t’s no secret that the number of choices can be overwhelming to even the most educated consumers. Even those looking to select a substrate for their signage needs can easily fall into choice paralysis as there are numerous options. Sign makers can choose from acrylic, polycarbonate, corrugated polypropylene, polyvinyl chloride (PVC), aluminum and more, but the fact is that not all these materials are suitable for cost-effective, quality signage solutions.
However, acrylic has proved its worth to many sign manufacturers in creating quality sign faces over time. Other materials may not be weatherable, have undesirable surfaces and/or are limited by color or opacity. Below are a few points to consider when choosing an acrylic substrate for cost-effective signage.
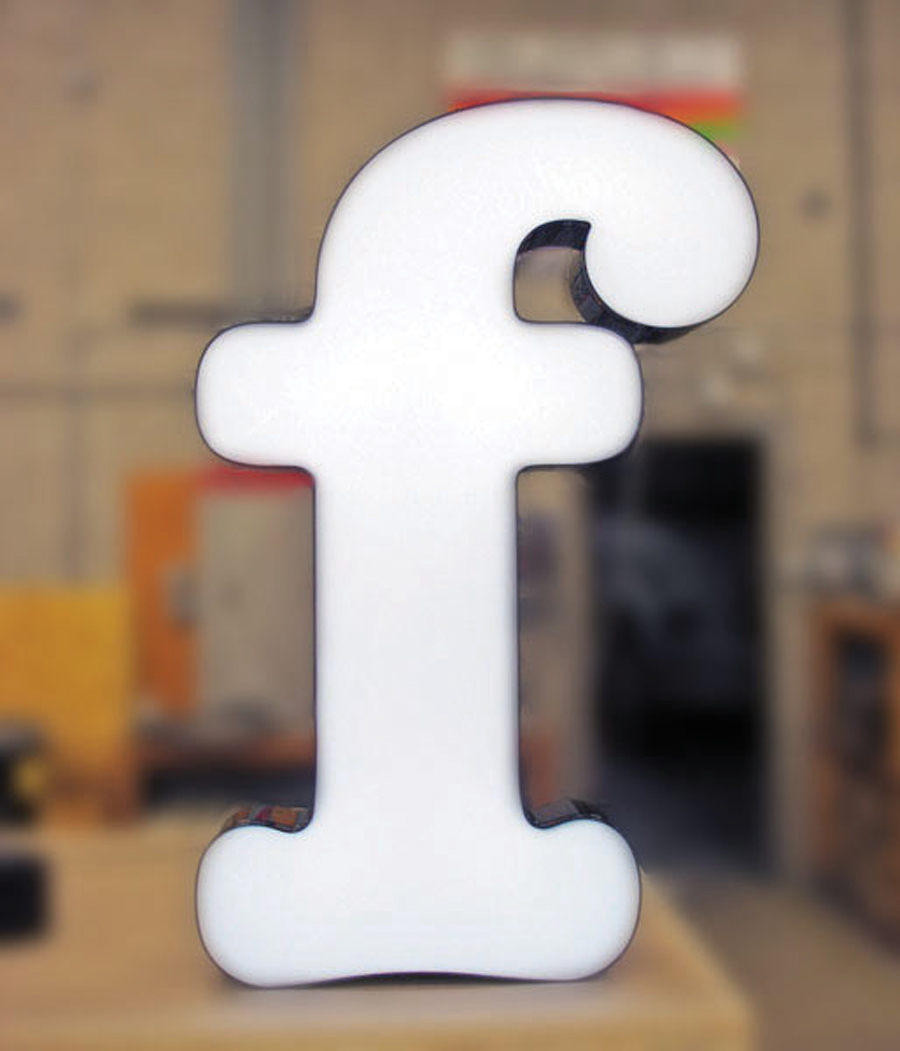
For thermoformed signs, there are some significant differences in material properties to consider. On average, acrylic can heat and form twice as fast as other substrates. Unlike other substrates that require heating to temperatures as high as 350°F/176°C, impact modified acrylic can thermoform at lower temperatures — even as low as 270°F/132°C, reducing cycle times by half in some cases, with lower energy costs. Cell cast and continuous cast acrylic are heated to slightly higher temperatures than extruded acrylic (but less than polycarbonate) and have a higher melt strength at thermoforming temperature while extruded acrylic, with its lower melt strength, provides higher part definition.
Sign makers considering making the switch to acrylic from materials that require higher heat temperatures will likely have no issues, as their heaters should be able to drop to the appropriate lower temperatures that work better and allow for quicker fabrication of acrylic. However, the opposite cannot always be said, as some conventional ovens may not be able to reach the high temperatures necessary to form those substrates. It’s always best to consult with experts to determine the exact requirements when dealing with each material.
Acrylic may also reduce thermoforming costs since drying time is rarely necessary. Other substrates may require pre-drying and will bubble if not dried properly, which can take many hours at lower temperatures and require extra ovens.
