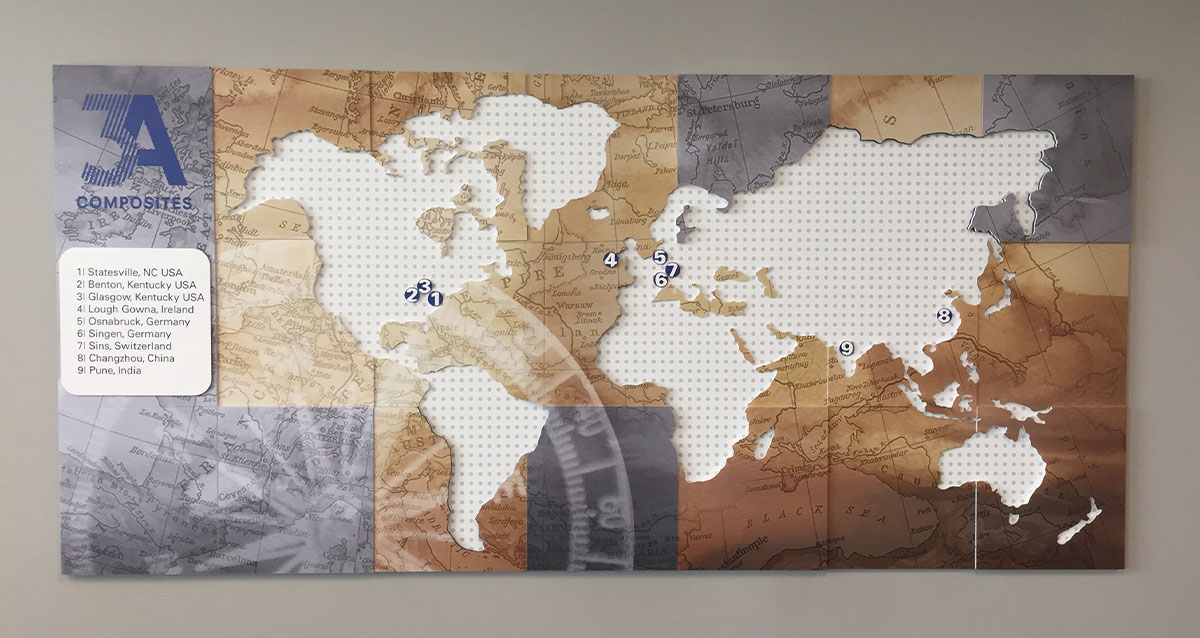
3A Composites USA, Inc. hired ACI Design Inc. to create and install graphic elements to decorate its lobby, business offices and product showroom after the company moved its headquarters to Davidson, NC, USA.
“Executives at 3A Composites wanted to demonstrate the company’s materials in any number of capacities including office and lobby décor as well as showroom graphics,” said Dain Richie, partner/designer, ACI Design. “They wanted to show the scope and range and creative possibilities of these materials using dimensional fabrication and digitally printed graphics.”
ACI Design was familiar with 3A Composites’ product lines, often turning to the company’s rigid substrates to create trade show exhibits, displays, corporate environments, museum exhibits and large-format graphics for clients.
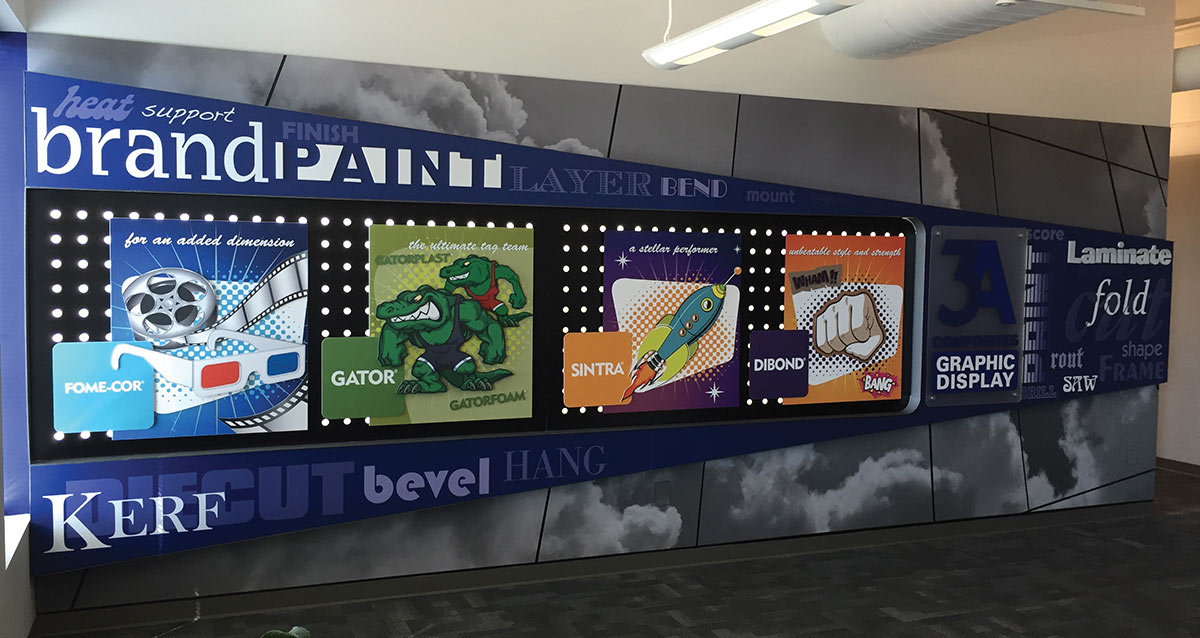
ACI Design used several rigid substrate brands from 3A Composites’ DIBOND®, SINTRA®, FOME-COR® and GATOR® Collections as well as ALUCOBOND® PLUS to create graphic displays for the company’s headquarters. Graphics were digitally direct printed with an AGFA Anapurna flatbed printer and AGFA UV-curable inks.
