoforming has evolved to incorporate a wide variety of sheet structures and materials. With thermoforming, performance plastics professionals can better deliver the sophisticated, tailor-made parts that customers expect and that also meet high industry standards.
There are some critical factors to consider when planning the thermoforming process for a production run. This article provides an overview when thermoforming polycarbonate for signage, skylight domes and other fabricated parts.
Vacuum forming — A fast and cost-effective process, which is ideal for high-volume projects. In this process, plastic sheets, placed in a mold frame, are heated to the point where they become flexible. As the sheets are pressed into the mold, a vacuum pulls the air out. This process is commonly used for creating formed sign faces.
Pressure forming — As with vacuum forming, the sheets are framed in a mold. With pressure forming, however, an additional part presses the sheet into the mold as the vacuum removes the air. This results in a more detailed product.
Matched mold forming — In this option, a two-sided mold forces the polycarbonate sheet to take on a specific shape. While this process is highly detailed, the tooling costs are higher due to the additional pieces required.
Hot line bending — During hot line bending, a narrow heated strip, such as a hot wire or an electric heater, is used to soften the length of the sheet. Heat can be applied to one or both sides of the polycarbonate sheet, depending on the thickness and duration. By using hot line bending properly, you can produce a product with almost no thickness loss at the bending area.
Free forming — Rather than using a mold, high air pressure is used to blow the heated polycarbonate sheets into a dome shape. The process is commonly used to create skylight domes and lighting fixtures.
Polycarbonate sheets with a thickness of 5.0 mm or less can easily be thermoformed using a one-sided heater machine. However, for demanding applications involving complex products or thick gauge polycarbonate sheets, using two-sided heated machines is recommended. Whether you use pressure molds, vacuum-forming or hot line bending, this recommendation applies.
With the matched mold forming process, products can be produced with almost no thickness loss, maintaining a sheet’s original strength and UV protection properties. However, in other thermoforming processes, such as vacuum forming, the sheet’s thickness may become uneven. For such cases, UV protection layer thickness and structural integrity are key considerations. In order to maintain a certain level of robustness and to avoid weak points, consider the complexity of the shape and the thickness reduction. Plan your product with all these considerations in mind and choose the right thickness for the processed sheet.
Solid polycarbonate sheets are a popular choice for thermoforming due to their excellent strength, clarity and durability. When thermoforming polycarbonate elements for use in an outdoor environment, it is crucial to use UV-protected sheets. Some polycarbonate sheets are only UV-protected on one side. Plan the thermoforming process so that the UV-protected side faces the source of UV radiation. Sheets with an especially thick UV protective layer can be used for demanding applications. This allows for higher draw ratios.
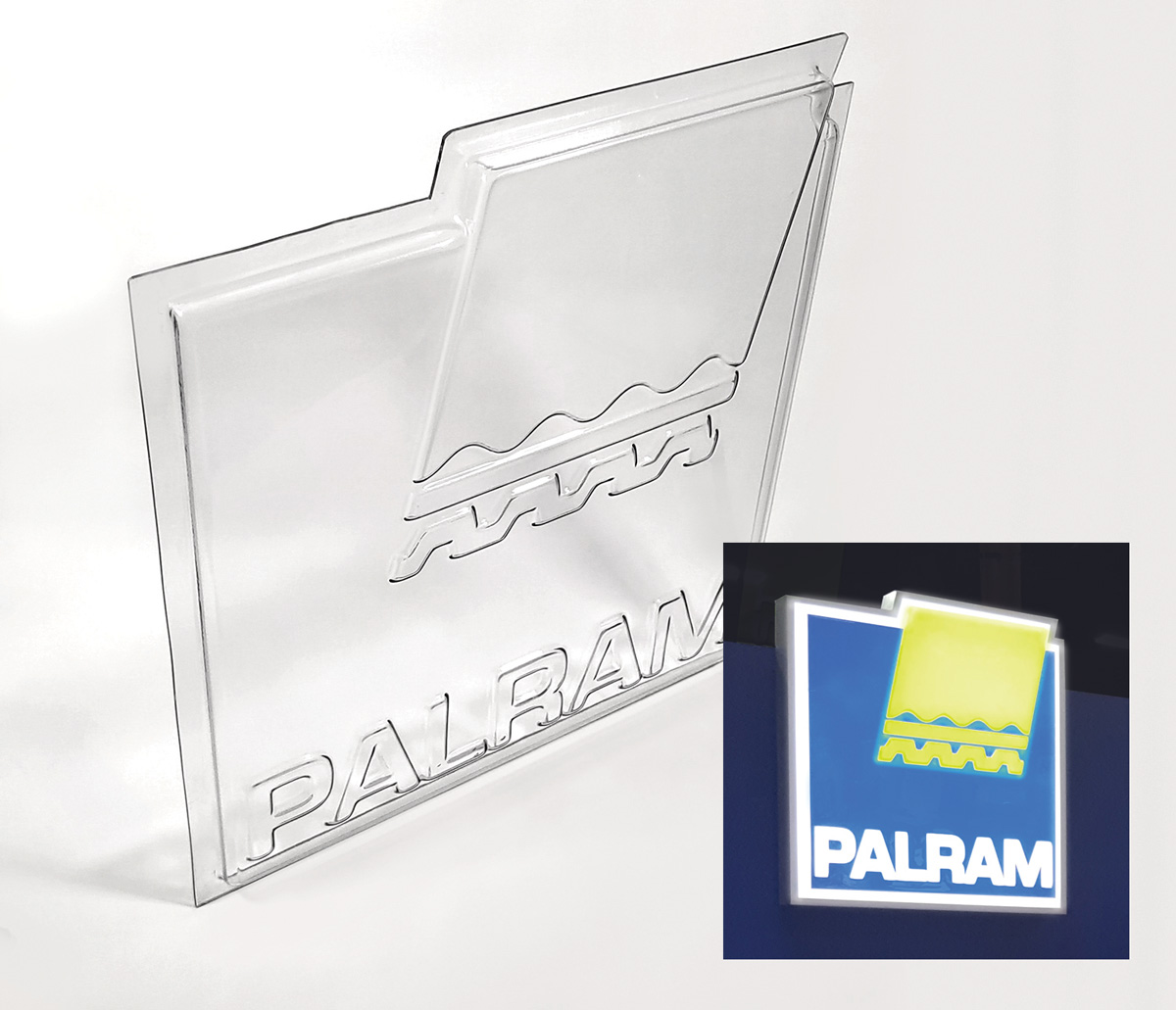
If bubbles appear in the thermoformed product, either the sheets were not properly pre-dried, or they were overheated. If this happens, you might try thermoforming at a lower temperature or pre-drying for a longer period of time or at a higher temperature. Pre-drying times may vary depending on local conditions. You can test whether your sheets are well dried and prepared by cutting a 50 mm x 50 mm slice of your pre-dried sheet and baking it at 356-374°F/180-190°C. After five minutes, if there are no bubbles, the sheet is dry. If bubbles do appear, the sheet still needs further pre-dying.
To avoid leaving marks on the fabricated product, make sure the film material is monochromatic and label-free.
Some masking films made from polyethylene (PE) may not be suitable for thermoforming. It is crucial to choose a brand that uses PE masking engineered for thermoforming. These maskings are pre-drying compatible and will peel off easily after the fabrication process has been completed.
This article is intended to provide the performance plastics professional with an overview of the types of thermoforming processes, as well as some considerations for successful thermoforming. With this knowledge, you will be better able to guide your customers to the appropriate thermoforming techniques relevant to their project and inform them of factors to take into consideration to make their projects a success.