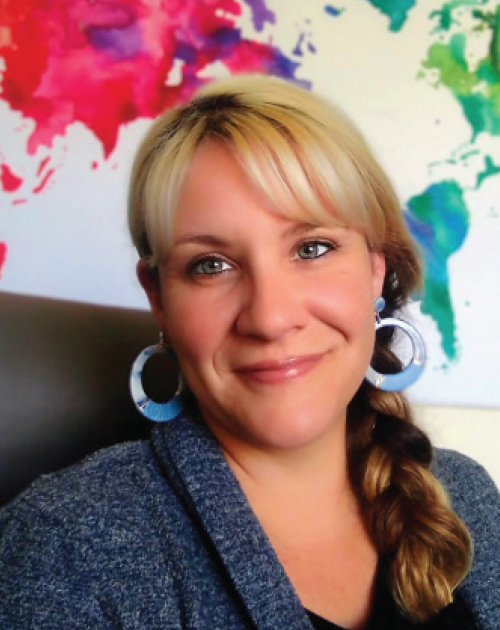
Lisciandrello-Crocco
“We are thrilled to bring Jen’s talent and energy to our team. Her extensive knowledge of performance plastics and thermoforming combined with her ability to develop new and existing business will be a great asset to CartierWilson. Jen is highly motivated, self-driven and thrives on the technical aspect of solution selling. We are confident that her core values will equip her to be successful with our principal manufacturers through our distribution partners, thermoformers and OEMs,” said Vice President Alicia Spence.
Lisciandrello-Crocco comes to CartierWilson with more than 20 years of experience in specifying the right materials in applications throughout various markets. “My intent is to be an asset and add value to every client I meet while ensuring that each customer receives the highest level of care and service. Plastics is in my DNA after many years in