Showroom Graphics — ACI Design graphically highlighted and visually demonstrated material performance and fabrication techniques that can be used with FOME-COR, GATOR, SINTRA and DIBOND in a three-dimensional graphic created with these rigid substrates to cover a 23-foot wide by 9-foot tall wall space in the headquarters’ showroom. The background base layer of this large-scale graphic features a black-and-white image of clouds printed with white ink on 3 mm Black SINTRA and screwed to the wall. “We used the clouds in black and white to add texture to the display,” said Richie.
Covering the clouds is a wedge-shaped shadow box created from 3 mm DIBOND in ultramarine blue gloss that narrows horizontally and becomes thinner as the viewer moves to the right of the presentation. “We laid this big picture frame out in CAD software and used a kerf technique to cut a groove to bend the material to this shape,” said Richie.
An additional rectangular shadow box created from 3 mm DIBOND in Jet Black Gloss — and featuring circular cutouts to expose LED lighting — is positioned within the wedge to highlight product presentations printed on 3/16-inch GATORFOAM with bright white facers/white foam. “The lighting was used to ensure that these graphics popped off the wall,” said Richie.
ACI Design turned to DIBOND to create custom mounting studs and supports for this large-scale display. “The whole point of this display was to demonstrate all of the ways you can fabricate 3A Composites’ rigid substrates and to draw attention to those techniques with words,” said Richie.
Conference Room Map — ACI Design used a multitude of foam-centered board products from 3A Composites’ FOME-COR Collection to create a dimensionally layered map highlighting the company’s worldwide locations for display in the headquarters’ conference room. The 8-foot by 4-foot map presentation is mounted to a common base of 3 mm bright white SINTRA and features built-in square tiles of the company’s foam-centered boards.
Hallway Display — ACI Design decorated a 42-foot-long hallway with images of project applications created with rigid substrates from the FOME-COR, GATOR, SINTRA and DIBOND Collections as well as ALUCOBOND PLUS. ACI Design created a series of interlocking open picture frames for displaying application photos from 3 mm SINTRA in dark blue to produce “a museum-like timeline effect,” according to Richie. Photos were digitally direct printed to 3 mm bright white SINTRA. Product headers were fabricated from 3 mm DIBOND in BUTLERFINISH® copper layered with product names routed from 3 mm bright white SINTRA. The hallway display features more than 800 components that were installed with magnets to allow for easy updating.
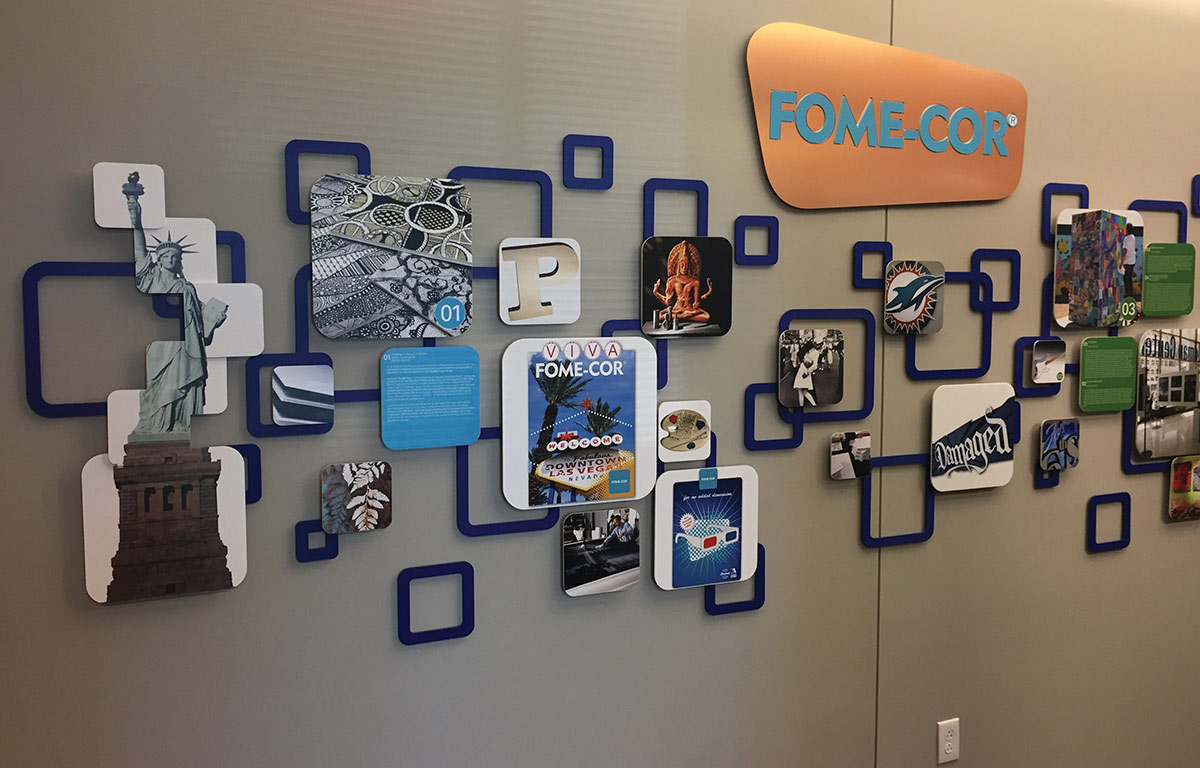
Office Décor — A total of 38 project application images were printed on 3 mm bright white SINTRA to display in pairs in 19 business offices. ACI Design created custom frames from 4 mm ALUCOBOND PLUS in rustic walnut from The Natural Collection Woodgrain Series. Both vertical and horizontal frames were created with ALUCOBOND PLUS, which was grooved to accommodate images that can be easily updated. The custom frames were mounted to the wall with decorative aluminum standoffs.
