“Normally, Giacomo Puccini’s ‘Tosca’ is a stringently written detective story which takes place at the beginning of the 19th century in Rome,” explained Stage Designer Wolf Gutjahr. “In Halle, we wanted to put the spotlight on the inner states of the people above all else.”
The original settings, which include the interior of a church, a police station and the Castel Sant’Angelo in Rome, were not suited for this purpose. “The main figures are artists who have become caught up in the political system. So, the stage design is intended to display the conflict between politics and art and how we deal with it,” explains Gutjahr.
The letters, which stand 20 feet tall and 40 feet wide, needed to be light enough to be suspended from the ceiling on wire ropes, yet strong enough to support the weight of singers walking across them. Additionally, the letters needed to have even illumination while keeping the light source hidden.
“ACRYLITE® acrylic provided the ideal combination of visual appeal and robustness,” said Torsten Paetzold, production manager in the workshops at the Halle Opera House.
The final letter forms were built by gluing custom-cut 32 mm thick acrylic sheets together and adhering them to aluminum frames. LED strip lights are hidden behind the semi-transparent sheets for adjustable and even illumination. www.acrylite.com.
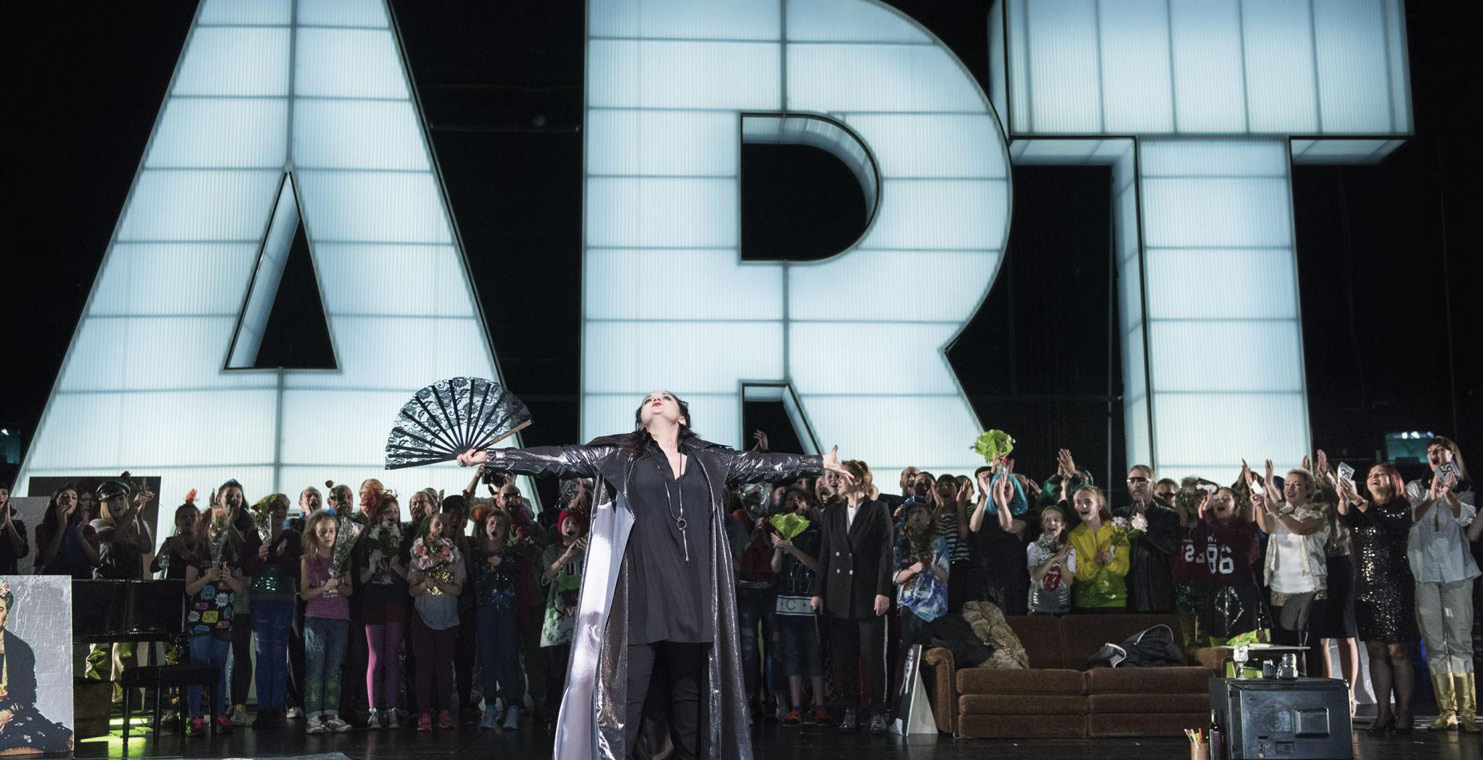
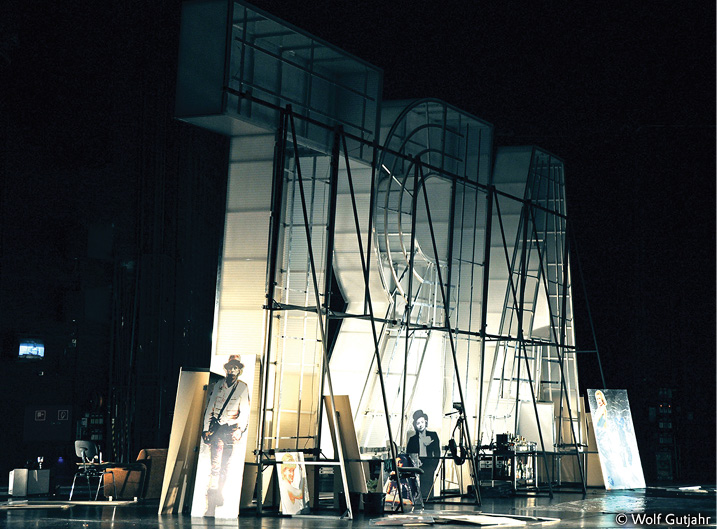
The platform marries material and cloud-based software expertise to provide easy access to a global supplier network for on-demand 3D printing. Included in the high-performance materials portfolio are Arkema Inc.’s ranges of biobased Rilsan® polyamide 11, Pebax® thermoplastic elastomers, Kynar® PVDF and Kepstan® PEKK. The list of materials is expected to grow in the future.
The platform is accessible for free and the steps are simple:
- The user securely uploads their part information.
- The tool selects the optimal material and provides printability analysis.
- The customer generates a real-time price quote and confirms an order to the selected part manufacturer.