the industry and I understand the value that performance plastics brings across all markets CartierWilson serves,” stated Liscinadrello-Crocco.
Mike Nye
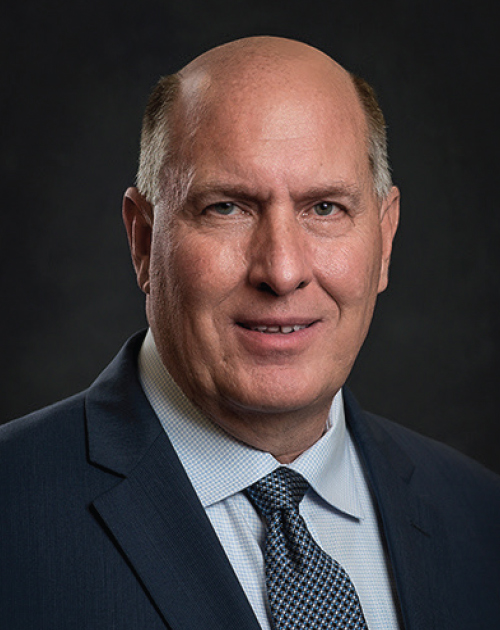
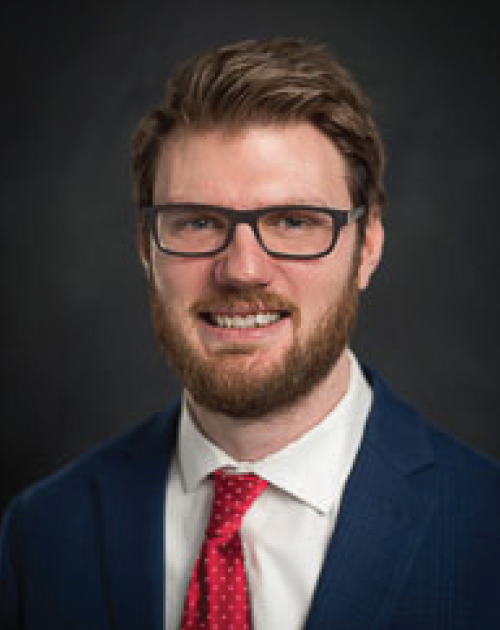
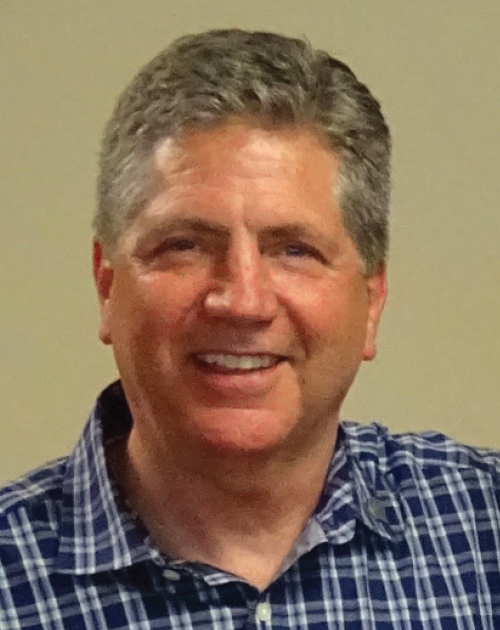
Gugger
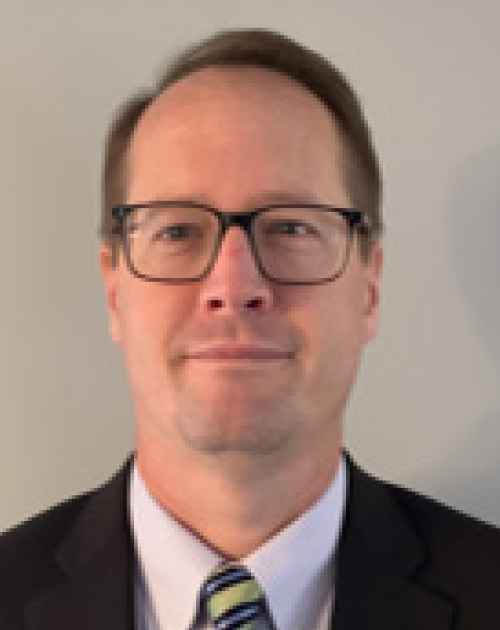
Mold
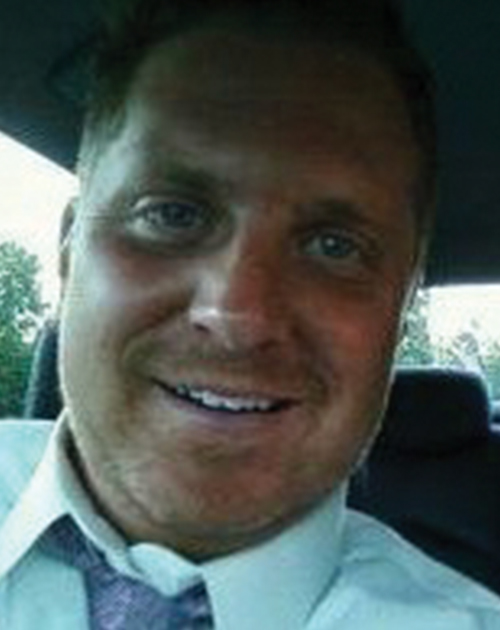
Cwalinski

Snyder
James Amano Michelle Kounlavong Bob Owen
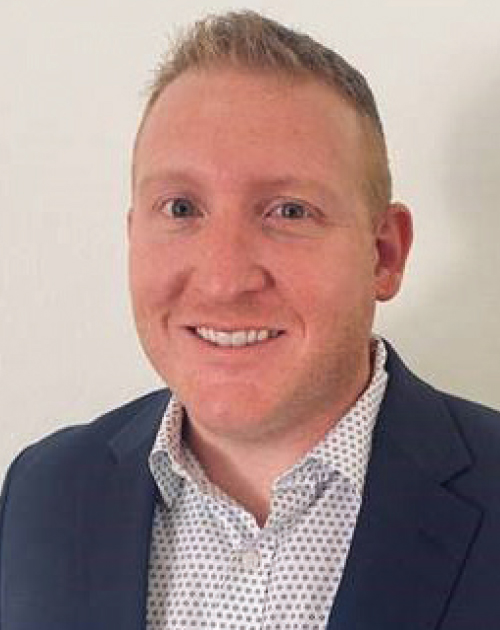
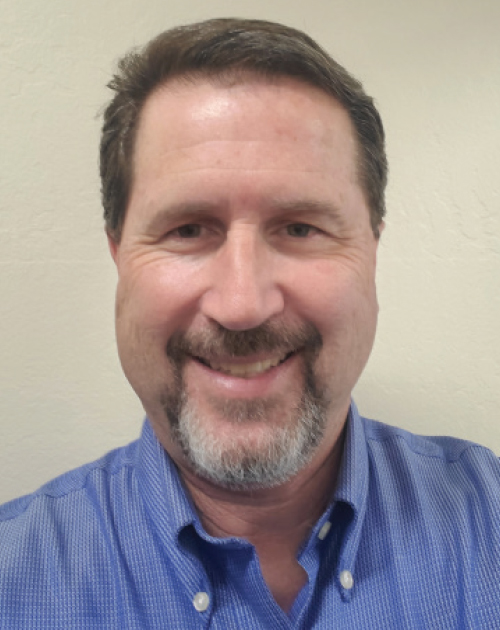
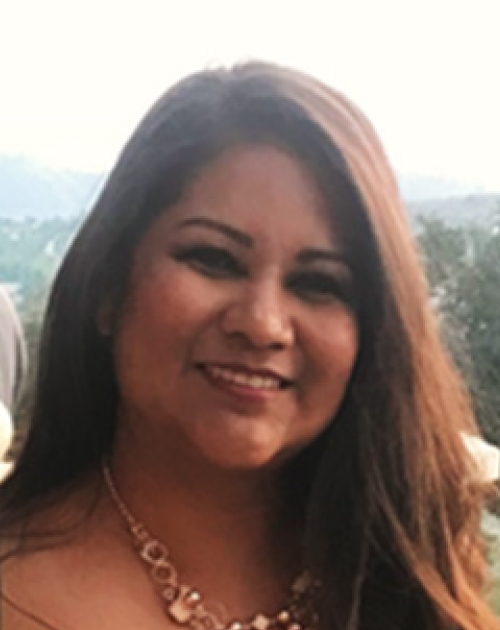

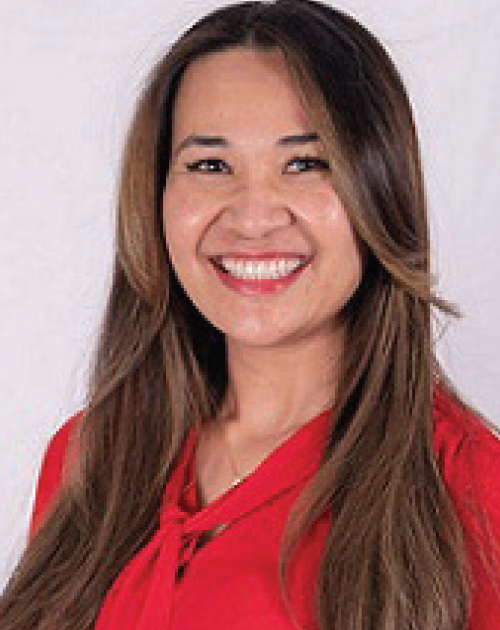
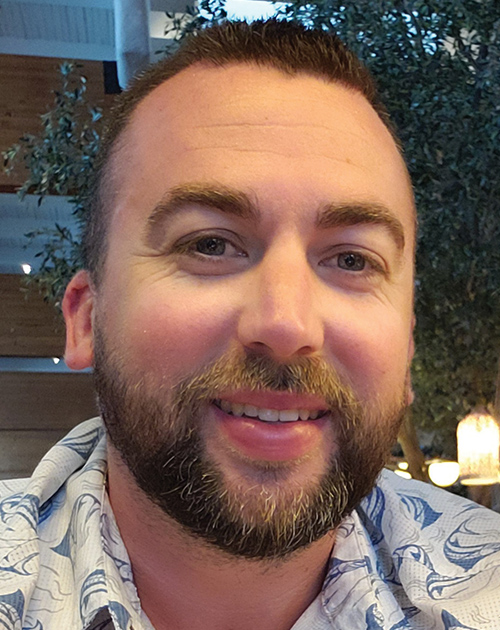
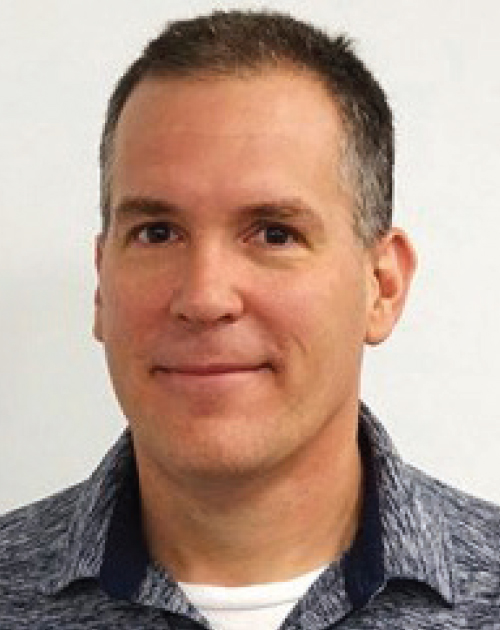
Hopkins
Prior to joining SIMONA, Hopkins worked in the abrasives industry with a focus on steel for the tank and pressure-vessel segments. He will now focus on promoting the capabilities that PP, PE and PVC deliver to these segments, while developing opportunities for these materials in applications that have been dominated by steel or other metals.
“I am excited to lead the key PP and PVC segment initiatives and eager to visit our customers to fully understand their business, pain-points, needs and expectations, and vision for the future,” said Hopkins.
“We are thrilled to have Rick join SIMONA. Rick has worked for the past few years in abrasives and brushes commonly used in metals and spent multiple years prior managing international R&D product development initiatives including onsite injection mold tooling inspections for PP, PE, nylon and other polymers. As our industrial segment has grown over the past few years, Rick’s comprehensive industrial knowledge will further position SIMONA AMERICA as a leader in PP and PVC materials and applications. We are pleased to welcome Rick to the SIMONA AMERICA team,” said Chris Art, vice president of sales for SIMONA AMERICA Industries.
