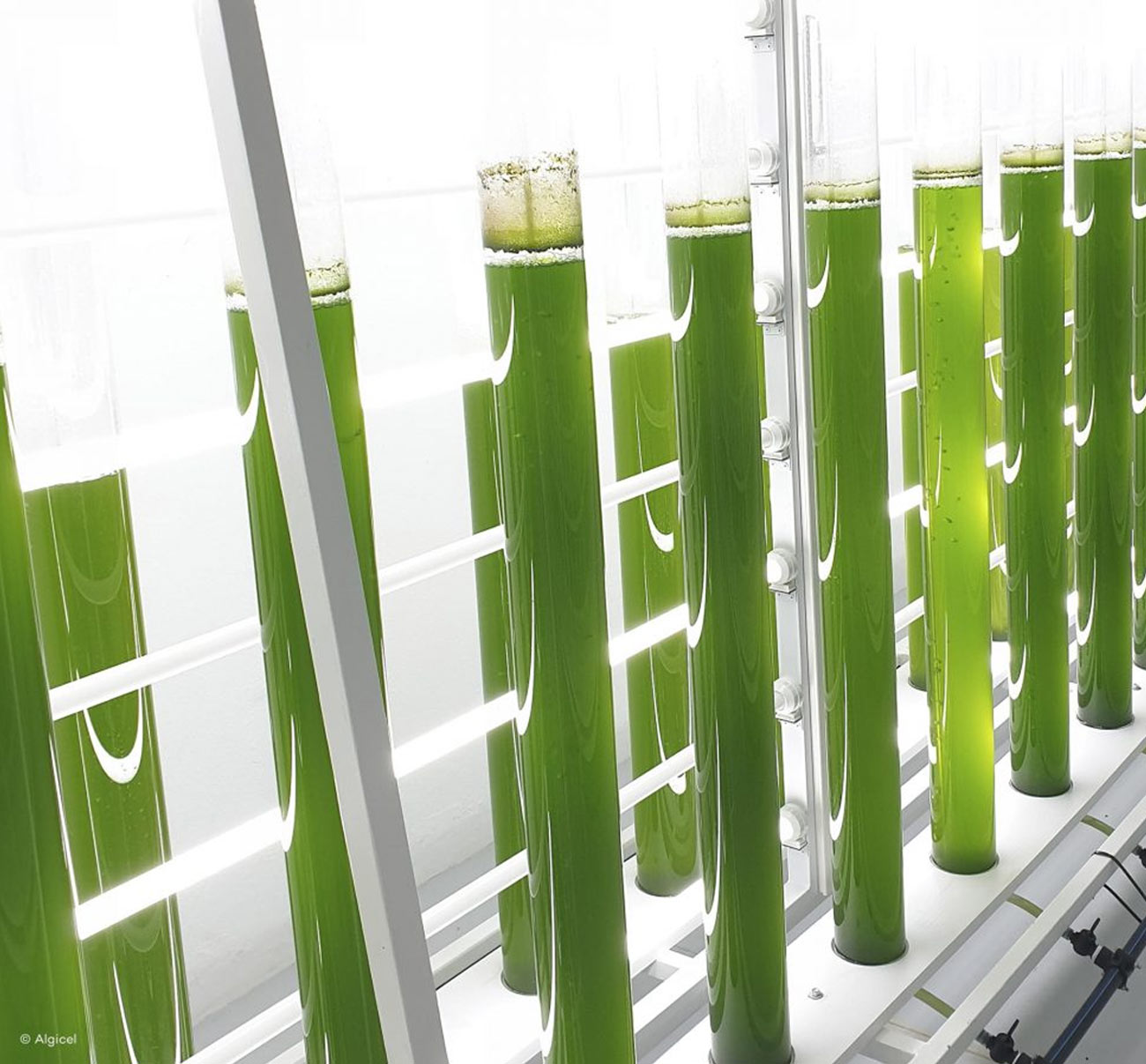
© Algicel
Microalgae produce valuable biomass more efficiently than any land plant. Since these little all-rounders primarily require plenty of even light to do their job, the algae grower Algicel relies on transparent ACRYLITE® tubes.
