SpecialFocus
ince 2009, towns around Lake Geneva, Switzerland have used the lake to create thermal networks to supply heating and cooling for local buildings. The technology works by exploiting the static temperatures at the lower depths of the lake with a heat pump on land to supply heating more efficiently during winters and cooling during summers. The technology can reduce energy usage for heating and cooling by up to 50 percent, providing an environmentally friendly alternative to traditional techniques.
Project GeniLac was one of the first projects to use the lake’s unique properties, connecting the United Nations district buildings to the system. In 2016, a nearby municipality took a similar approach in La-Tour-de-Peilz to heat more than 400 homes. By 2018, leaders expanded the GeniLac system to support the Geneva city center and seven other municipalities, serving approximately 50 buildings.
In 2021, Centre Patronal sought to build a new employer center in Lausanne to cool and heat the building with the same hydrothermal technology.
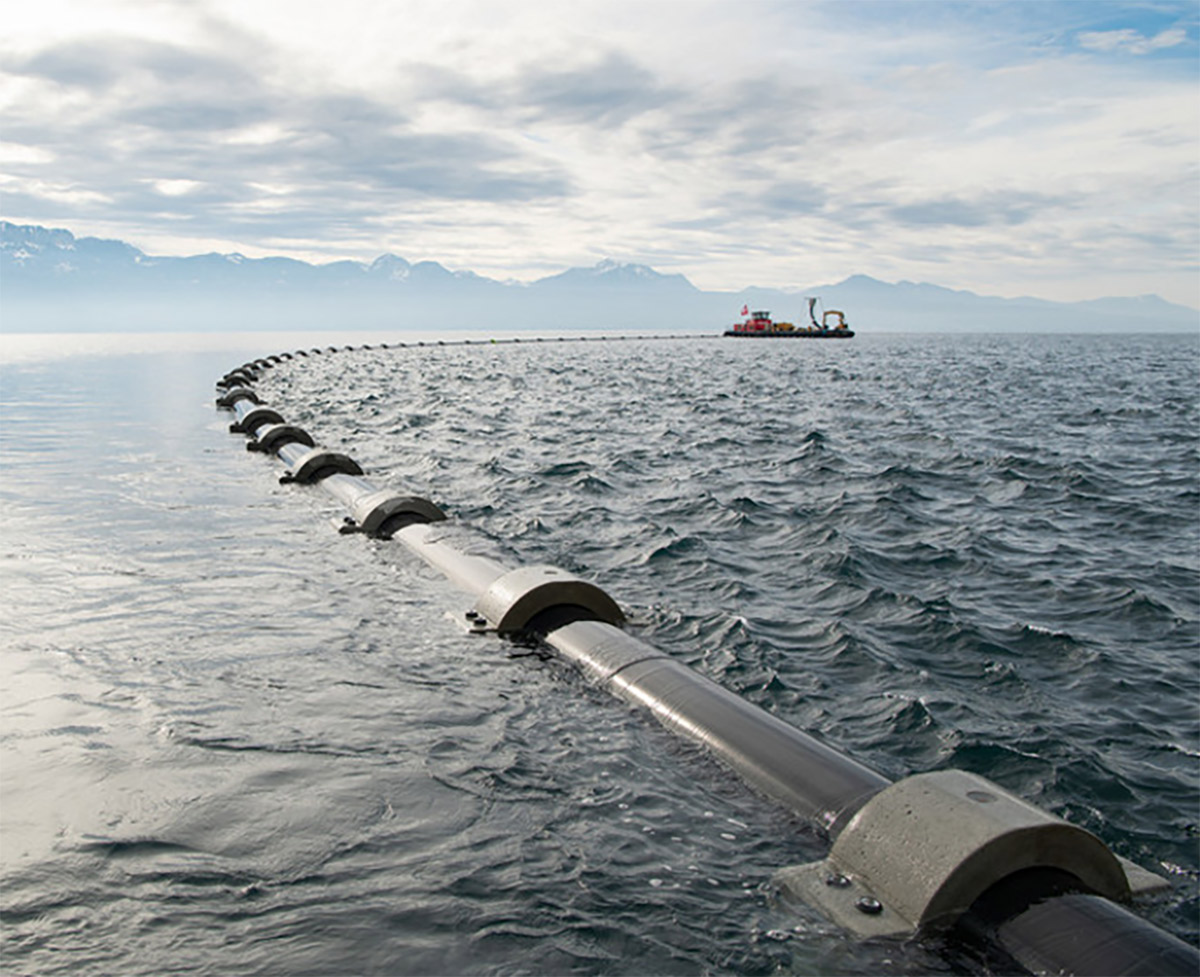
The pipeline comprised OD 500 mm SDR 11 PE 100-RC AGRULINE and was carefully flooded and lowered to a depth of 80 m in an S-shaped curve. Photo courtesy of Hydrokarst Swiss.
