Heavy Equipment
by Dr. Ted Trautman, PLASKOLITE
perator safety is paramount on the job site when operating heavy equipment. Heavy equipment cabs are purposely designed with clear lines of sight for manipulating machinery in taxing work environments. High optics and low distortion are critical for working long hours, but high visibility cannot trump operator safety. When hazards such as tree limbs, rocks and projectiles from equipment failure are present, impact-resistant glazing is a critical for protecting operators.
Polycarbonate (PC) sheet offers high impact resistance, low distortion and high clarity, making it the material of choice for window glazing in heavy equipment applications such as forestry, construction, agricultural, mining and forklifts.
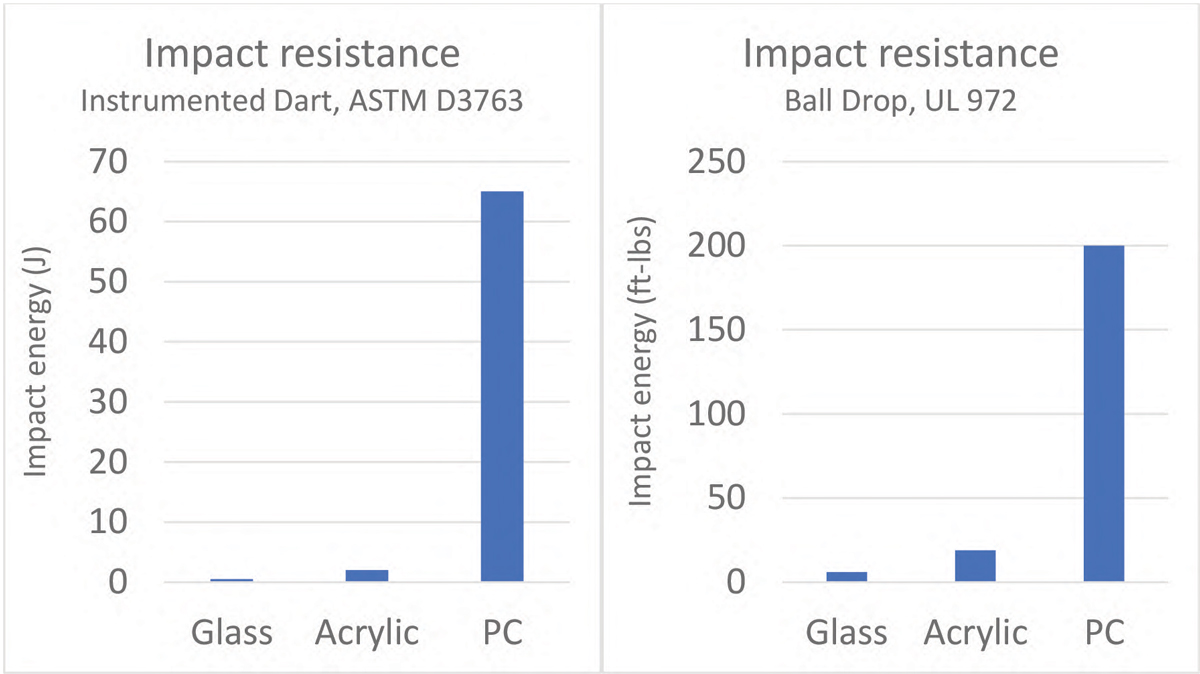
A comparison of impact resistance of glass, acrylic and PC using two common tests.
An advantage of polycarbonate safety glazing is its resistance to breakage during most impact events, leaving the window operable and the equipment in service. Laminated safety glass glazing often shatters during an impact event. The limited line of sight and sharp shards present a hazard for continued operation.
Multilayer polycarbonate laminates offer even higher impact resistance than monolithic sheet. Having been tested to a range of impact events in containment and forced entry test protocols such as ASTM F1233, ASTM F1915, H.P. White TP 0500 and UL 972 demonstrates polycarbonate’s robust resistance against repeat, varied and heavy impact events. Polycarbonate laminates are also tested for ballistic performance, stopping high speed projectiles. Equipment failures in the tree harvesting and mining applications can create high speed projectiles, essentially ballistic projectiles. Cab structures have successfully passed stringent falling object protective structures (FOPS)/roll-over protective structures (ROPS) requirements while using both monolithic and laminated polycarbonate safety glazing.
