SpecialFocus
additives in extruded sheet:
safety and design options
additives
by Chris Holland
R
aw material additives play an important role in the manufacturing of extruded sheet products. Additives can be used to aid in more efficient manufacturing — allowing for easier production — and they can be used to enhance the features of finished products, providing greater application benefits. Here are some examples of how additives contribute to materials that enhance safety and provide creative design options.
Photoluminescence
A great example of an enhanced feature achieved with the use of additives would be photoluminescence (aka glow-in-the-dark). A blend of special non-toxic pigment additives is added to the base acrylic resin during the extrusion process to create a finished sheet product that can absorb and store energy from ambient light sources. After only one hour of light exposure, the additives can absorb and store enough energy to transmit 90 minutes of light which can be seen from a distance of 25 feet during times of total darkness. This photoluminescent quality is required to meet many building code standards for lifesaving emergency egress signage applications. The additive is non-toxic and allows the finished product to be a sustainable, green design with zero energy consumption.
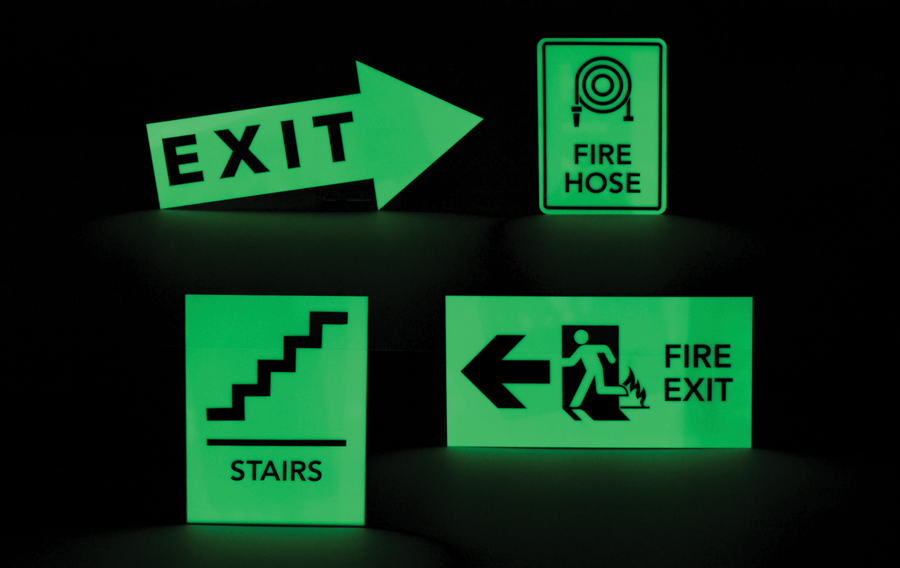
No electricity or maintenance required: LaserGlow emits light from stored energy for up to 90 minutes to provide life-saving emergency messaging.

The reflective top layer addition to this acrylic sheet is particularly advantageous in boosting visibility in low light conditions at night.
Decorative laminates
Plastic sheets can be transformed into high end decorative laminates by adding a foil to the surface(s) of the sheet. These additive foils are available in a wide variety of colors, design prints, metallics, finishes and textures that can provide endless customization. They can be added during sheet production for high volume runs or added via a secondary lamination operation for small quantities as well. In addition to great finished looks on their own, the foil additives also create a layered product which is highly desirable for engraving via laser or rotary equipment. Higher quality acrylic foils can provide added ultraviolet (UV) and scratch resistance, improving the long-term performance of the sheet when exposed to more challenging environments. The addition of foils allows the end user to take creativity to a new level.
Self-extinguishing properties
Another common use of additives is to create self-extinguishing plastics. Many local and national building codes require plastics to be self-extinguishing, meaning that once the flame source is removed, the product will not support flame on its own. A UL94 V0 rating can be achieved with the use of a non-bromine, non-halogenated fire-retardant additive allowing the sheet to have the necessary self-extinguishing qualities needed to meeting building codes.
