Showcase
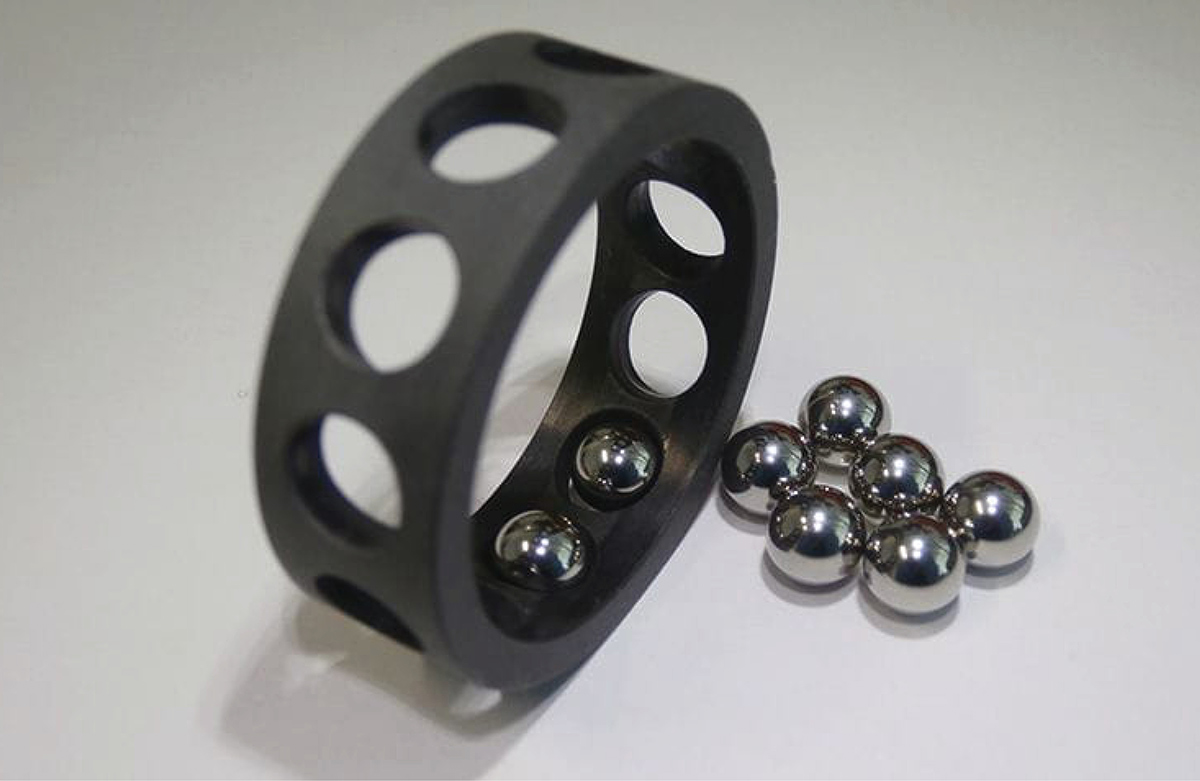
Through this project Ensigner has launched a new higher-performance plastic named TECASINT 8591 for applications in the space industry, including ball bearing cages in satellites. Use of PTFE with special lubricants and fillers provides the new product with outstanding self-lubrication properties under conditions found in space.
Satellites used for weather, communication and earth observation circle in low Earth orbit (LEO). These satellites use sensors, antennas and reflectors that unfold when the satellites reach their orbit. The mechanisms for unfolding these systems must retain long-term functionality under the conditions found in space. Included in these mechanisms are ball bearings that must maintain a constant ball bearing torque over the course of at least 20 million bearing revolutions. This amount of friction places a high demand on these components.
It has been found that ball bearing cages made with TECASINT 8591 feature a lower ball bearing torque compared to other materials and undesired stick-slip effects do not occur. Additionally, the material complies with outgassing limits stipulated by ECSS Q70-02 and exhibits low levels of post-shrinkage. TECASINT 8591 also demonstrates excellent frictional properties at cryogenic temperatures and under vacuum.