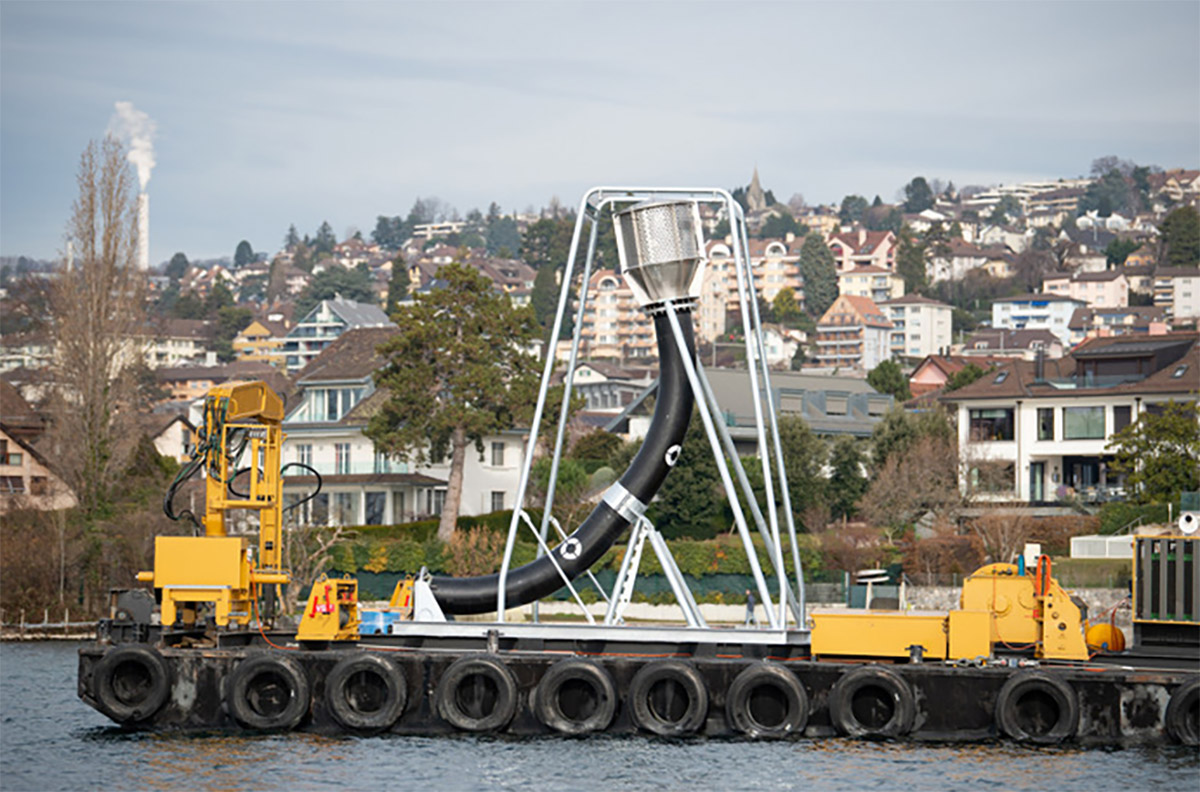
AGRU supplied sweep bends for the seawater intake pipe. Photo courtesy of Hydrokarst Swiss.