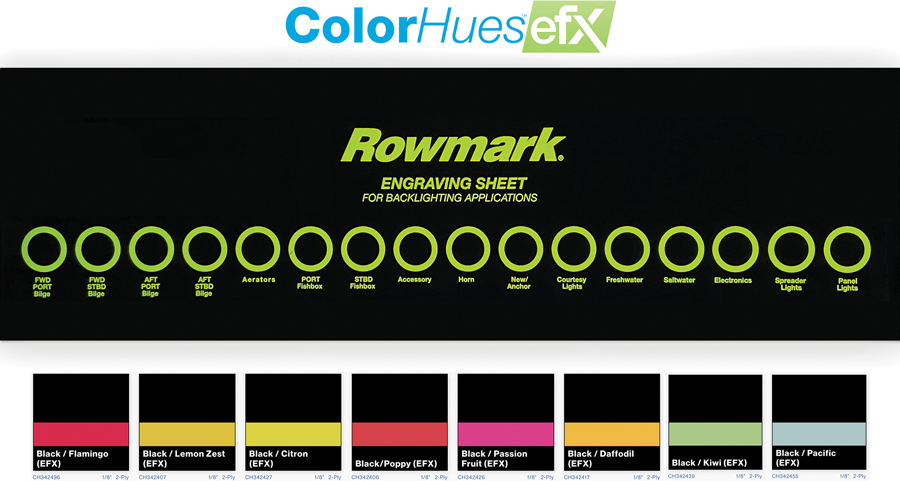
The addition of an engravable foil layer on top of vivid colors creates eye-popping backlit displays.
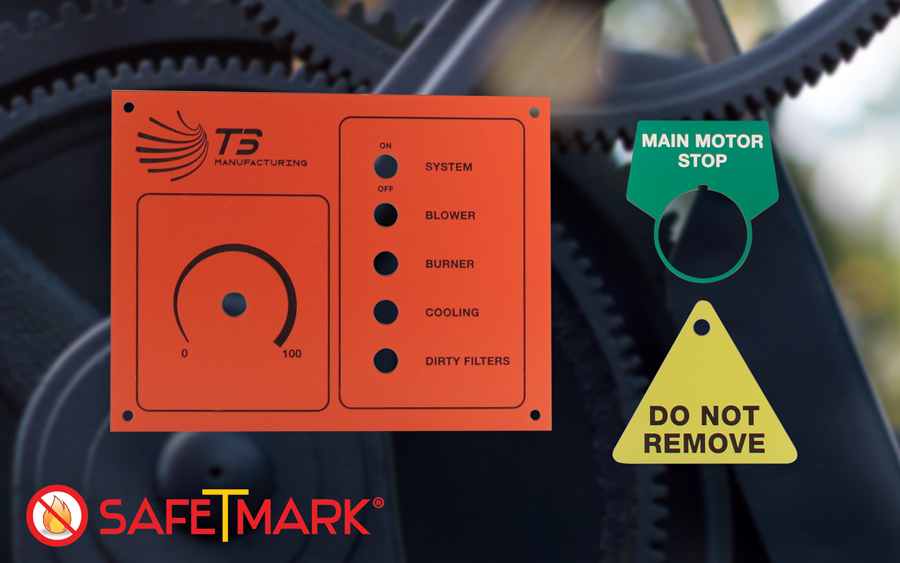
With self-extinguishing properties and a UL94-V0 rating, Safe-T-Mark is an excellent choice for applications where flammability is a concern.
Practical and versatile
This article has showcased some exciting applications for additives, from providing the photoluminescence that allows people to safely exit structures in low-light conditions to the many options available to designers looking for innovative laminates to the all-important ability for plastics to self-extinguish. Thanks to additives, there is a world of possibility for performance plastics.
Chris Holland is the business development manager for Rowmark LLC. For more information, contact Rowmark LLC at 5409 Hamlet Drive, Findlay, OH 45840-6618 USA; (800) 243-3339 or (419) 425-8974, fax (419) 425-0501, sales@rowmark.com or www.rowmark.com.