TECASINT 8591 has been approved by ESA as an alternative to the current single-source material PGM-HT. www.ensingerplastics.com
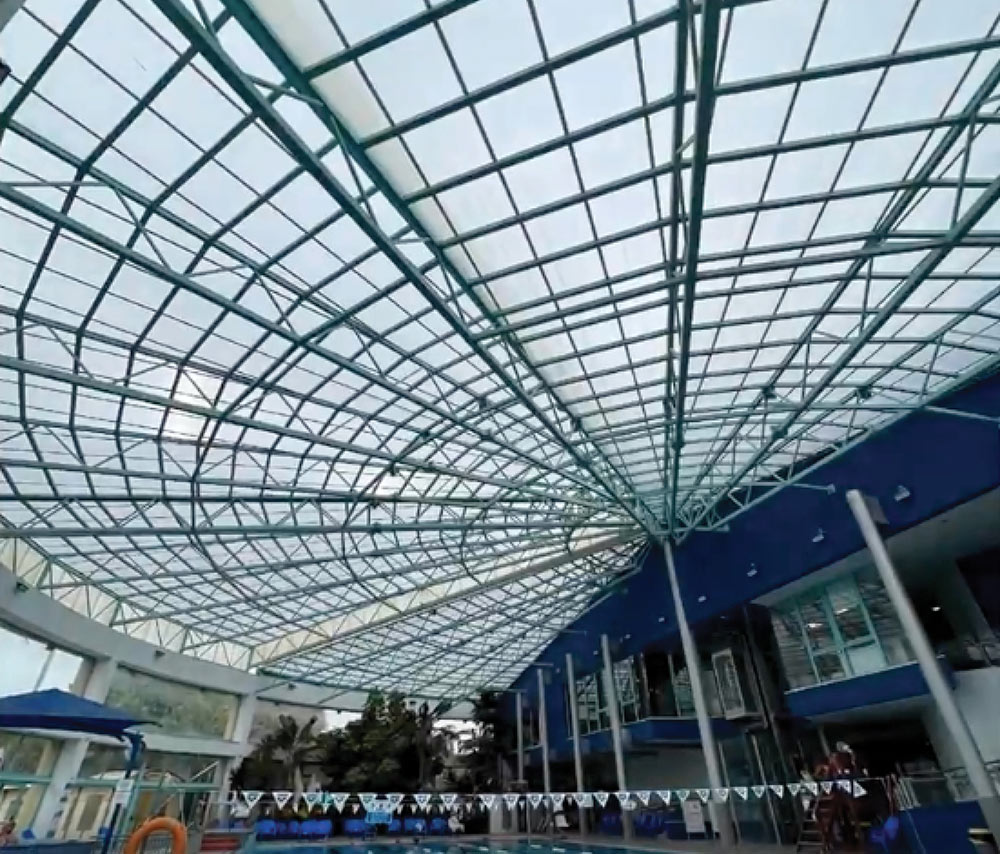
PLASKOLITE’s Titan Sky (TSK) sheets in 16 millimeters thickness were selected for the project. TSK sheets are made from transparent PC HCP, offering durability and clarity. The transparency and clarity of the sheets allow park-goers to enjoy the sunlight, even when the roof is closed. The internal cross-brace structure of the sheets also increases their strength and durability.
The custom fitted sheets were up to 25 meters long and cut into triangles with varying widths. The custom triangle sheets were used to give the roof a curved edge.
Transporting the oversized sheets required custom-designed truck equipment with an extendable cart and rear steering.