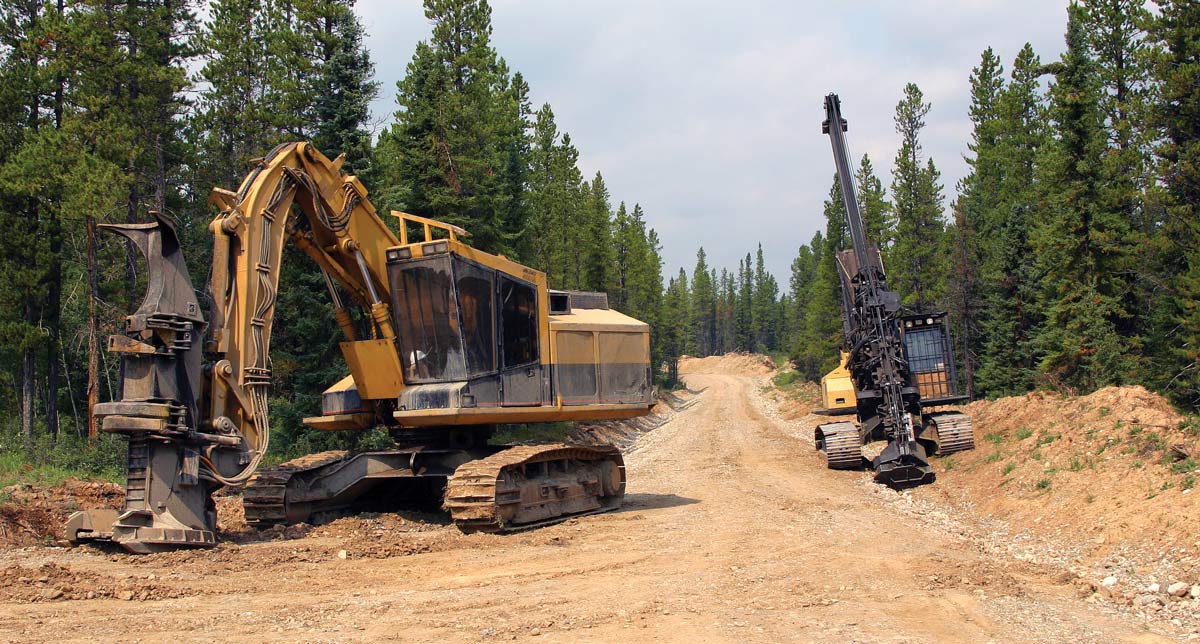
TUFFAK® Abrasion Resistant hard coat provides clear line of site even in harsh environments.
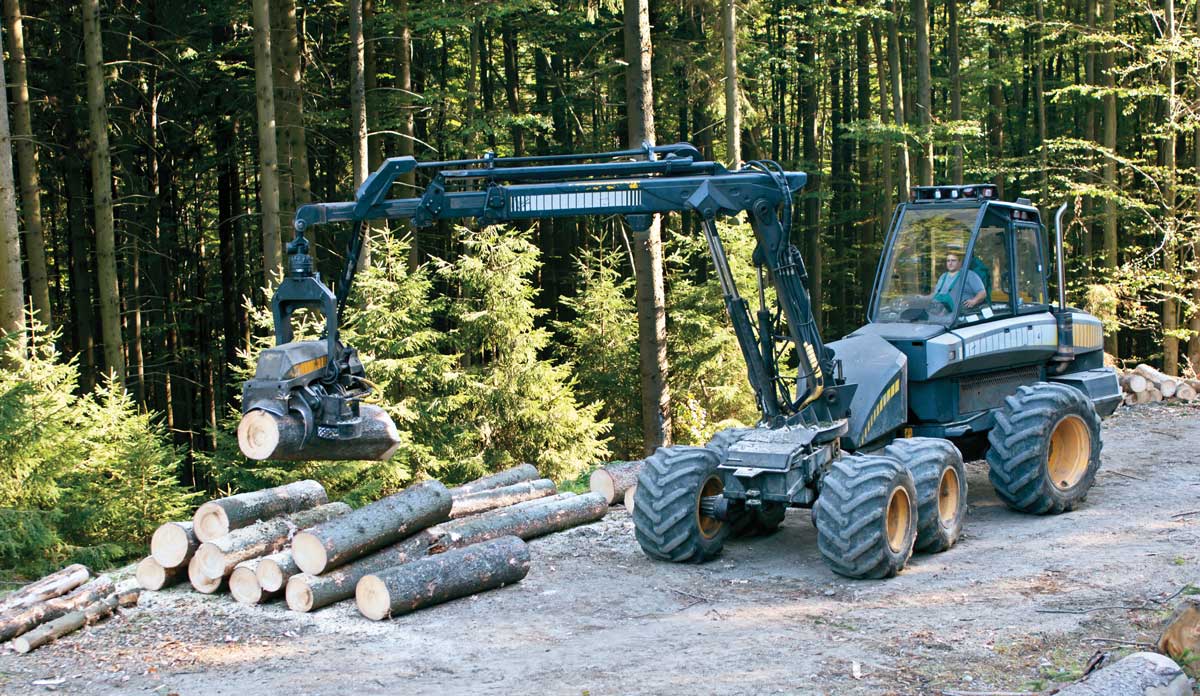
HYGARD® CG500 offers proven impact resistance for operator safety.