Lobby Logos — ACI Design created two LED back-lit box designs with 3 mm DIBOND to display the 3A Composites’ logo in the headquarters’ lobby entrance. “We basically used a box approach folding it out of DIBOND,” said Richie. “The inner face is white with a lid that goes over it made out of blue DIBOND.”
“It was such a fun project to complete with 3A Composites’ substrates,” said Richie. “It was a wonderful opportunity to create a custom design and deliver it from engineering through installation.” www.3acompositesusa.com.
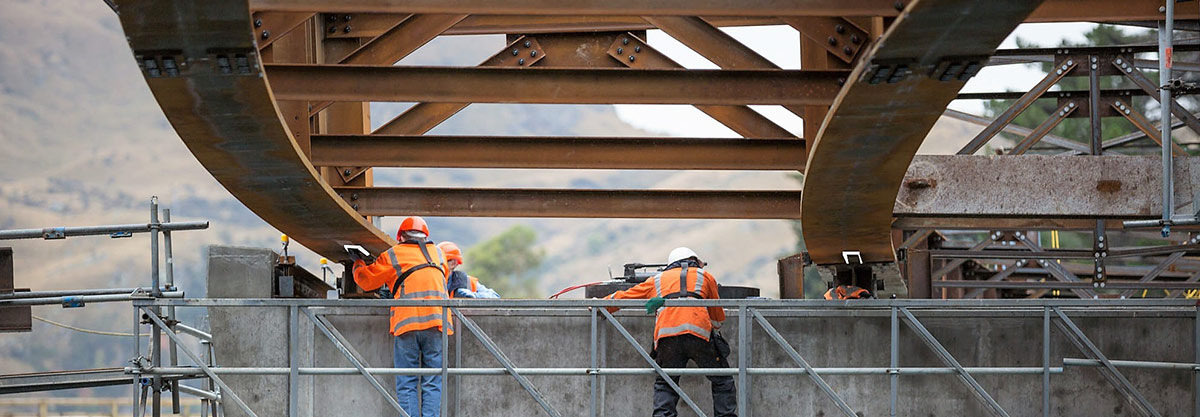
When you are hydraulically jacking a 252-meter bridge over the Kawerau Gorge, south of Queenstown, New Zealand, you want the least amount of friction possible. McConnell Dowell, an infrastructure construction company, approached IAPD distributor Supply Services looking for a performance plastic material that could handle the high mechanical loading and pressure of 20MPa (approx. ~2900 PSI) with a very low coefficient of friction. They wanted to hand feed this material as the bridge was jacked out to remove metal-on-metal friction.
The engineers in the Auckland, New Zealand branch of Supply Services selected TECAPET TF (PET) from Ensinger GmbH. The TECAPET TF can be seen in the photos as the white material between the support beams and the bridge.