Microalgae are used in a variety of ways: In dietary supplements, cosmetics, pharmaceutical products and even in energy generation. Researchers are constantly discovering new applications for these miracle plants.
The founders of the Portuguese company Algicel discovered a high concentration of the antioxidant astaxanthin in the microalgae in their native Azores, more precisely on the island of São Miguel. Antioxidants protect not only the skin’s cell structure, but also the whole body against oxidative stress and aging symptoms as well as inflammation.
Since 2007, the company has been researching a way to produce the health-promoting substance astaxanthin from the microalgae growing in their natural environment on the Azores. After all, the climate and pure inland waters of the islands are ideal for this type of microalgae. In the summer of 2019, the company started the industrial cultivation of the Haematococcus pluvialis species of microalgae based on the technology that was developed in house.
To produce the microalgae for the mass market, the company first had to create an environment similar to that of the inland water bodies of the Azores. Algicel opted for so-called photobioreactors made of ACRYLITE tubes. The extruded acrylic tubes are UV permeable across the entire spectrum of sun rays and provides 92 percent light transmission, offering optimum conditions for the microalgae. Along with nutrients, water and carbon dioxide from the air, algae primarily require plenty of even light to grow, making the ACRYLITE acrylic tubes an excellent choice to cultivate the microalgae.
“ACRYLITE acrylic is one of the most transparent materials available today. There is virtually no absorption of visible light in the material,” said Janina Rossmann, product manager at Roehm. “And the transparency of the tubes remains unchanged for decades: ACRYLITE has UV protection inherent to the material. This prevents yellowing and thus the loss of transparency. ACRYLITE colorless tubes are backed by a 10-year warranty.”
Thanks to these properties, the microalgae now grow under nearly natural conditions and reach their maximum number within just 30 days. Harvesting takes place by centrifugation of the water/microalgae mix. “The absolute roundness of the tubes means that there are no edges that could cause trouble,” Rossmann explains.
Then, the harvest cycle begins again. The more than 1,000 six-foot high tubes must be rinsed and refilled with every cycle. The smooth, non-porous inner walls ensure that no bacteria or microorganisms remain stuck to the walls. This keeps the ACRYLITE tubes clean during the entire cultivation — thereby contributing to an efficient and sustainable biomass production. www.acrylite.co.
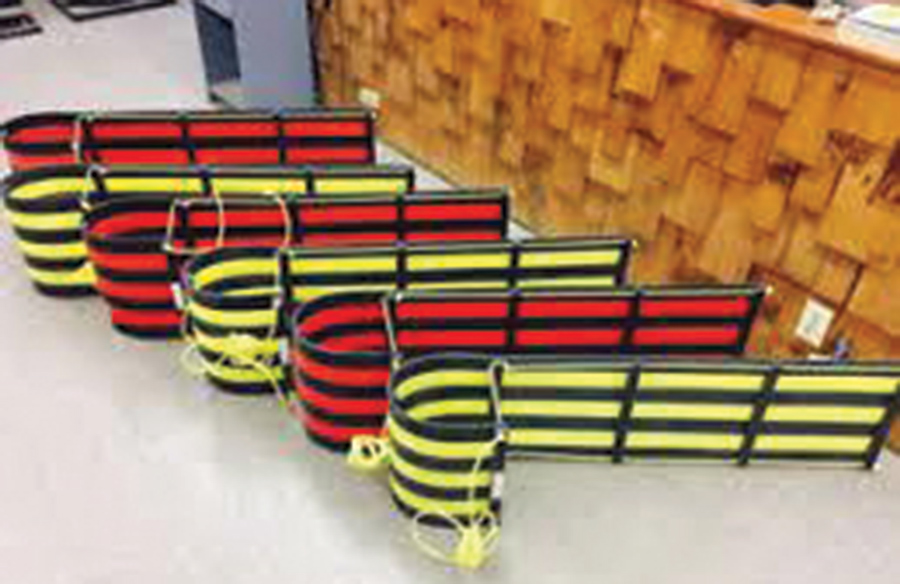
The design involves laminating together multiple assorted colored strips of ultra-high molecular weight polyethylene (UHMW) to create a safe, durable, attractive, fun item that is sure to delight anyone using it. The material’s low coefficient of friction makes the sleds fast. “They go like crazy” and will go much farther than the standard toboggan. Safety is a priority for the company, so they inform customers of the speed and attach labels to each toboggan, showing they are not to be used on hills that lead to a lake, river, road, railroads and other unsafe areas. These sleds typically last for decades. There are customers and friends whose received the Maljohn Toboggans 30+ years ago, whose grandchildren are now enjoying the thrill of winter with them.