Polycarbonate sheets also are certified under federal rail transportation standard FRA 49 CFR 223, an impact safety glazing specification for locomotives, passenger cars and cabooses. Thick gauge 0.500″ PC sheet passes both TYPE I and II against heavy concrete masonry drop tests. In addition to impact resistance testing, polycarbonate sheet complies with Federal Railroad Administration (FRA) standard for flammability, smoke and toxic gas evolution during burn testing. This ensures passenger safety should a fire take place in an enclosed rail terminal or tunnel.
Polycarbonate sheets used for glazing in the transportation industry are protected by a hard-coat surface that is resistant to marring and holds up to frequent cleanings. The coating also provides outstanding chemical resistance to various cleaners and splash contact from gasoline and diesel fuels. In addition, the coating provides lasting outdoor weathering performance to resist discoloration and hazing from the sun’s harmful UV rays.
At the same thickness, polycarbonate sheets are half the weight of laminated safety glass. Polycarbonate’s impact performance can allow for thinner and even lighter sheets or laminates than impact rated glass.
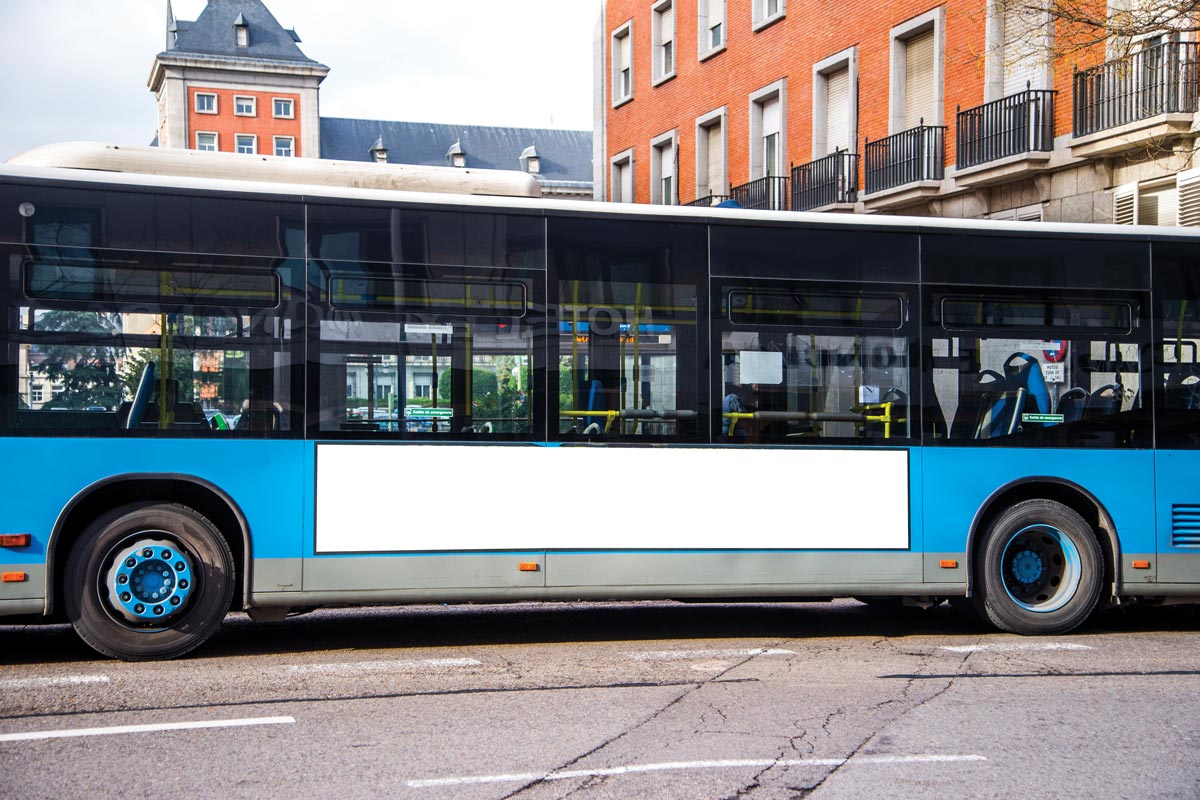
TUFFAK® BG meets DOT/FMVSS 205/ANSI Z.26.1 AS-4 requirements.