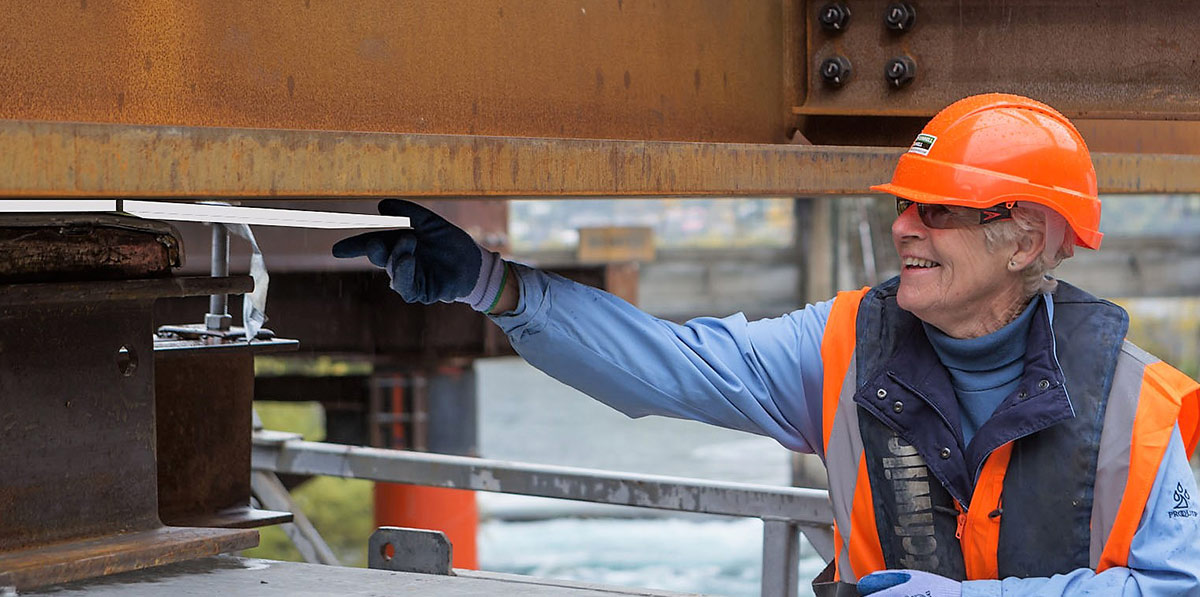
Ensinger TECAPET PET is a polyester that offers hardness, rigidity and strength with exceptional sliding and wear capabilities. TECAPET PET is available as an amorphous or semi crystalline thermoplastic. Due to its good creep strength, low moisture absorption and dimensional stability, TECAPET PET is well suited for applications where complex parts and the highest requirements regarding dimensional accuracy and surface quality are required. The thermal properties of PET support good temperature stability as well as dimensional stability.
TECAPET TF PET is similar to standard TECAPET PET but modified with a solid lubricant such as PTFE to become TECAPET TF. TECAPET TF PET was selected as the material of choice for the Kawarau Falls Bridge project. With all the familiar properties of TECAPET PET, the addition of PTFE improves and enhances the wear characteristics of PET, which allows for excellent sliding properties and wear characteristics. It was the appropriate material for hydraulically jacking the Kawarau Falls Bridge out over a gorge to reduce as much friction as possible. www.supplyservices.co.nz.

Designed with the needs of experienced and professional players in mind, The Premiere Series by FootJoy features ESTANE® TRX TPU polymers from Lubrizol offering superior traction on wet and dry surfaces. ESTANE TRX TPU’s design flexibility helps ensure the successful molding of FootJoy’s (FJ) anti-channeling tread pattern VersaTrax+, engineered to provide total traction coverage for any angle, reducing slippage.
The VersaTrax+ outsole technology, first introduced in FJ Stratos™ spikeless golf shoe in the fall of 2020, uses multiple ESTANE TPU compounds to grip any surface — a harder TPU for better on-course grip and a softer TPU for traction on hard surfaces. VersaTrax+ provides the Premiere Series modern performance innovation, while staying true to its design.
“The VersaTrax+ outsole in the Premiere Series, made with Lubrizol ESTANE TPU solutions, is a premiere technology using our premiere material for a premiere line of shoes,” said Kenneth Kim, footwear market development manager, Lubrizol. “This new line is a nod to traditional golf designs blended with innovative technology to deliver performance and style for the experienced golfer.”
“We saw a terrific opportunity to completely reinvent the classically inspired golf shoe from the ground up,” said Chris Tobias, vice president, FJ Footwear. “And to accomplish that, we leveraged every ounce of innovation, as well as direct input from the world’s best players, to deliver next-level performance with a distinctly modern take on classic design.”
Lubrizol invented thermoplastic polyurethane (TPU) polymers more than 60 years ago and continues to deliver solutions to a wide range of industries from performance footwear and apparel to surface protection, consumer electronics, transportation, industrial specialties, bonding solutions and more. The customizable properties of TPU allow manufacturers to create smarter, helping reduce waste in manufacturing and providing durable, long-lasting, recyclable solutions that can help differentiate their products. www.lubrizol.com.