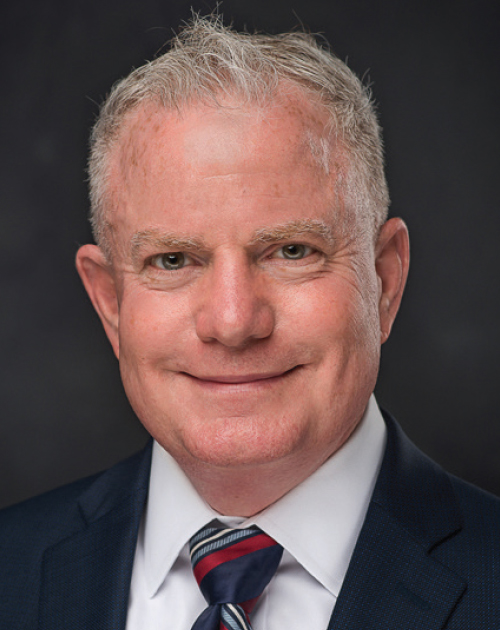
Shepherd
“John’s channel perspective and relationships with our distribution partners is extremely valuable to Cast Nylons and aligns with our future growth objectives,” said Derek Publicover, chief commercial officer. “John brings the leadership and change management qualities that will help us scale our business. He understands engineered plastics and the customers that use them.”
“We are building our commercial organization for the future,” said Cast Nylons President Steve Briggs. “We are evolving into a broader engineered polymers business and the addition of Shepherd is another strong commercial asset and confirmation of our growth agenda.”
Matt Armstrong
![]() |
![]() |
Alaina Swaller | Matt Armstrong |
![]() |
![]() |
Alaina Swaller | Matt Armstrong |
![]() |
![]() |
Alaina Swaller | Matt Armstrong |
Anne Rupp Kate Khrunova
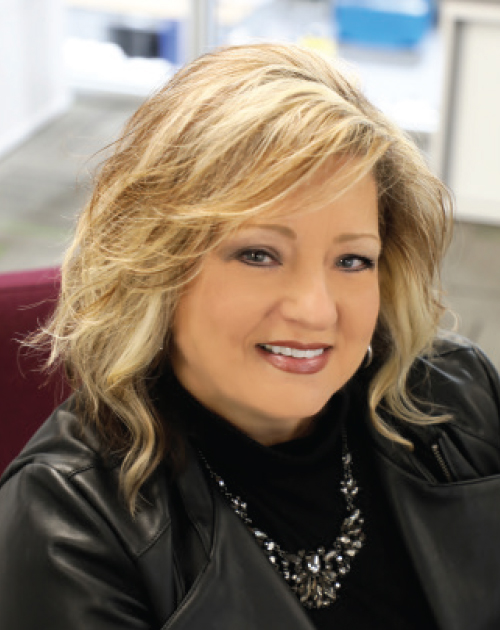
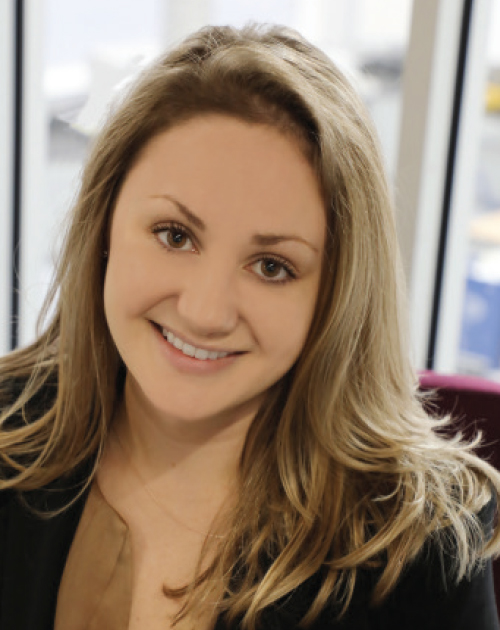
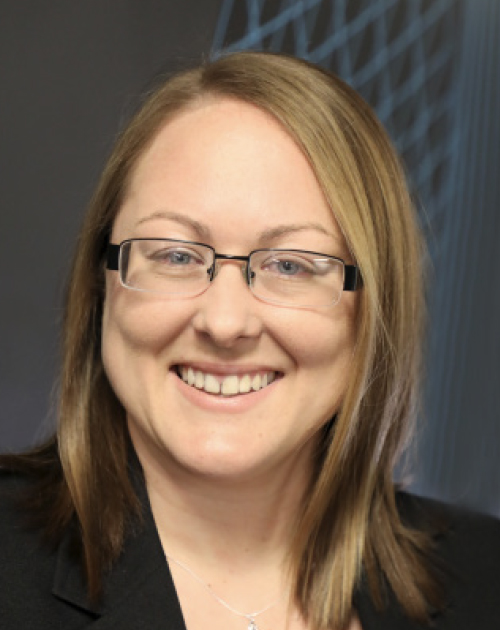
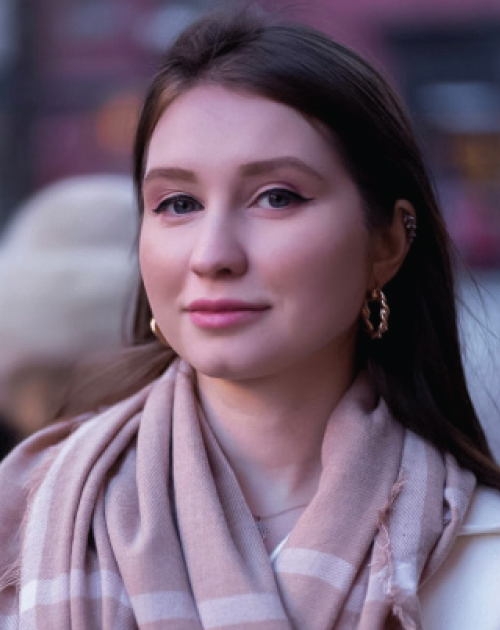
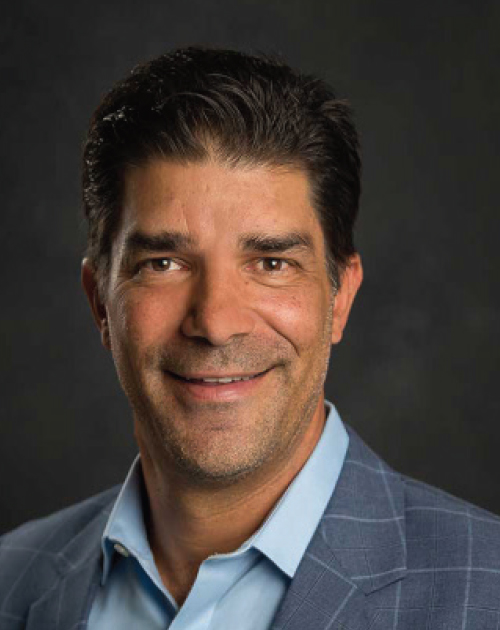
Broll
Drake Plastics Ltd. Co. has been awarded certification as a manufacturer of extruded shapes and precision parts under AS9100D(2016), an international quality management system that includes the ISO 9001:2015 standard and additional requirements for the aerospace industry.
The achievement puts Drake Plastics in esteemed company. Of the million plus organizations worldwide that are ISO 9001 certified, less than 2 percent hold AS9100 certifications. “Our compliance enables us to meet the rigorous demands of aviation, space and defense clients worldwide,” stated Drake Plastics President Steven Quance. “It also elevates our quality systems and procedures to the benefit of all customers, regardless of industry.”
Orion Registrar, Inc. USA, a firm accredited by ANSI National Accreditation Board (ANAB) performed the certification audit in accordance with AS9104/1:2012. Their assessment found Drake Plastics was compliant with the standard as a manufacturer and precision fabricator of extruded and injection molded specialty, high-performance polymer stock shapes and precision parts for the aerospace and defense industries. The rigorous procedures of the AS9100D standard will apply to all products the company manufactures including those for its customers in semiconductor, energy, transportation, medical, life science and many other industries.