PLASKOLITE collaborated with Roof Dagan to complete the oversized project. www.plaskolite.com
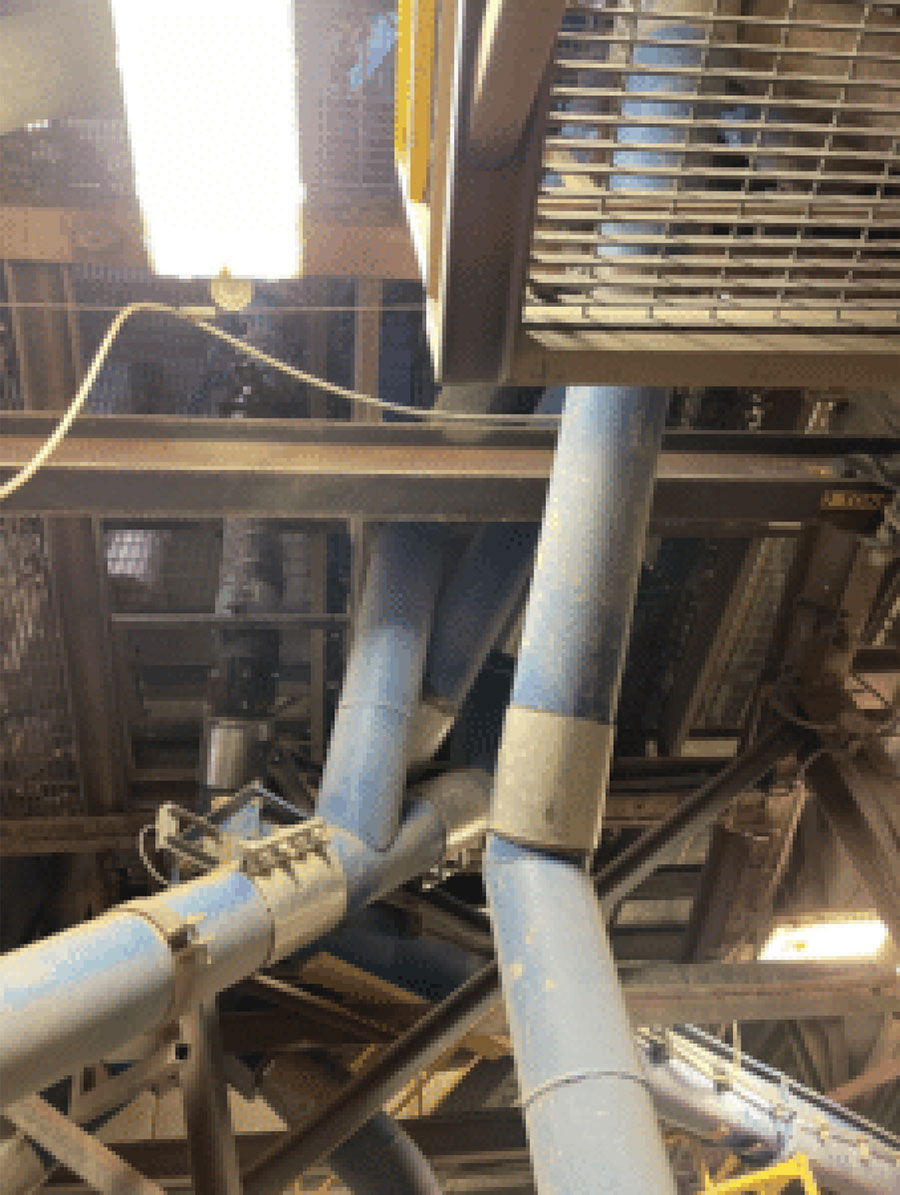
Progressive Planet Products piping system is responsible for moving high quantities of minerals, including diatomaceous earth, zeolite and calcium bentonite. Under the abrasive conditions required to transport these specialty minerals, Progressive Planet Products’ original carbon steel pipes only lasted 18 months. The company began working with Redwood Plastics and Rubber to create a longer lasting solution for their piping system.
Redwood selected pipes made from Redco™ 430 (90A) urethane for the project. Redco 430 (90A) urethane touts resistances to weather, cuts, impingements and impacts, making it ideal for a tough environment like Progressive Planet Product’s where high abrasion resistance is required to transport minerals.
The piping system supplied by Redwood Plastics and Rubber has been a mainstay at the manufacturing site for over nine years, and is still used to this day, outlasting the previous carbon steel system by many years. www.redwoodplastics.com