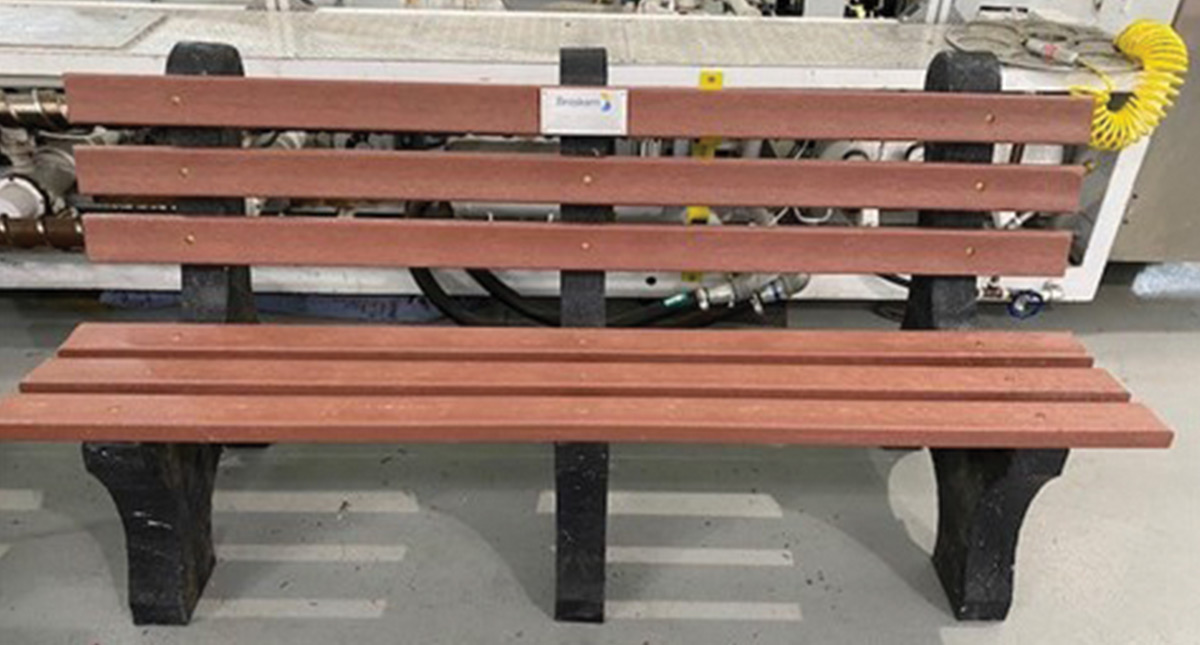
Braskem America, Inc. has donated durable benches and tables made from 100 percent recycled plastic to non-profits and other organizations in the local communities where the company operates. Braskem’s sustainability development strategy includes a strong focus on local development. As part of Braskem’s WeCARE Week, a global week dedicated to mobilizing team members to give back and volunteer in their local communities, some Braskem team members focused on efforts to promote recycling and reuse of plastics. Team members nominated organizations in their local communities that would benefit from receiving durable plastic furniture and the winning organizations were selected as a result of these nominations.
According to Brittany Darras, one of Braskem’s team members who works in the circular economy and sustainability area and oversees the volunteer program in the United States, "With the restrictions put into place due to the pandemic, our traditional ways of impacting our communities were limited in 2020; a creative idea brought forth was to donate durable furniture made from 100 percent recycled plastic to organizations that could benefit from additional seating. This furniture is an example of how recycled plastic can be transformed and used in valuable applications that benefit our communities. The more educated and aware our society is on the benefits of recycling, the more we can keep waste out of landfills."
The foundations that received donations include: Today’s Harbor for Children (La Porte, TX, USA), Bridge Over Troubled Waters (Pasadena, TX, USA), Stepping Stones Inc. (Huntington, WV, USA), Marcus Hook Borough (Philadelphia, PA, USA), Carnegie Science Center (Pittsburgh, PA, USA), Oakland Catholic High School (Pittsburgh, PA, USA) and Science Leadership Academy (Philadelphia, PA, USA).
Braskem is strongly committed to a world where nothing is wasted and everything is transformed. Braskem announced its commitment to a carbon neutral circular economy, with clearly stated targets for growing the company’s I’m green™ recycled products portfolio to sales of 300,000 tons by 2025 and 1 million tons by 2030. In 2020, Braskem became a founding member and funding partner of the Polypropylene Recycling Coalition, an initiative of The Recycling Partnership, to increase U.S. curbside recycling access for polypropylene and ensure PP is widely recovered and reused. Braskem is also a founding member of the Alliance to End Plastic Waste. www.braskem.com.