One of their suppliers, Roechling Engineered Plastics generously donated enough material to produce hundreds of sleds. For the past two years, Maljohn Company has sold these toboggans to fundraise for charities that are close to company founder Malcolm Johnson’s heart, Ronald McDonald House Charities and Childhood Cancer, with 100 percent of the funds raised being donated. “Being able to bring joy to the lives of others is our purpose. It lifts my spirits,” said Johnson. www.maljohn.com.
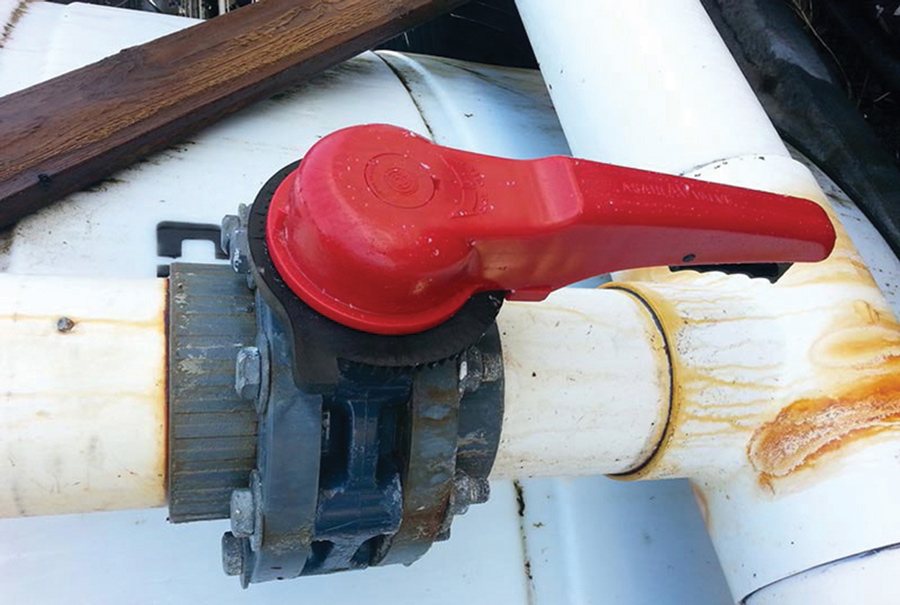
While abalone may thrive in saltwater, it’s a harsh environment for metallic valves. A western U.S. aquaculture farm was experiencing widespread issues in their pipelines due to corrosion. The metallic butterfly valves were seizing, their stems shearing and handles and discs breaking. Rust particles were traveling in the pipelines, causing contamination and blockages in the saltwater feed lines.
Asahi/America’s Type-57LIS butterfly valve was the ideal solution for replacing the corroded metallic butterfly valves because both valves have identical face-to-face dimensions. Installing the Type-57LIS in place of metallic valves can be done without any modification to the existing piping system. The abalone farm originally installed a 6″ PVC/ EPDM Type-57LIS butterfly valve to test the durability of the valves. After six months, they were pleased with the functionality and corrosion resistance of the valve in their tank application.