The new Easy3D platform, created by Arkema Inc. in collaboration with 3YourMind, an on-demand software specialist, is designed to allow part manufacturers to accelerate on-demand production in an optimized ecosystem.
“Our mission is to facilitate the easy adoption of end-to-end 3D printing technology with advanced and bio-circular materials. Easy3D is a new milestone that will provide end users with digital access to our expertise in advanced materials for 3D printing as well as an optimized supply chain option,” said Adrien Lapeyre, Arkema Inc.’s 3D Printing Group program director. www.arkema.com.
TotalEnergies Corbion and COEXPAN launch biobased cups made from recycled PLA
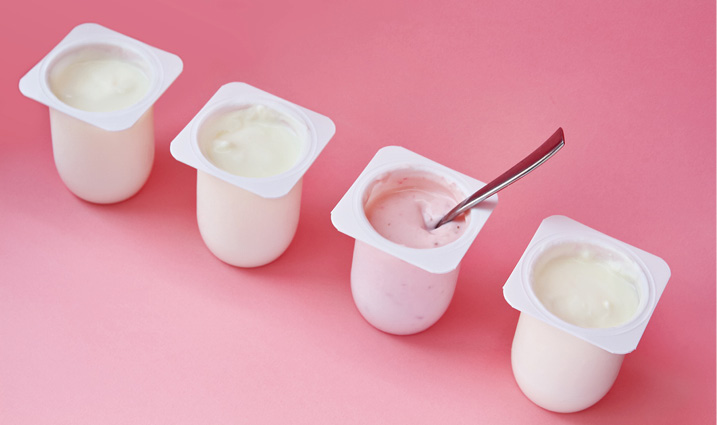
“Another milestone has been achieved! We are very proud to include in our portfolio a new sustainable product that increases the number of technical solutions we can put on the market, a clear added value for all our customers. Having used this material for more than 10 years, we are undoubtedly the leading PLA resin converter in the FFS market,” said Gonzalo Sanchez, COEXPAN’s recycling manager.
Derek Atkinson, senior director sales and business development, added, “Providing PLA solutions to our customers with their existing technology is a priority for TotalEnergies Corbion. We have a team of specialized engineers to work with our partners and develop the right Luminy® PLA grades. And we also buy back the used PLA to recycle it at our facilities. Advanced recycling of PLA is a much more energy efficient process in comparison with other plastics.”
Environmental stresses have increased pressure to meet recycling and sustainability targets. With the readily available recycled polylactic acid (rPLA), brands can offer consumers sustainable options, without additional investment or significant changes in existing FFS facilities.
Luminy rPLA is a bio-based polymer produced from sugarcane. The carbon captured from the atmosphere by the sugarcane is kept in the cycle with advanced recycling. The rPLA has the same properties as virgin PLA, including food contact approval in Europe, the United States and China. www.coexpan.com.