The divestment of Arkema’s PMMA business to Trinseo, fully in line with the company’s plan to become a pure specialty materials player by 2024, was finalized on May 3, 2021. Following the announcement made on December 14, 2020, Arkema’s and Trinseo’s teams have carried out all the steps leading to the closing of the transaction. The divested business, which employs 860 people and operates seven production sites (four in Europe and three in North America), will be joining Trinseo, a company specialized in the production of plastics, synthetic rubber and latex binders.
GEHR Plastics is making a further contribution to reducing CO2 and, by switching to eco-gas at their plant in Mannheim, Germany, they implemented CO2 neutral production in accordance with the GHG Protocol Scope 1 and Scope 2 guidelines in Germany as well as in the United States. Environmental protection and sustainability are of great importance to the company. Following the conversion to green electricity implemented in 2016 in Mannheim and in 2020 in their plant in the United States, they took another step toward CO2 neutral production: the entire heating system in their Mannheim plant was switched to eco-gas. As a result, they can produce in a climate-neutral manner.
This year marks the 30th anniversary of AAG Tailored Cutting Solutions. AAG started in 1991 as AXYZ International by Alf Zeuner and Gary Harvey, two friends who embarked on a router repair initiative. Before long, the focus shifted to creating modular machines to better fit their customers’ needs. Today, the company has restructured into AAG Tailored Cutting Solutions, a manufacturer of routers and waterjets. With AAG officially representing the brands AXYZ, WARDJet and the newly revamped ecommerce site, CNCshop.com, the company is optimistic about the future.