With the results they experienced during the test period, the abalone farm purchased nearly 70 6″ and 8″ Type-57LIS butterfly valves to replace all the corroded metallic butterfly valves throughout the farm. This decision was based on the ability to directly replace the valves without shutting down the facility and no rework required on the existing pipelines.
The farm has since retrofitted nearly a third of the Asahi butterfly valves with pneumatic actuators to ease operation at the facility, which will aid in their efforts to upgrade and expand production for their worldwide customer base.
The Type-57LIS butterfly valve is well suited for a wide variety of life support applications. The Type-57LIS butterfly valve conforms to ISO-5752 short pattern face-to-face dimensions. This allows the Type-57LIS to directly replace metal valves conforming to the same standard. Available in ANSI B16.5 wafer or ANSI lug models with 316 stainless steel drop-in lug inserts. The Type-57LIS butterfly valve can be pneumatically or electrically actuated. www.asahi-america.com.
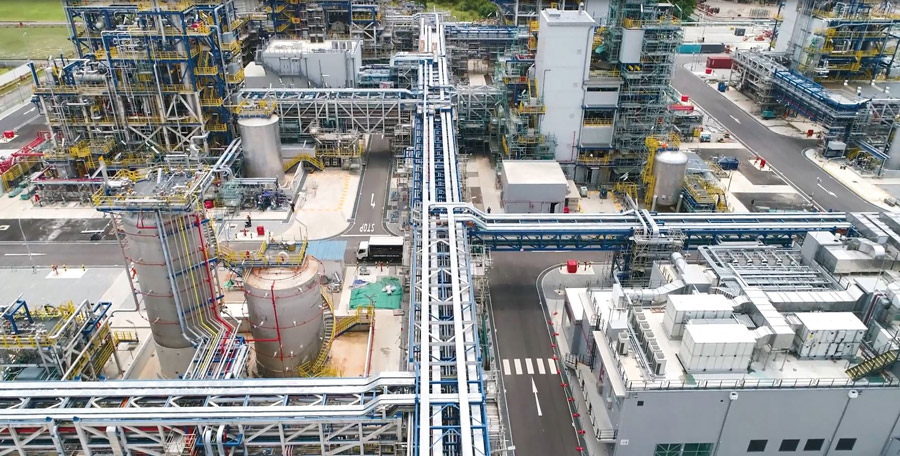
When designing the new plant, Arkema engineers knew that Kynar® PVDF piping systems would provide the maximum longevity and reliability, especially in challenging chemical environments. Kynar PVDF has a long history of being used in piping systems for acidic and halogen environments, both of which are used in the new Singapore plant. Supplied by SIMONA, these piping systems provided the chemical resistance, high temperature capabilities and low permeation needed to withstand such aggressive environments. Arkema is proud to not only continue to manufacture its high-performance materials but also stand by their product line for some of the world’s most extreme environments. www.arkema.com.
