Articles reporting on plastic products are prepared from information furnished by members of the IAPD and non-member magazine advertisers. The information provided is deemed reliable but is not verified. It should not be assumed that the publisher has reviewed or tested any of the products. For more information, contact companies by visiting their websites.

Arkema certifies bio-attributed acrylic monomers
Arkema announced the certification of a range of bio-attributed acrylic monomers using the mass balance approach. These monomers enable Arkema to start offering certified bio-attributed specialty acrylic additives and resins for a wide range of applications.
The launch of Arkema’s new range of bio-attributed acrylic monomers and specialty acrylic additives and resins, mass-balance certified under the International Sustainability and Carbon Certification-PLUS (ISCC+) framework, is a key milestone in the transition to a more renewable and lower carbon economy. The replacement of fossil feedstock by bio/bio-circular feedstock will support Arkema’s customers in achieving their climate plan goals by reducing their scope 3 greenhouse gas emissions.
“The development of these bio-attributed acrylic materials is an important step on the sustainable development roadmap of Arkema and its Coating Solutions segment,” said Hervé Castres Saint Martin, global group president acrylic monomers. “These innovative products deliver the same high quality and performance that our customers expect from us, while at the same time enabling them to lower their own carbon footprint.”
Arkema’s use of the mass balance approach in the manufacture of bio-attributed solutions complements the bio-based segregated polymers, resins and additives Arkema is already offering. These performance bio-based segregated solutions are, to name a few: Rilsan® and Pebax® Rnew® polyamide 11 advanced polymers, Sartomer® Sarbio UV-curing resins, Synaqua® alkyd emulsions, Crayvallac® and Coapur® rheology additives.
The mass balance chain of custody is designed to track the total amount of the content in scope through the production system and ensure an appropriate allocation of this content to the finished goods based on auditable bookkeeping. Property conservation principle is set to ensure that the total certified output does not exceed its original input and take into account the appropriate conversion losses and production/assembly ratios.