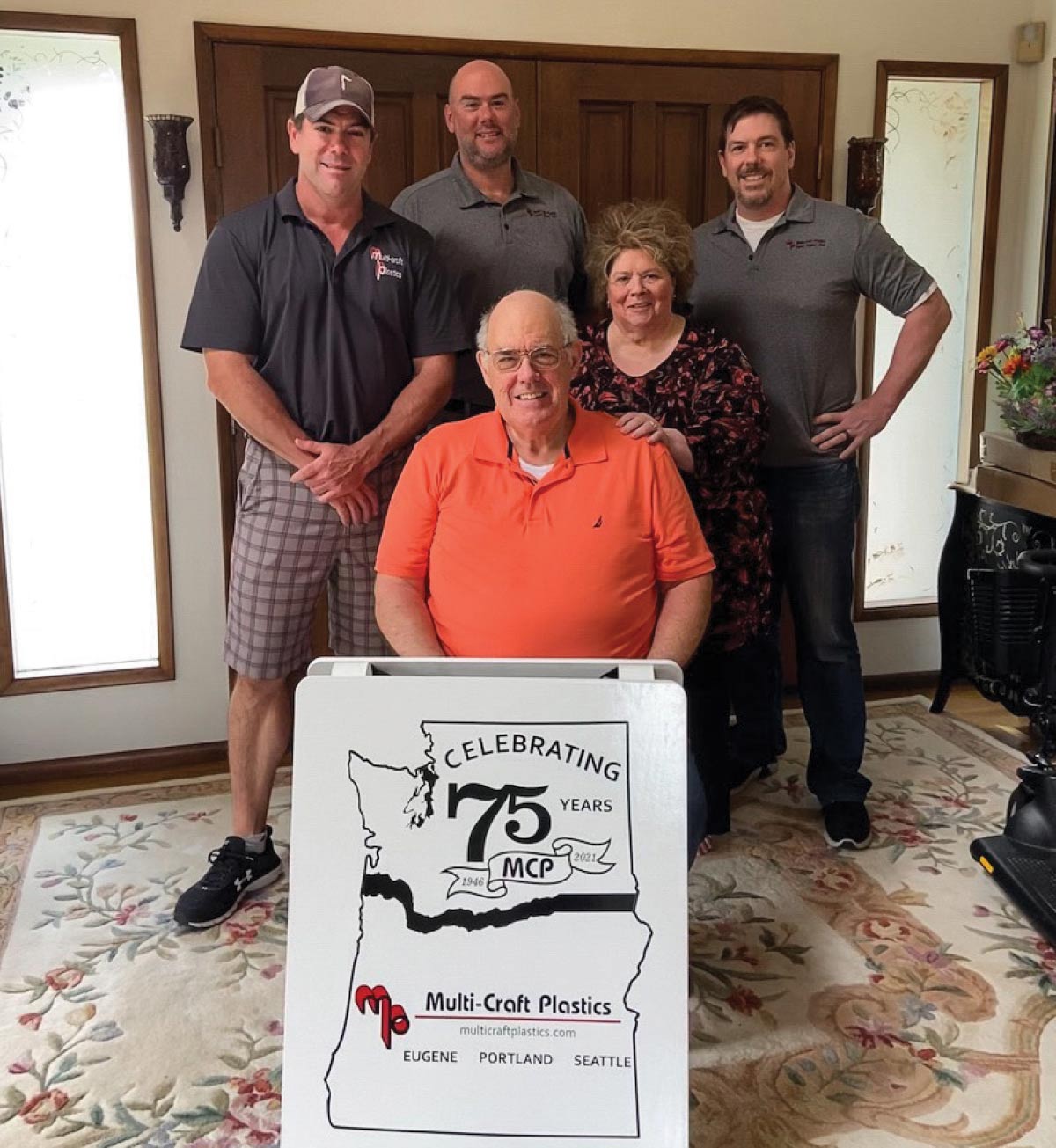
GF Piping Systems (GF) has earned Intel’s Preferred Quality Supplier (PQS) Award for 2020. Through its dedication to continuous quality improvement, GF has achieved a level of performance that consistently exceeds Intel’s expectations. The Intel PQS Award recognizes success in the Intel SCQI Program, a multiyear road map for continuous improvement for high-performing Intel suppliers. Of the thousands of Intel suppliers around the world, only a few hundred qualify to participate in the SCQI Program. The PQS Award is the second-highest honor a supplier can achieve. In 2020, only 26 suppliers in the entire Intel supply chain earned a Preferred Quality Supplier Award.
“As one of only 26 Preferred Quality Supplier Award winners in the entire Intel supply chain, GF Piping Systems has been vital to our success, especially during this uniquely challenging year,” said Dr. Randhir Thakur, chief supply chain officer at Intel. “They provided standout service in a critical area of the Intel supply chain and met or exceeded their annual improvement goals. Earning this award represents years of hard work, continuous improvement and truly exceptional performance.”
To qualify for an Intel Preferred Quality Supplier Award, suppliers must exceed expectations, meet aggressive performance goals and score 80 percent or higher in performance assessments throughout the year. Suppliers must also meet 80 percent or more of their improvement plan and demonstrate outstanding quality and business systems.