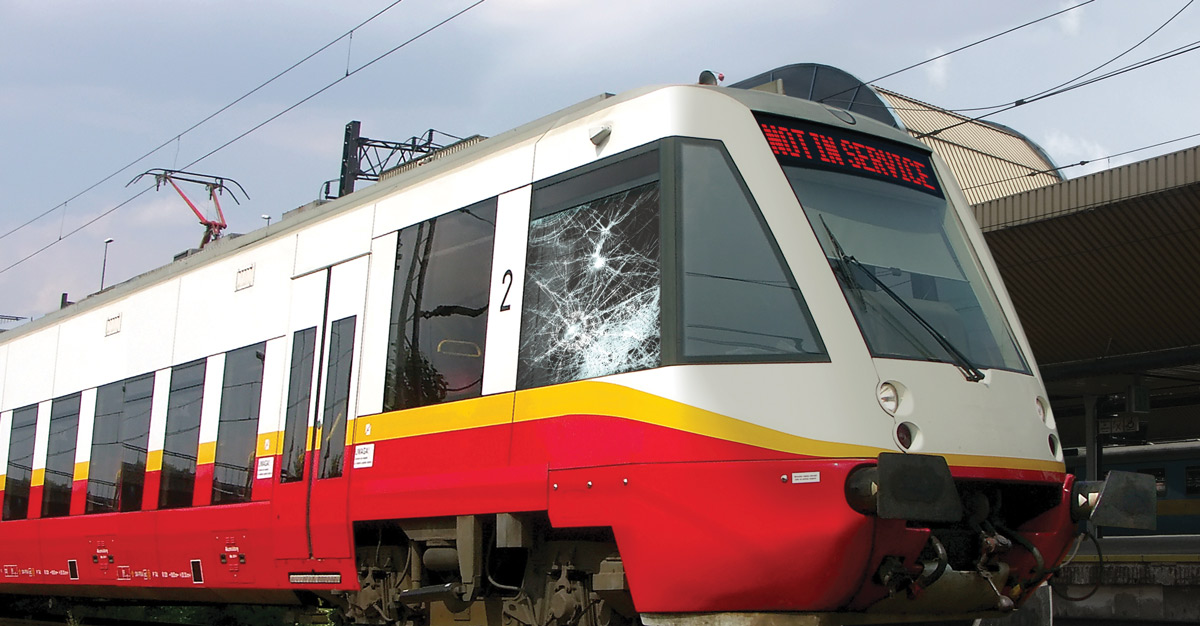
TUFFAK® TG meets stringent US Federal Railroad requirements for impact, ballistic and flame, smoke and toxicity performance.
An additional benefit when using polycarbonate sheets in replacement glazing is the ease of fabrication. Polycarbonate sheet and laminates can be cut to any and all window configurations with standard saws or routers. This eliminates downtime versus ordering custom sized laminated glass or the high cost of inventorying the range of glazing types and sizes. Shipment of polycarbonate is easy by comparison with essentially no concern for breakage on its way to the end user.
Gone are the days of operating heavy equipment through metal cages or expanded metal screens over glass windows. Polycarbonate monolithic and laminate glazing solutions allow for high visibility without sacrificing critical operator safety.