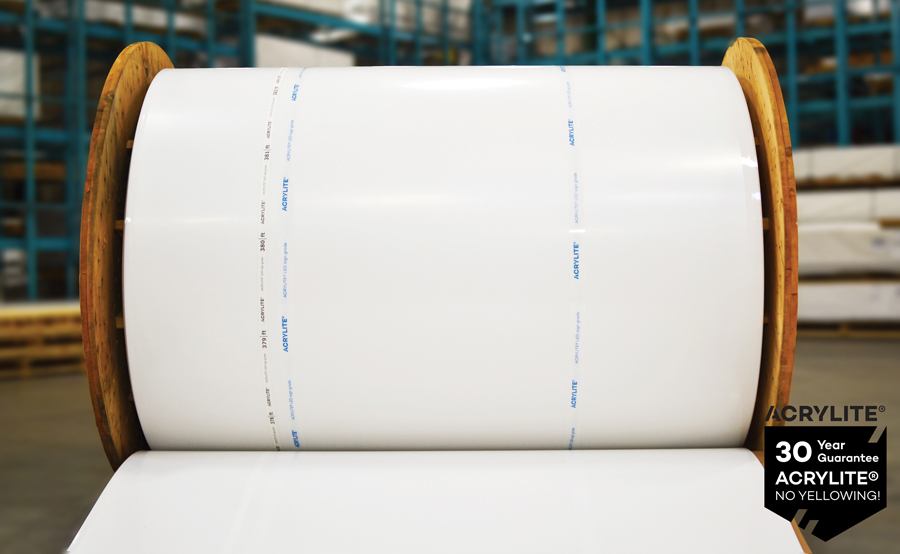
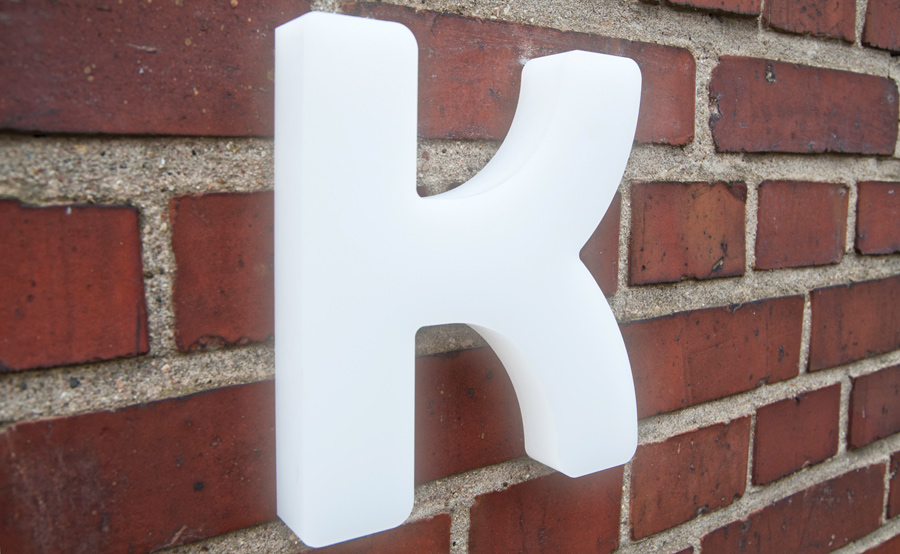
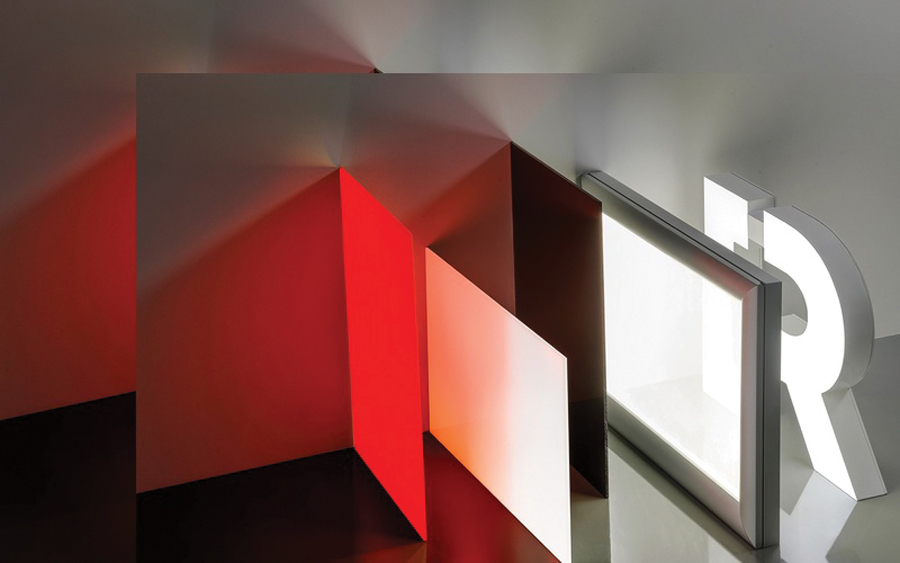
Set weatherability expectations
Unlike other substrates, acrylic will not show signs of weathering and deterioration in its impact strength. Often, other plastics yellow and become hazy after only a few years of UV exposure, even those that have been pre-treated with UV-protection. Acrylic is UV stable and, therefore, is much less susceptible to yellowing over time.
Replacing a piece of domestic acrylic produced by a manufacturer that guarantees its product is a simple process and requires no color matching as the old sheets are just as vibrant as the new. This quality keeps signs looking uniform and color consistent for many years.
Impact-modified acrylic comes in many different grades with various levels of protection against breakage. You can choose a high, medium or lower impact strength acrylic and save on material costs.