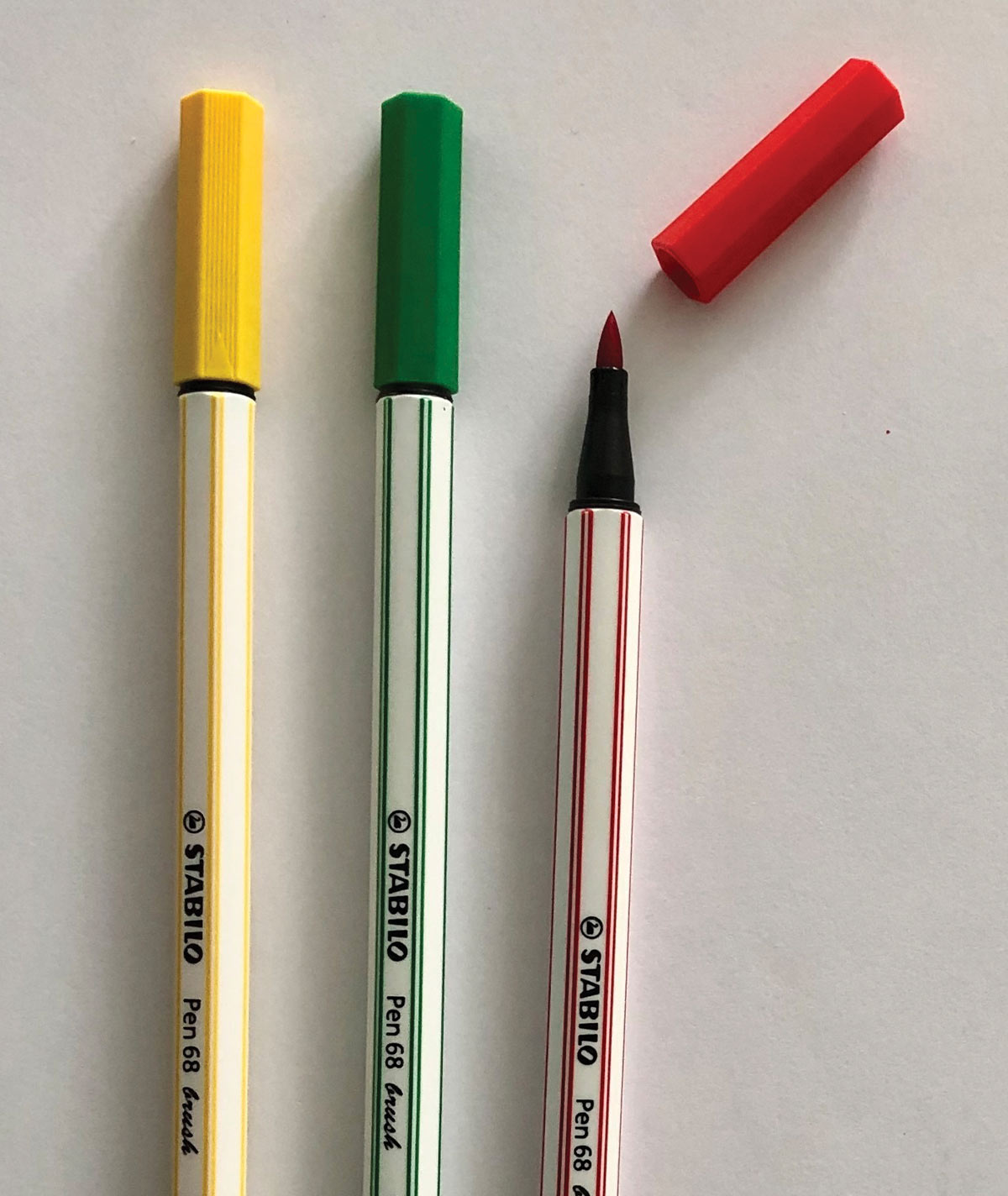
GEHR Plastics, Inc. has supplied their customer Schwan STABILO with polypropylene (PP) hexagonal tubes in various colors for their new product line: A fiber-tip pen with a flexible brush tip for use in a modern form of calligraphy known as brush lettering. This craft involves using a flexible brush pen to create individual letters or entire sentences using flowing, differently accented upward and downward strokes on the paper. The flexible brush tip makes the STABILO Pen 68 brush a useful tool for hobby artist and professionals alike. The challenge for GEHR was to exactly reproduce the available colors of the brush in the color of the double edge strip of the PP tube, as well as the close tolerances the tube was required to meet.
GEHR supplies extruded precision tubes for the writing instruments industry. These tubes permit the production of designs that are impossible to achieve with injection moulding processes. GEHR PP® is used most frequently due to its processing options. Depending on the individual requirements, different surface effects ranging can be achieved. GEHR has been producing the famous hexagonal tube for the classic orange fine line pen point 88 for STABILO for the past 50 years. www.gehr.com.
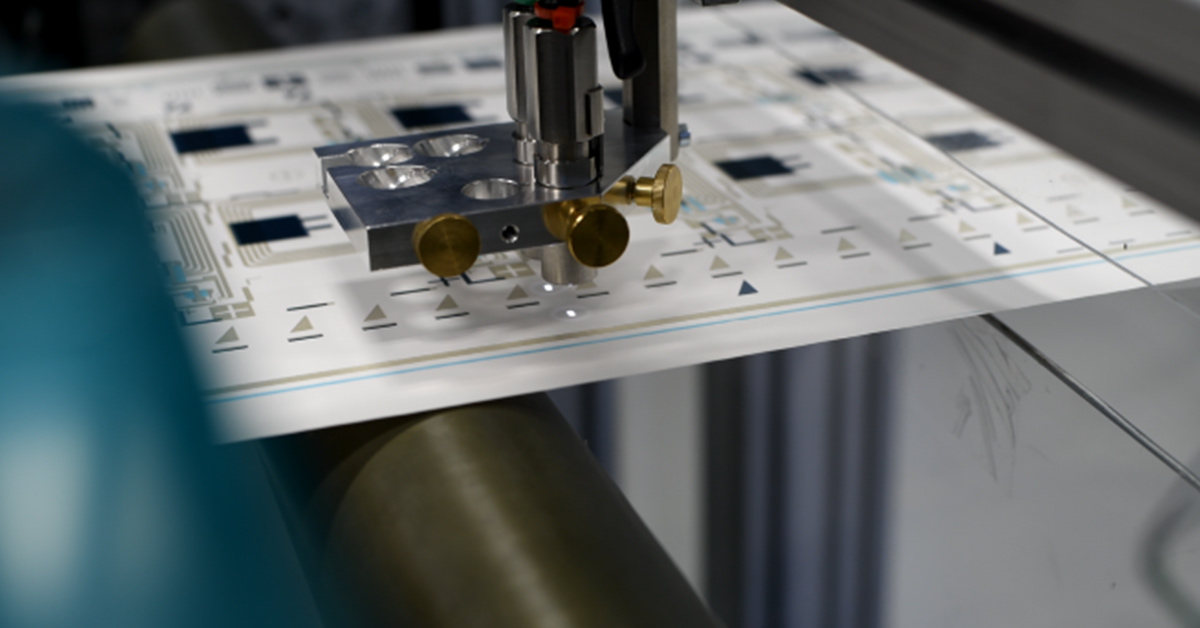
The SUPERSMART European project funded by the European Institute of Innovation and Technology (EIT) and coordinated by Arkema with 10 partners won the 2021 Organic Electronics Association competition award for the Best Publicly Funded Project Demonstrator. This project advances the emerging technology of paper printed organic electronics to the industrial phase. Two innovative demonstrators were designed and produced on a pilot scale:
A smart label including an impact sensor based on Arkema’s Piezotech® piezoelectric material and a smart counterfeit-proof label with conductive tracks and electrochromic displays directly printed on paper. The data detected on both components can be read via a smart phone app. Meanwhile, life cycle assessment (LCAs) and recycling studies have demonstrated the environmental benefit of these new solutions.
The smart impact sensor tag using piezotech material could be used:
- In packaging luxury goods, pharmaceutic and medical products to record their exposure to impact, fall or vibration during transit.
- For people’s care in hospital and homes, where the tag can be integrated under carpets, floor tiles or parquet floors to detect falls or abnormal movements of patients or the elderly.
- In vehicles to track accidents.
- In the military to detect falls and blast.
- In offices and shopping centers, to count people and detect their movements in order to adjust lighting, air-conditioning or heating.
Piezotech materials have been developed within Arkema’s electronics solutions innovation platform designed to deliver the growth of sustainable solutions in line with to the UNs’ SDG 9: “Build resilient infrastructure, promote inclusive sustainable industrialization and foster innovation.”