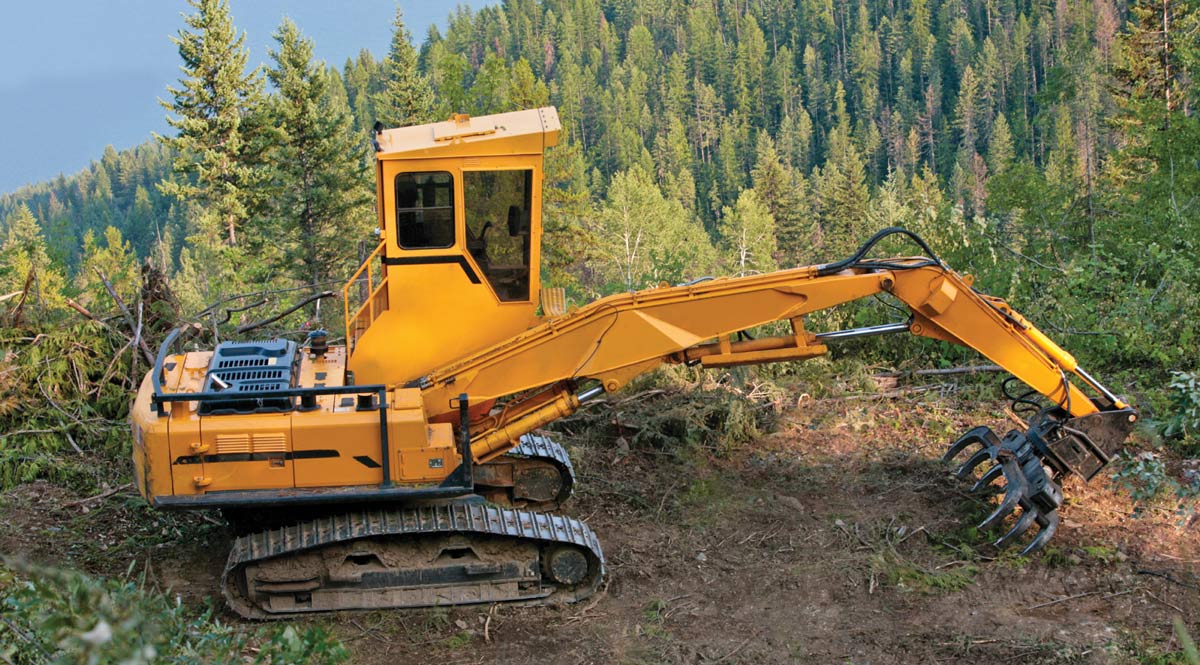
TUFFAK® HV provides low optical distortion and advanced hard coat technology.
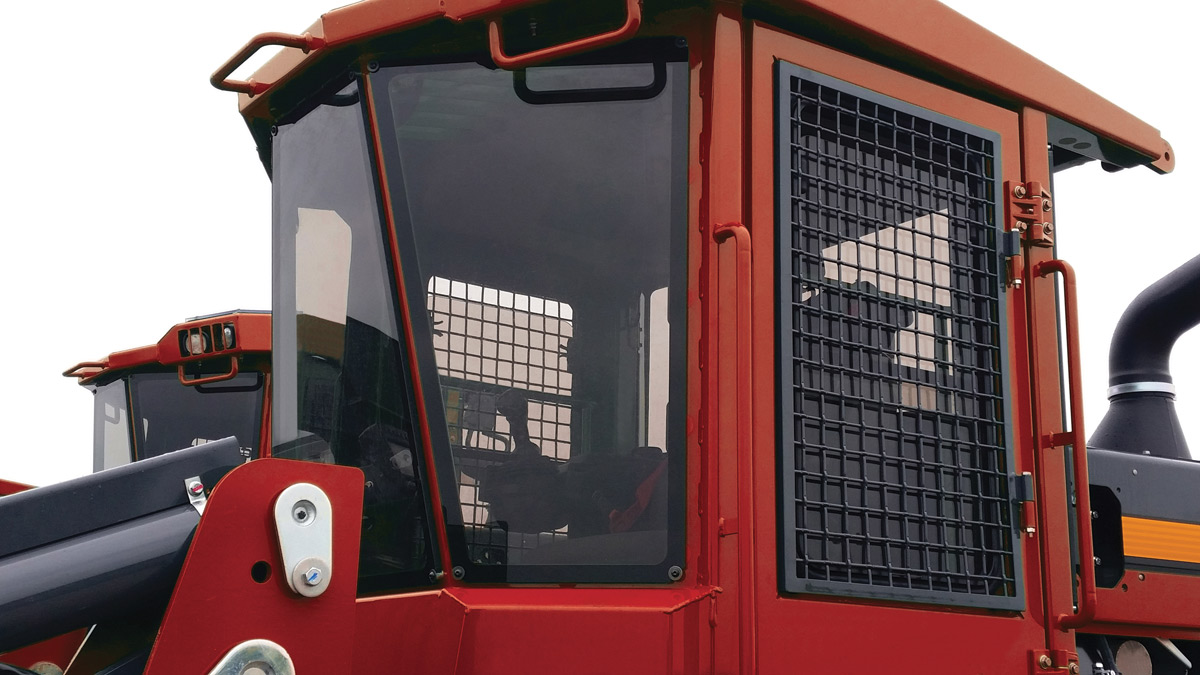
HYGARD® Glazing eliminates wire cages in high use windows.
Dr. Ted Trautman is technology director for PLASKOLITE. For more information, contact PLASKOLITE at 400 West Nationwide Boulevard, Suite 400, Columbus, OH 43215-2394 USA, (800) 848-9124 or (614) 294-3281, fax (877) 538-9754, plaskolite@plaskolite.com or www.plaskolite.com.