“Engaging in both complementary approaches of mass balance and physical segregation accelerates our innovation in renewable materials for our customers and partners, to help them achieve their own sustainable development targets,” said Richard Jenkins, senior vice president, Arkema coating solutions. “In line with Arkema’s newly reinforced commitment to the Paris Agreement, we are working diligently to reduce our environmental footprint while developing innovative materials for a more sustainable world.”
Arkema plants newly certified are Carling, France, for acrylic monomers; Genay, France, for specialty acrylic additives; and Zwickau, Germany, for specialty acrylic resins. In further development phases, the production of certified bio-attributed acrylic materials will extend in Europe and other regions. www.arkema.com.
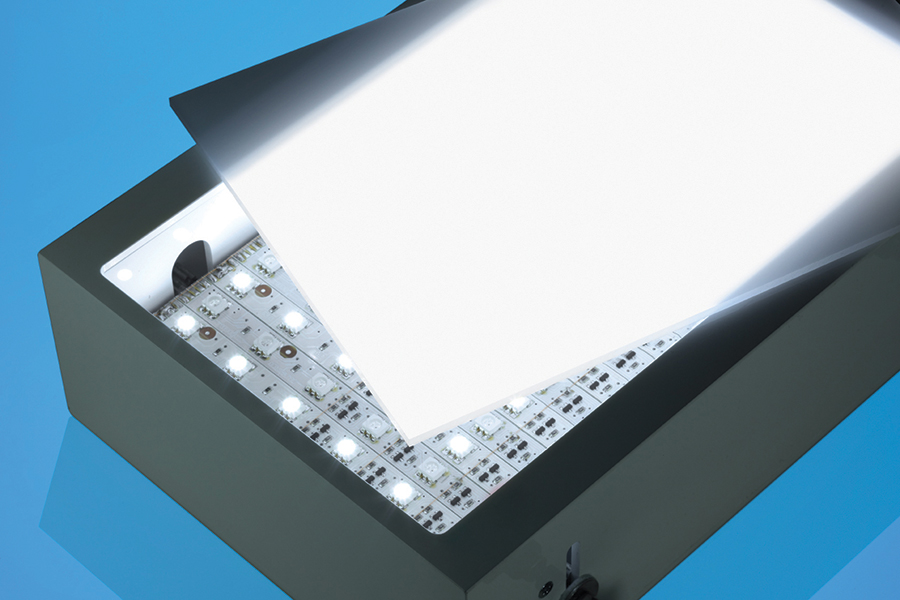
Exolon® DX
The use of many LEDs places the highest demands on homogeneous light diffusion and brightness, combined with wide or low light scattering. The Exolon® DX (Diffusion eXcellence) product family offers designers and lighting specialists the flexibility to implement sophisticated lighting concepts simply and systematically. Even with slim designs, hotspots disappear due to high light transmission and even brightness. Thanks to the synthesis of special highly transparent polycarbonate raw materials with scattering additives, the incident light color remains radiant even when emitted. It is a suitable lighting solution for adjustable cold/warm white and RGB-colored LEDs. The DX diffuser product family — Cool, Bright and High — comes by default with a matt and glossy surface. Optionally available types are:
- UV-resistant for outdoor use with a 10-year weather resistance warranty
- AR with hard coating that increases chemical resistance and protects against scratches and abrasion
- Flame-retardant product type FR for public transportation applications
- Specially flame-retardant products designated as TPA for special building requirements in the United Kingdom
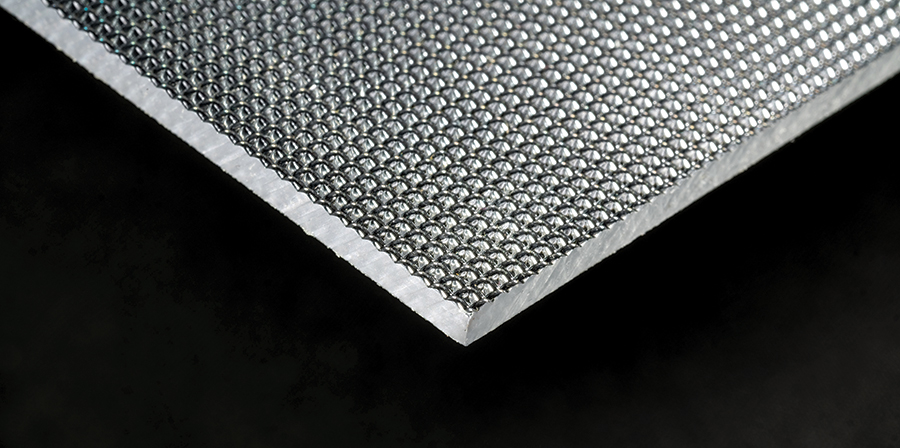
Exolon® SX Sharp
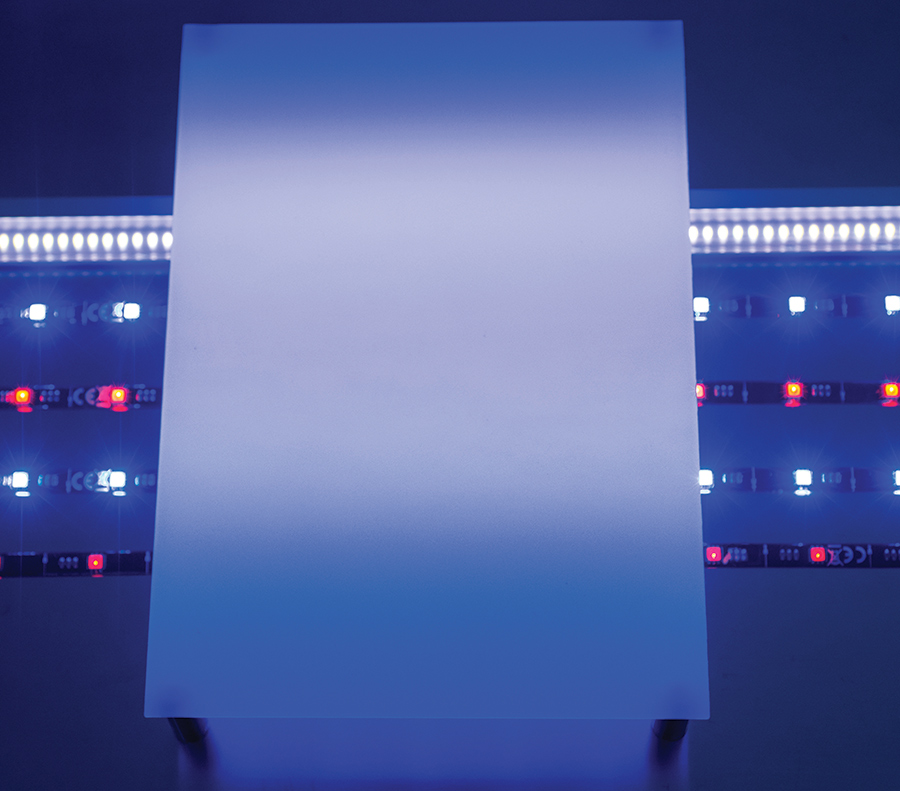
Exolon® UV AdLight
Functional and glare-free lighting and sleek designs are key requirements for the office design of the future. The Exolon Group has addressed these with their Exolon SX Sharp transparent polycarbonate solid sheet with a special microstructure finish applied on one side. This solution is suitable for indoor lighting and is used, for example, for lamp covers at the workplace. It also makes it possible to achieve an optimal UGR (Unified Glare Rating) value.