The area of Lake Geneva near Lausanne presented a unique opportunity as it is the site of the lake’s deepest point. Hydrothermal power leverages temperature gradients, so creating the system’s intake point at a lower depth offered the potential for greater efficiencies. Other systems have drawn water between 45 and 70 m below the lake’s surface. Designers for Centre Patronal’s design targeted a depth of 80 m. The temperature hovers between 4 and 8 degrees Celsius (39-46 degrees Fahrenheit) throughout the year.
The targeted depth, however, presented challenges. First, the total length of pipe for the project meant on-site fabrication. Second, the intake and outfall sections of the system would be at significant depths, requiring good pressure resistance. The depth would also cause more costly maintenance. Lastly, any fouling in the pipe over time would decrease flow capacity and increase pumping cost, negating the purpose of the system. The solution would need to address all these factors.
Centre Patronal opted for an HDPE pipe made with a resin gaining popularity known as PE 100-RC. Typically, HDPE is made with either PE 100 or PE 4710 resin. To summarize, PE 100 polyethylene pipe grade material designation within ISO defines a different set of criteria when compared with PE 4710, which is an ASTM pipe material designation. PE 100 establishes the product as being made with polyethylene (PE) that maintains a minimum required strength (MRS) rating of 10 MPa (multiplied by 10) over 50 years (statistically projected) at 20 degrees Celsius (68 degrees Fahrenheit).
Unlike the ISO designation, ASTM classifies the PE pipe grade material based on density, slow crack growth resistance and hydrostatic design stress (HDS). The last three parts are all measured according to specific ASTM testing conditions. PE 4710, for example, means that the product is made of polyethylene with a “4” rated density, “7” rated slow crack growth class and has a 1,000-psi maximum recommended HDS with a 0.63 design factor at 23 degrees Celsius by ASTM D3350 and the stress rating policies in the Plastics Pipe Institute’s PPI-TR-3. Pipe grade polyethylene materials with the PE 4710 designation describe a pipe grade material that meets exceptionally high-performance requirements.
At high-end, long-term applications, the pipe’s performance is often limited by crack formation. This makes resins such as PE 4710 and PE 100-RC (resistance to crack) ideal for applications requiring superior durability, longevity and stress crack resistance.
Longer lasting pipes, especially in the context of hydrothermal power intake and outfall piping systems, means significantly lower maintenance costs compared with other piping materials. Additionally, the smooth internal surfaces of the pipe and abrasion resistance means higher flow capacity and lower pumping costs throughout its service life.
Hydrokarst Swiss handled the pipe installation starting at the delta of the Rhone River. After assembly, the pipe was tugged more than 20 km to the site on the lake. Divers then lowered the two pipelines to the target depth of 80 m before completing the installation.