Fabrice Domingues Dos Santos, piezotech product development manager who coordinated the project, said, “The collaborative work within the framework of SUPERSMART and this recognition by the organic electronics community paves the way for a new sustainable electronics and a large number of new applications using our piezoelectric materials.” www.arkema.com.
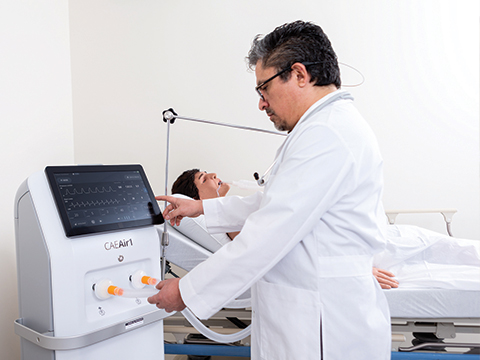
In April 2020, following the shutdown in response to the COVID-19 pandemic, CAE Healthcare responded to the Canadian government’s call for the production of 10,000 ventilators. CAE was known for producing simulation equipment for the medical and aviation industries, but they transformed into full-scale ventilator mass production.
Unlike other ventilator projects using existing designs, CAE opted to engineer and develop a new ventilator, the CAE Air1. It began as the size of a shoe box and was meant to be a portable unit before evolving into a high-end, intensive care ventilator unit measuring approximately four feet tall. Thermoformer Plastique Art accepted the challenge of producing the parts required for the machine.

As experts in the field, Plastique Art provided guidance on recommended materials and thermoforming processes. The project required medical-grade materials that were durable, chemical resistant and met the demand of certification from Health Canada. Plastique Art turned to KYDEX® Thermoplastics, knowing they were widely used in medical applications.
Using technical data and material testing information from SEKISUI KYDEX, Plastique Art was able to expedite the material choice with CAE. KYDEX Thermoplastics are durable, chemical resistant, inherently antimicrobial and available in a wide range of options for design. Ultimately, Plastique Art chose KYDEX T for the project.
Housing choices considered for the CAE Air1 ventilator included 3D printing, injection molding and sheet metal. However, when considering the urgency and volume of the project, Plastique Art knew thermoforming, specifically vacuum forming, was the best solution. 3D printed parts and sheet metal solutions are labor intensive to fabricate. They also require extensive finishing processes to seal, sand and paint to achieve the same level of aesthetics of thermoplastic material with in-mold color features.
Vacuum forming allows for shorter lead times to have material on hand for processing, shortening the production time for parts. Tools can be turned around in under two weeks, while pressure forming tools may take four to six. Once the sheet is formed, it only requires trimming and minimal assembly time for installation.
Final CAD files were received on April 20 and by April 30, Plastique Art finished parts for 11 CAE Air1 prototypes. Design adjustments were made through May. By June 16, the CAE Air1 ventilator was in its first round of certifications. By August 14, the second round of certifications was completed. On August 17, 142 days since the start of the project, mass production was under way. Under normal conditions, the average time for a medical device from conception to production typically takes at least 18 months.