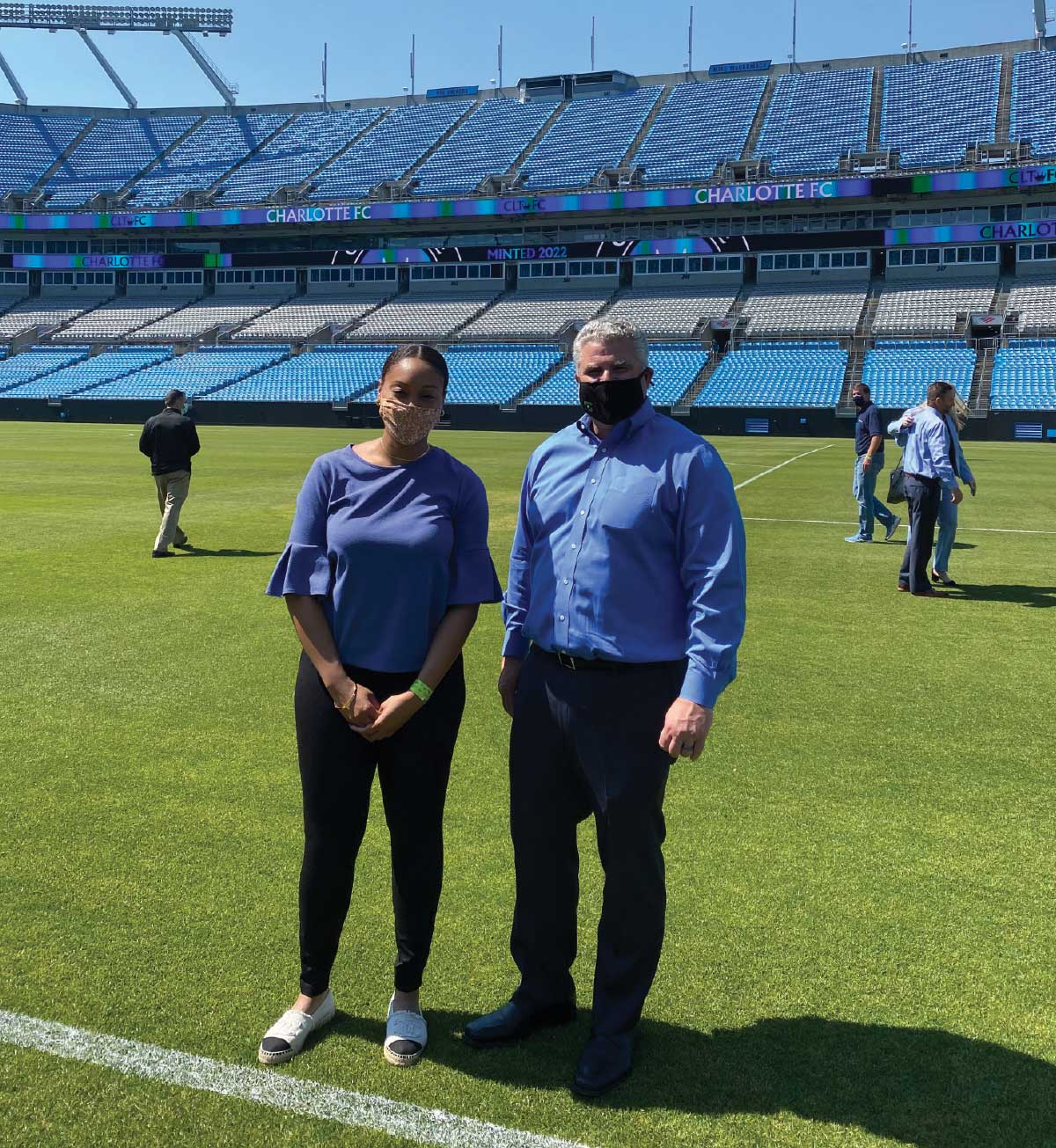
“As our country moves to a new phase in our pandemic recovery, it is no surprise that wholesaler-distributors are delivering by donating needed supplies to mass vaccination sites across America,” NAW President and CEO Eric Hoplin said. “NAW and wholesaler-distributors across the country are proud to help NFL teams and vaccination sites because we know how important it is to safely get more shots in arms as we seek to put the COVID-19 pandemic in the past.”