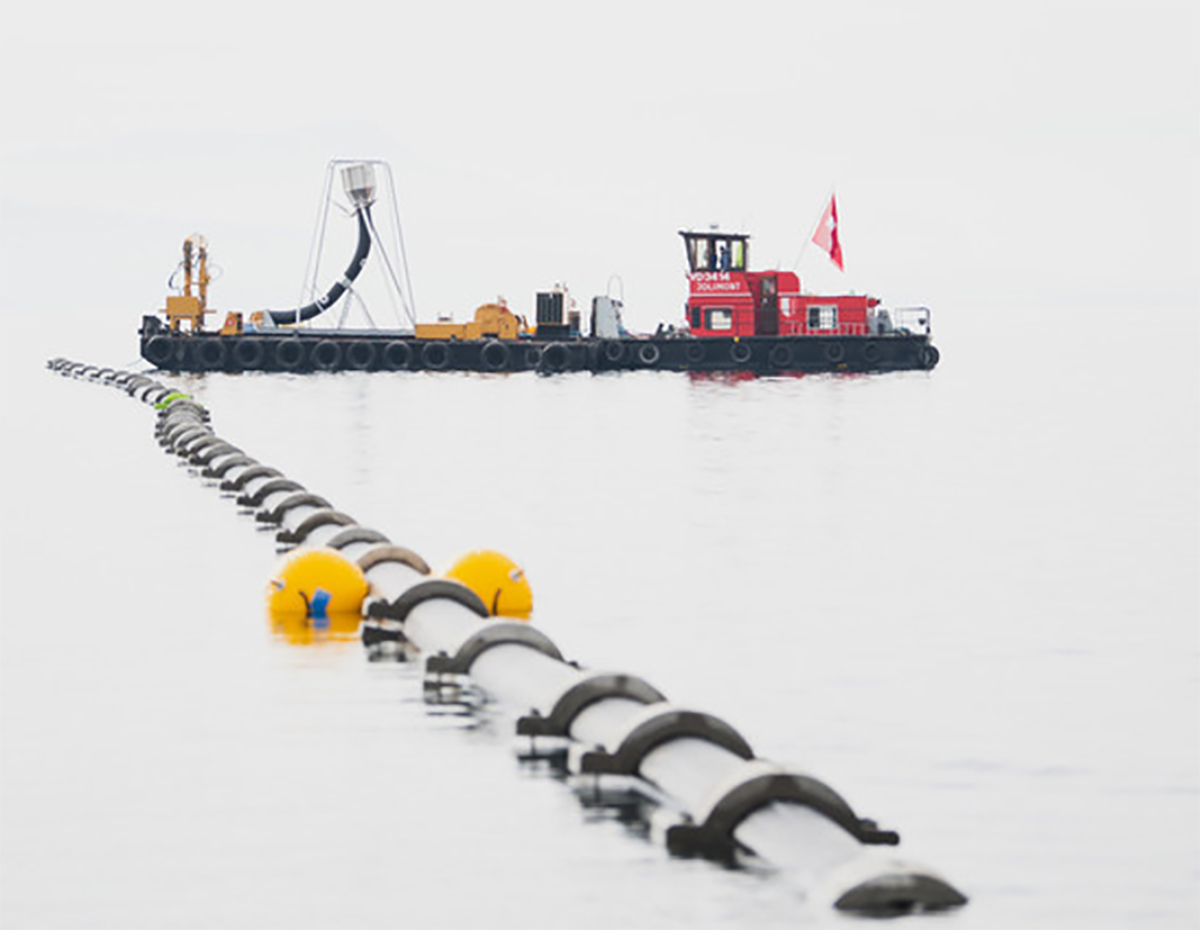
The preassembled pipeline was towed 20 km across Lake Geneva to the site. Photo courtesy of Hydrokarst Swiss.