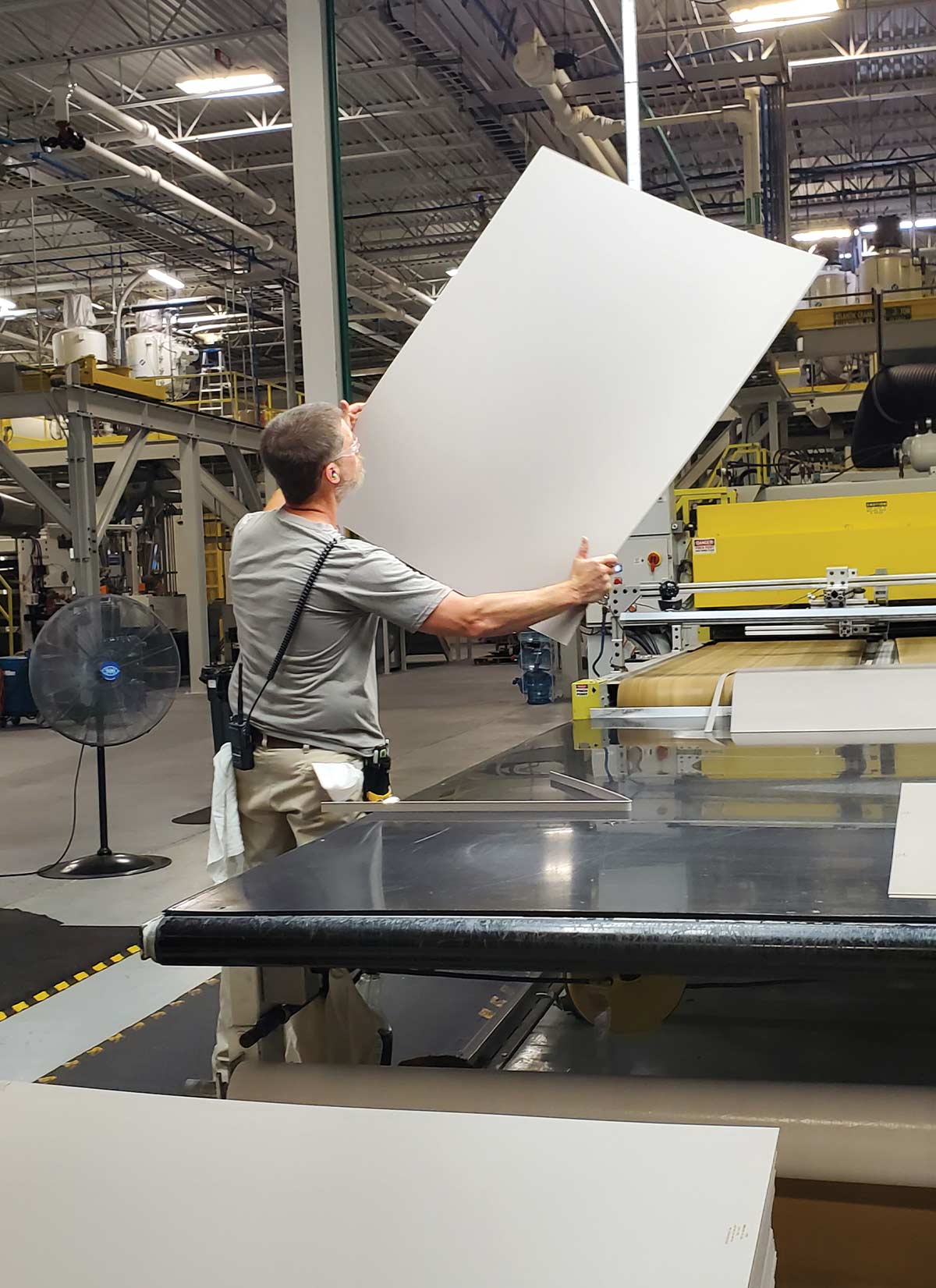
To achieve the goal of making 10,000 certified units in three months, production had to be scaled to maximum capacity. Plastique Art invested in a new thermoformer and expanded their shifts to include weekends for two months. This enabled them to meet the goal of parts for 1,100 units per week.
Using SEKISUI KYDEX’s Quick Response Manufacturing Model, 50,000 pounds of KYDEX Thermoplastics were delivered every week to Plastique Art. The standard lead time of four weeks for material was expedited to one week. The volume of KYDEX Thermoplastics was so high, Plastique Art had to secure additional warehouse space to house the pallets of material.
“It was a privilege to work with Plastique Art and CAE on this important application, and our team was excited to provide whatever support was needed. CAE and Plastique Art are real-life heroes for making this happen, from concept to fulfillment, in a ridiculously fast time, which ultimately saved people’s lives,” said Mark Denning, medical market business manager, SEKISUI KYDEX. Thanks to a dedicated supply chain working together to make this project a success, the last of the CAE Air1 ventilators were completed in December 2020. www.kydex.com.