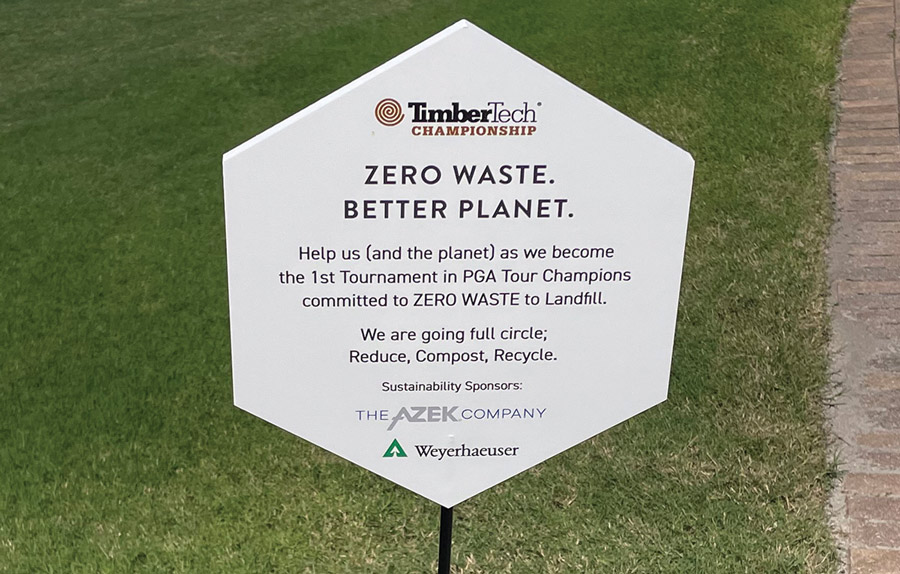
One way The AZEK Company — the event sponsor and an affiliate of Vycom — accomplished this goal was to use Vycom materials for the event’s wayfinding, signage and entertainment elements. Vycom polyvinyl chloride (PVC) and polyethylene (PE) performance plastic materials can be returned to company recycling facilities and used to manufacture The AZEK Company’s residential and commercial products, ensuring they do not end up in landfills.
Vycom provided TimberLineTM high density polyethylene (HDPE) sheets and Celtec® and StreamLiteTM PVC sheets in various thicknesses to Think Patented of Miamisburg, OH, USA, which created signage and the games for the spectator area designed as a casual and fun “TimberTech Backyard.” Among the elements produced were wayfinding and informational signs, an oversized chessboard with printed panels alternating with unprinted panels, a large Jenga®-style game, cornhole boards and a decorative backwall panel featuring a dimensional logo for sponsor Meomi. Think Patented used an HP UV flatbed printer to create the graphics and a Kongsberg flatbed cutter for trimming.
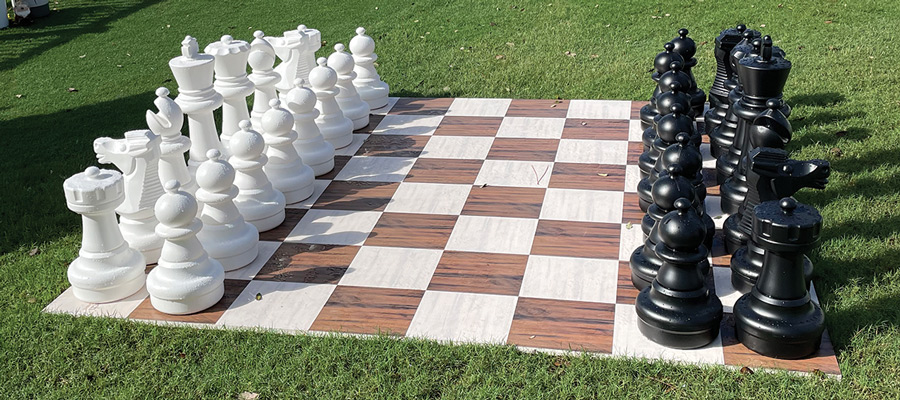
Spectators attending the event were encouraged to donate plastic bags resulting in approximately 5,000 bags collected during the tournament. These recycled materials are used to create TimberTech composite decking. Other initiatives included ensuring food waste and associated service items were composted, which returns organic matter and nutrients to the soil.
“No waste was sent to area landfills,” said Amanda Cimaglia, vice president of ESG and corporate affairs for The AZEK Company. “We spent several months designing waste out of the event and then finding ways to repurpose, recycle, reuse, donate or compost.” One hundred percent of used materials (signage and graphics, plastic bags, food and service items, etc.) were diverted from landfills: 49 percent were recycled, 30 percent were converted to energy sources, 16 percent were donated and 5 percent were composted. www.vycomplastics.com