A strong brand needs a strong presence — not only in the media, but also live on site. The Exolon UV AdLight solid polycarbonate sheets are suitable for all types of backlit outdoor advertising that must be robust, low-maintenance and durable. The sheets offer a combination of design freedom and efficiency for this aspect of visual communication. They have a UV protective layer on both sides and a glossy and matte surface. It is easy to print onto the glossy side.
All products in the Exolon LED range have a fire classification. Easy installation, high breaking strength as protection against vandalism and with thermoforming properties make the polycarbonate sheet range suitable for use in various lighting conditions. www.exolongroup.com.
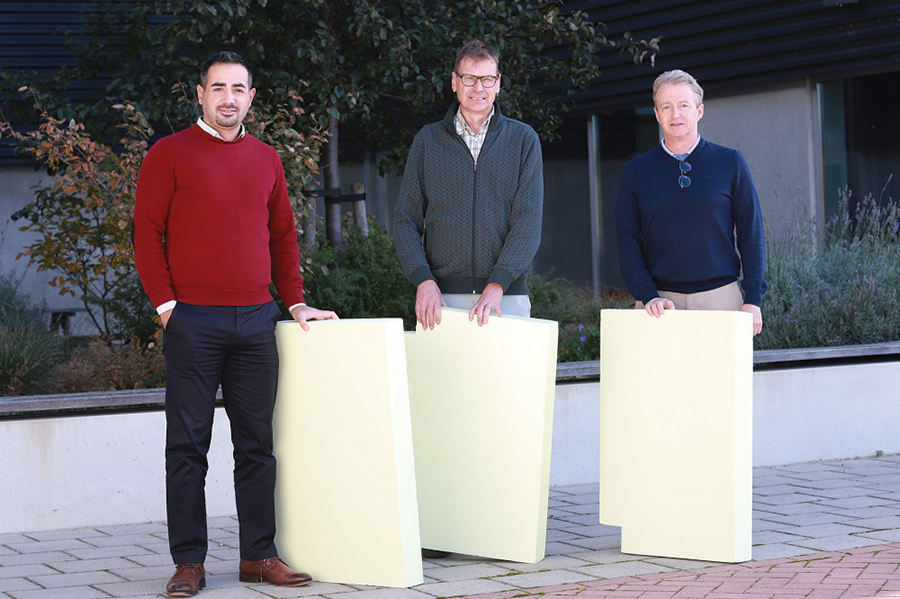
Trinseo announced the commercialization of its STYRON X-TECH™ 4660 Polystyrene Resins for Extruded Polystyrene (XPS). The material allows customers in the building and construction industry to reduce material consumption in foam insulation boards through Trinseo’s patented cross-linked polystyrene technology.
“Customers are able to lower foam insulation board density without compromising compression strength with our STYRON X-TECH 4660 material,” said Alain Minelli, business manager of copolymers and polystyrene. “With extruded polystyrene insulation board, its closed cell foam structure is responsible for providing the long-term durability and rigidity that is needed. Trinseo’s new material impacts this structure by introducing increased melt strength to enhance performance and allow for raw material and cost savings. This innovative material was developed by Trinseo’s polystyrene R&D team, and it truly sets a new industry standard.”
STYRON X-TECH 4660 Polystyrene Resin offers the same reliability and performance as previous resin formulations with greater sustainability advantage. It has been validated by several Trinseo partners who have been able to reduce weight of insulation board by approximately five percent, reducing carbon emissions by a corresponding amount.
Trinseo is an innovator and investor in polystyrene technologies, recognizing the material’s recyclability and circularity potential. STYRON X-TECH 4660 Polystyrene Resin is the latest sustainable innovation that serves a growing demand in the marketplace resulting from the European Green Deal, which was adopted by the European Commission to focus on sustainability strategies on the continent. www.trinseo.com.
Spartech Royalite® thermoplastic sheet provides permanent protection against electrostatic discharge (ESD). This product line features several material chemistries for manufacturing everything from shipping containers for sensitive software chips and aviation fuel caps to temporary floor material used during avionics assembly.
Spartech’s most popular thermoplastic ESD sheet, Royalite R63, is an ABS/PVC product that is both electrically conductive and fire rated. Containers made from Royalite R63 thermoplastic sheet provides permanent static protection and the dimensional stability typical of ABS plastics required for today’s robotic material handling systems. It is widely used for applications where dissipation of electrostatic charge is critical and provides excellent ESD protection to sensitive devices during manufacture, assembly and storage.