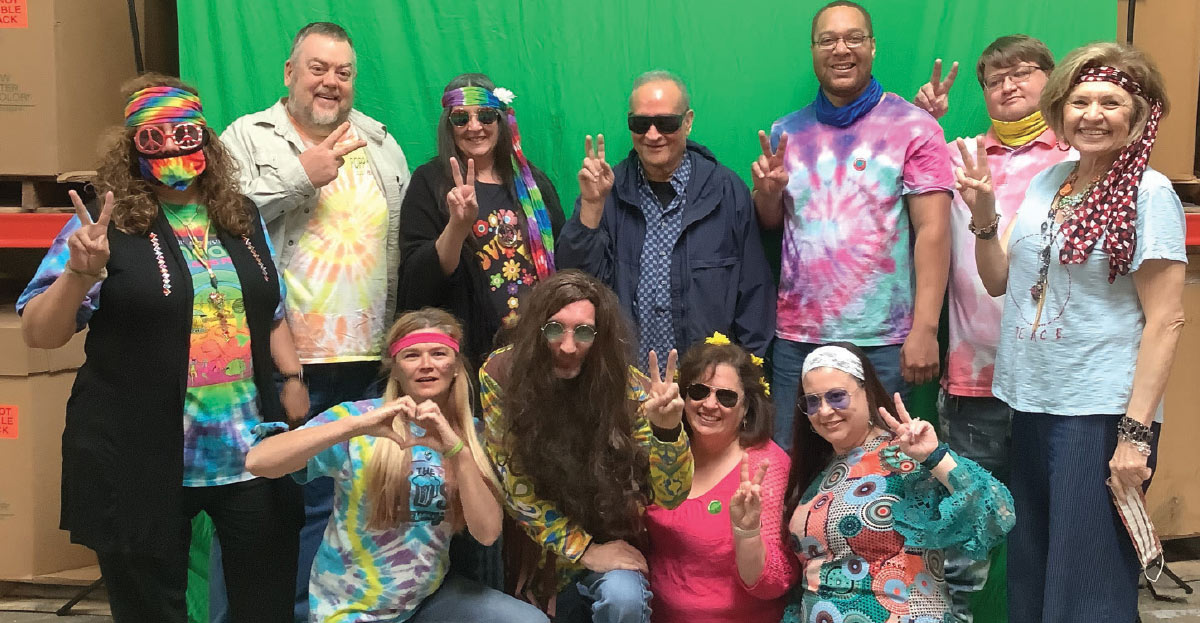
The Curbell T&D team was paired with three Bloomsburg students pursuing their Master of Science in instructional technology. Throughout the semester the students interviewed and collected data from Curbell’s subject matter experts, created a storyboard concept and developed a final product for the client’s use and their portfolios. The final project was a module containing a series of videos with assessments that address the difference between single use and performance plastics, discuss the importance of life cycle analysis (LCA) and share information about Curbell’s commitment to sustainability.
This opportunity turned out to be a beneficial learning experience for the students and the T&D team. While the students learned about Curbell as a company and the world of performance plastics, the T&D team learned about new design software, techniques and how to work with an outside organization to create a product that would still be representative of Curbell’s brand.
“Instructional designers put so much time, dedication and effort into their creations, and one of the toughest parts of the job is receiving feedback,” shared Curbell Plastics’ Associate Director of Training and Development Jinny Kcehowski. “We talked a lot about the importance of understanding goals, objectives, requirements and getting feedback all along the way to ensure that the final product meets expectations. It was an absolute pleasure to work with this team of students.”
The Bloomsburg University graduate students’ final capstone project was a fully animated, entertaining and interactive eLearning module. “We especially loved the concept of Plastics Man,” Kcehowski said. “He’s a superhero whose mission is to inform the world about how important performance plastics are to our everyday lives.” The eLearning module features video lessons with original characters, staggered learning assessments and takes approximately 15 minutes to complete.
Visit the digital version of this issue to watch “The World of Plastics” eLearning module.
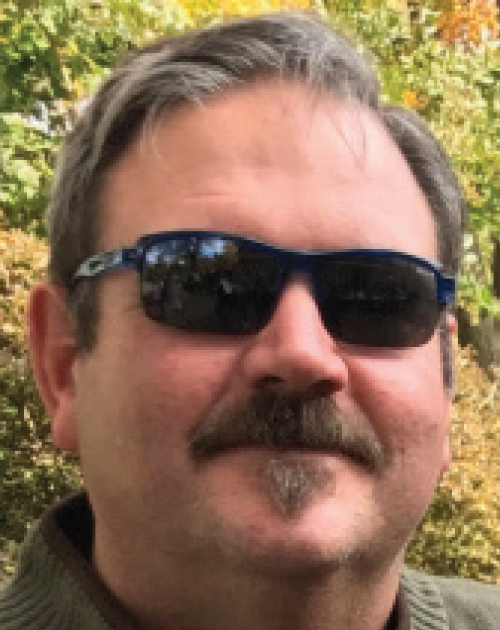
Mort was born in Wynnewood, PA, USA on September 1, 1965 and attended Canterbury High School in Connecticut. He went to The Catholic University of America in Washington, D.C. before transferring to Boston University and graduating in 1988. He worked in the plastics industry for many years in his family business before striking out on his own with Centric Plastics.
Mort is survived by his wife Nina (nee Franco), four daughters, his parents, brothers and sister as well as aunts, uncles, cousins, nieces and nephews. In lieu of flowers, please consider a memorial donation to the National Alliance on Mental Illness (donate.nami.org/mortonrfrench). Condolences may be left at www.mcgoldrickfh.com.