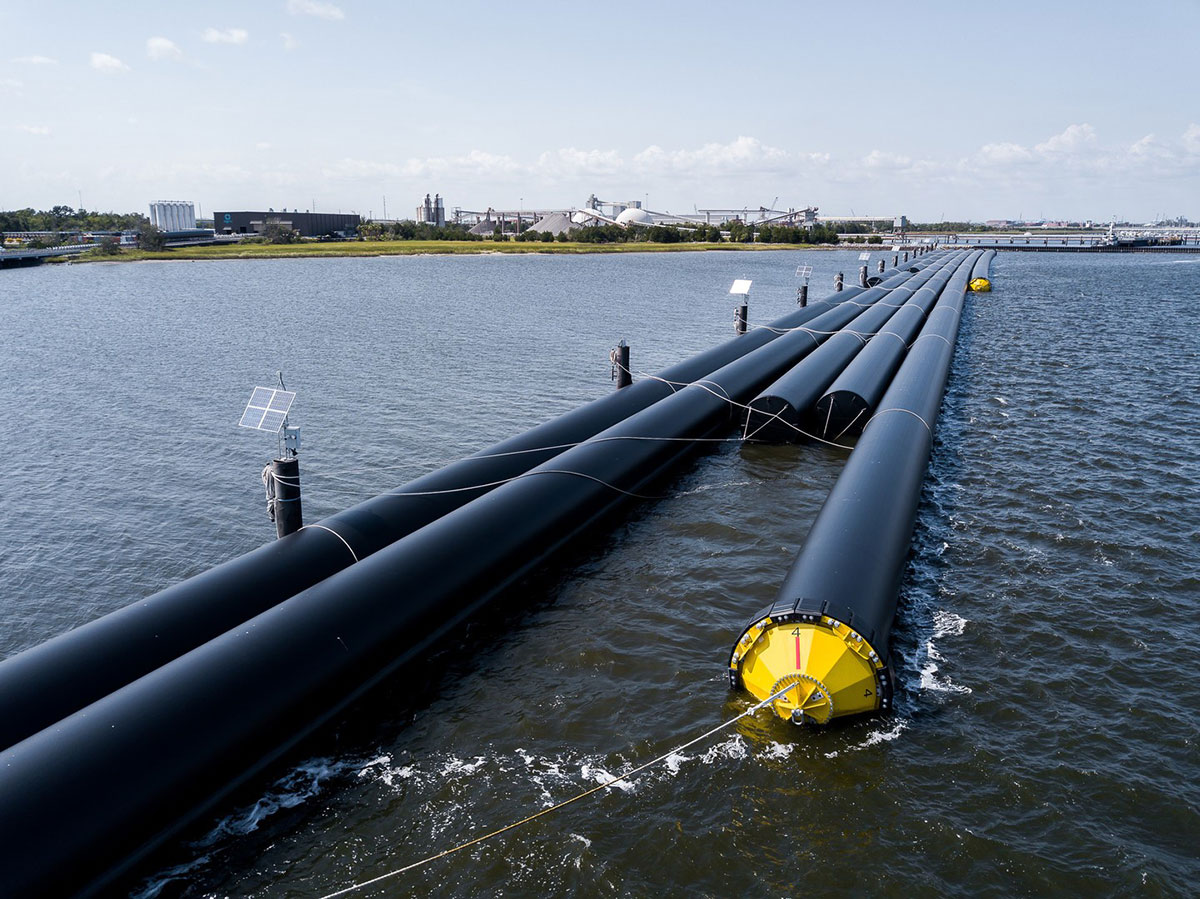
AGRU manufactures OD 24–63″ PE 4710 pipes and up to OD 137″ PE 100-RC pipes from its state-of-the-art facility in Charleston, SC, USA. Photo courtesy of AGRU.
The intake and outfall pipelines for the Centre Patronal facility’s heat pump were completed in March 2021, using about 800 m of piping. The new facility can now use the water in Lake Geneva to cool and heat its building with improved efficiencies.
Hydrothermal heating systems are gaining traction also in the United States, with the Washington Post reporting several use cases in New York and stating that geothermal heating is possible in all U.S. states and territories.
“Water from Lake Geneva used to heat and cool buildings,” House of Switzerland, https://houseofswitzerland.org/swissstories/environment/water-lake-geneva-used-heat-and-cool-buildings.
“The almost invisible machinery that uses Lake Geneva to heat 400 homes,” Le News, https://lenews.ch/2016/09/24/the-almost-invisible-machinery-that-uses-lake-geneva-to-heat-400-homes/.
“Geothermal heat pumps are among the most earth-friendly home energy sources, experts say,” The Washington Post, https://www.washingtonpost.com/business/2022/03/29/home-geothermal-heat-pumps/.
Yuse Lajiminmuhip is head of marketing at AGRU America, Inc. For more information, contact AGRU America, Inc. at 500 Garrison Road, Georgetown, SC 29440-9680 USA; phone (800) 373-2478, fax (843) 546-0516, info@agruamerica.com or www.agruamerica.com.