The ALPLA Group is expanding its product portfolio with innovative systems for soap and shampoo pumps made of plastic. By signing a joint venture with South Korean company, HANA Innovation, ALPLA now plans to continue its growth course in the strategically important injection molding (IM) sector. With its cutting-edge solutions for the cosmetics industry, HANA Innovation is a recognized supplier of pumps and lotion dispensers. Founded in 1993, the company has developed fully recyclable solutions made of plastic mono-material.
“The potential for high-quality, recyclable pumps is enormous. As a system provider, we can offer the matching bottles at the same time. With this new partnership, we are combining our strengths as a globally operating company with the technological edge of HANA Innovation,” says Michael Feltes, global business development director IM at ALPLA.
The ECO Pump system developed by HANA Innovation is made of 100% polypropylene, which makes it fully recyclable, and can also be manufactured from post-consumer recycled material. In addition to its ecological advantages, the pump convinces with its convenient handling. A smooth spring execution guarantees linear and even force over the entire pump stroke. In the future, the pumps – like all ALPLA products – will also be customizable.
With the new cooperation, the two companies want to push the worldwide distribution of the sustainable pumps with the new patented plastic spring technology and, in addition, offer complete systems including the bottle. www.alpla.com.
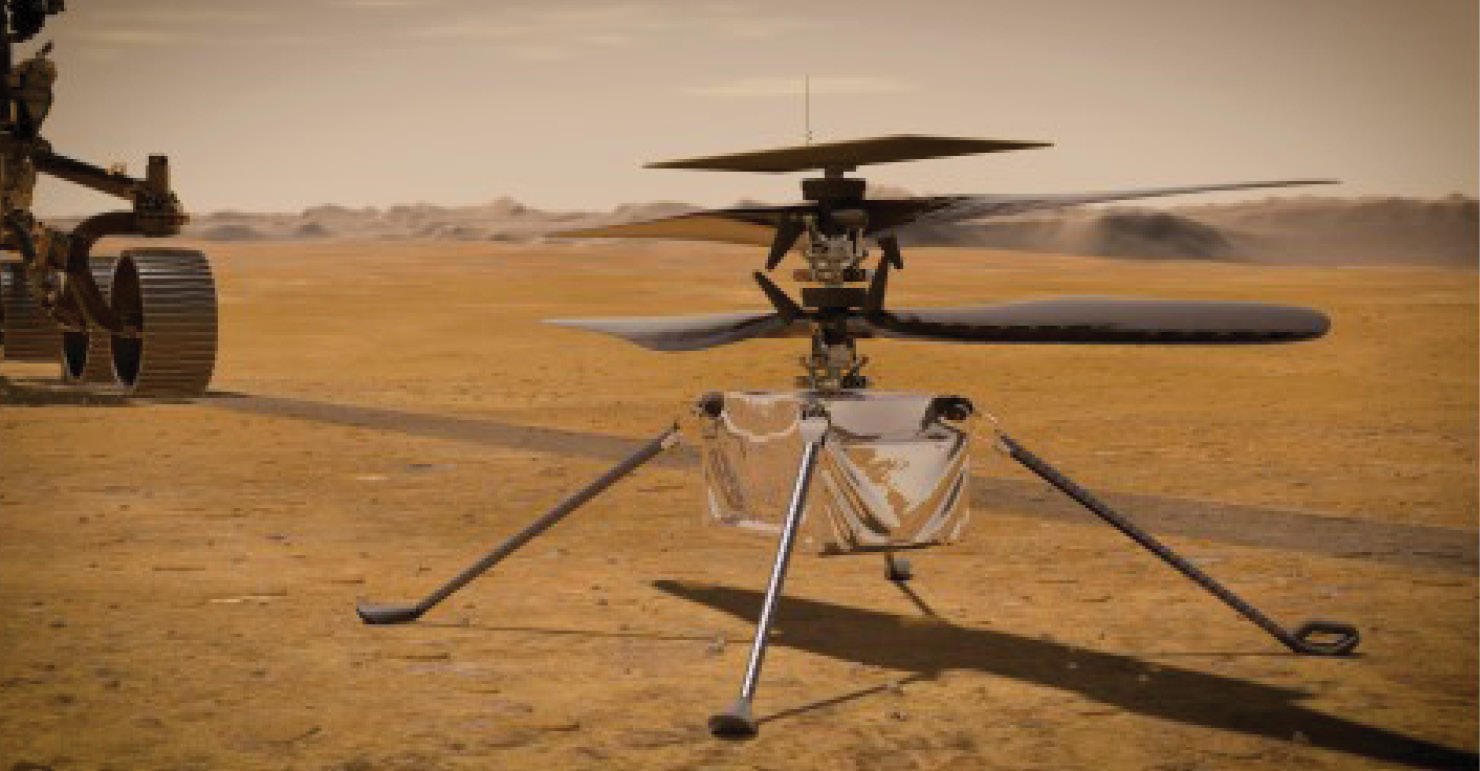
Photo © NASA/JPL-Caltech