Royalite R63 combines high stiffness and abrasion resistance with excellent thermoformability and meets the minimum static decay requirements outlined in MIL-B-81705C and NFPA Code 99 specifications. It is recognized under the component program of Underwriters Laboratories, Inc. with a classification of 94V-1 at 0.066″.
In addition to Royalite R63, other available options include Royalite R632 thermoplastic ESD sheet which is both electrically conductive and UL® listed, Royalite R64 conductive sheet is a high molecular weight high density polyethylene for excellent thermoformability, Royalite R637 which is both an anti-static and high impact polystyrene sheet, Royalite R607 is an internal anti-stat applied to PETG rolls and Royalite R608 which is a topical anti-stat applied to PETG rolls with many uses such as electronics packaging for controlling static build-up and where clarity needs to be maintained.
Royalite is available in several thermoformable thermoplastic ESD material chemistries, depending upon the specific application, and can be specifically designed to comply with FDA Food Additive Regulation 21CFR177.1640 for rubber modified polystyrene. In most cases, using conventional plastic fabricating tools, it is possible to machine, saw, drill, rout and grind this rigid sheet material. www.spartech.com.
Braskem announced a project to evaluate an investment in producing carbon negative bio-based polypropylene (PP) in the United States. The project would use Braskem’s proprietary technology to convert bioethanol into physically segregated bio-based polypropylene. Braskem is exploring partnership opportunities for this project with several clients, brand owners and suppliers.
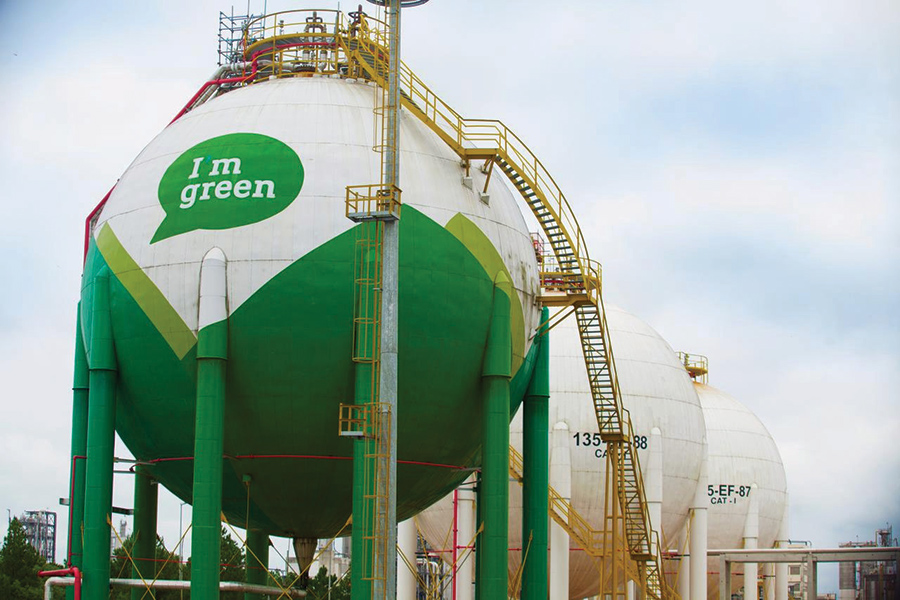
Braskem America CEO Mark Nikolich commented, “Building on our core technology and market leadership, we are actively evaluating a project to produce the world’s first bio-based polypropylene on an industrial scale to support our ambitious sustainability objectives and deliver tangible solutions to our clients. As an established leader in the innovation and production of bio-based materials, we have seen the demand for Braskem’s bio-based materials grow significantly since our initial product launches. This new U.S.-based project would not only serve a growing market for sustainable solutions but also reduce Braskem’s reliance on fossil feedstock. Expanding our portfolio to include bio-based PP supports Braskem’s goal of 1 MM tons of biopolymers capacity by 2030 and becoming carbon neutral by 2050.”
The United States is home to the largest ethanol industry production in the world and consists of ample technology, infrastructure and supply availability for a project in the polymers’ value chain. Braskem’s bio-based PP would be a drop-in solution that has the same technical properties and recyclability found today in Braskem’s current PP portfolio, with the additional benefit of a negative carbon footprint. Braskem’s bio-based PP would address brand owners’ and OEMs’ transition to a more sustainable future.
The company’s ambition is to be among the global leaders in greenhouse gas (GHG) emissions reduction and a key player in carbon capture through the production of materials with renewable, biobased raw materials. By 2030, they seek to reduce scope 1 and 2 GHG emissions by 15 percent and to achieve carbon neutrality by 2050. www.braskem.com/usa.