Putting Polycarbonate Glazing to the test
Security
quick look at the latest numbers from the National Centers for Environmental Information will tell you a story worth listening to. In 2015, There were five extreme storms in the United States with a cost of damage totaling over US$1 billion. Just two years later, that number more than doubled with 12 catastrophic national storms. In 2020, the total number of extreme windstorms in the United States reached 20. Exponential is the best word to describe this upward trend. While we are still working on ways to mitigate the financial cost of extreme windstorms, we can now provide better safety, minimizing the impact to human life thanks to performance plastics.
Eight years ago, International Building Code (IBC 2015) standards began requiring new and improved safe rooms of protection for essential buildings. These buildings include schools, hospitals, police stations, fire stations and emergency operation centers with occupancy over 50 persons in areas that face extreme weather with over 250 mph wind. These safe room shelters should be large enough to hold everyone in the building and withstand wind and debris from EF5 tornadoes or Category 5 hurricanes. A key component in these structures is window protection.
Glass windows are some of the weakest links in the severe weather protection chain, but windows are also an important part of the health and well-being of students and employees in these buildings. Past protection included windowless structures, or steel shutters that required time and effort to secure shut assuming time would allow before the storm arrives.
By creating glazing that consists of multiple layers of glass and polycarbonate laminated together combined with frames that provide adequate support, these buildings can maintain all the clarity and sunlight that pure glass can provide, while being able to withstand 5,000 FT-LB of force.
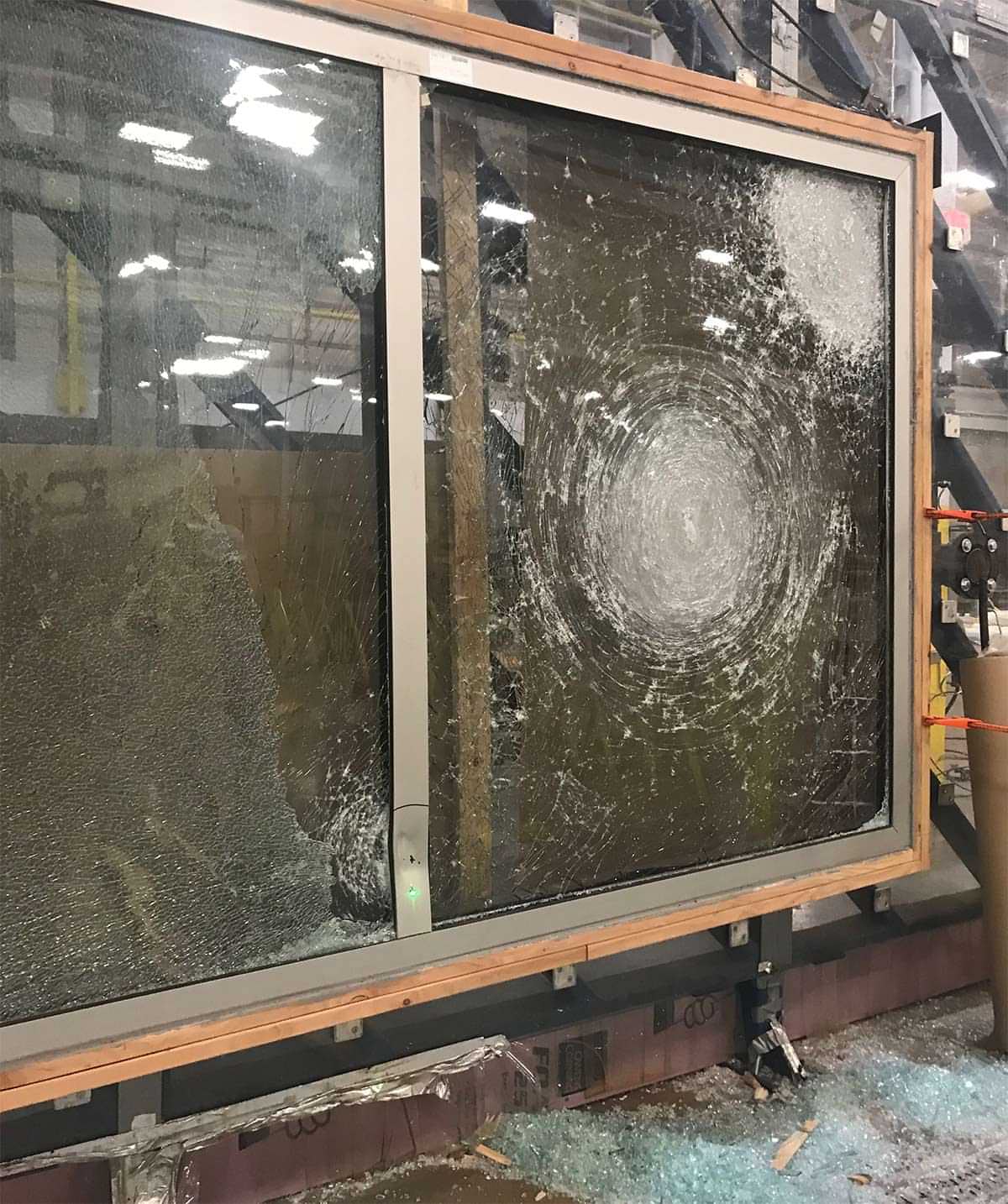
Polycarbonate laminate undergoing impact testing. (Photo courtesy of Insulgard Security.)
“First, the glazed windows and doors must go through structural pressure testing. Our testing consists of +292 and -368 psf (pounds per square foot). This structural pressure testing simulates the winds associated with an EF5 tornado and to pass the testing the glass must not break and remain intact and secure in the opening.”
Once the polycarbonate/glass laminate passes the structural pressure testing it then undergoes debris impact testing.
“The most common debris found within a tornado is lumber from homes and structures that have been destroyed. As a result, debris impact testing for these components consists of a 15 pound wood 2×4 traveling at a speed of 100 mph,” Gerry continues.
This debris impact testing is simulated by an air-compressed canon that shoots the wood against the glazed windows. The polycarbonate/glass must not only withstand prevent penetration from the 2×4 and related debris but it cannot so much as allow spall shards of glass to penetrate the witness panel which is comprised of a piece of craft paper just 5 inches from the interior of the polycarbonate/glass window.
“If any spall of glass penetrates that craft paper, it’s a failure,” added Gerry. The 0.125 inch polycarbonate sheet on the interior/safe side of the glazing the center of this makeup is essential to pass the debris and glass spall test. It provides an inner layer that acts as a spall shield to absorb the debris’ impact and prevent shattering glass that could further damage property or the safety of those lives inside the building.
Gerry went on to clarify special consideration for hurricane-resistant structures, “If these products are to be used in hurricane shelters as well, cyclic testing per ASTM E 1886 must be conducted on the windows and doors that have already been through this initial testing. Additional cyclic testing for hurricane shelters consists of a total of 4,500 positive and negative cycles of wind pressure simulation ranging from 0 – 213 psf, with each cycle taking 2 – 5 seconds.”
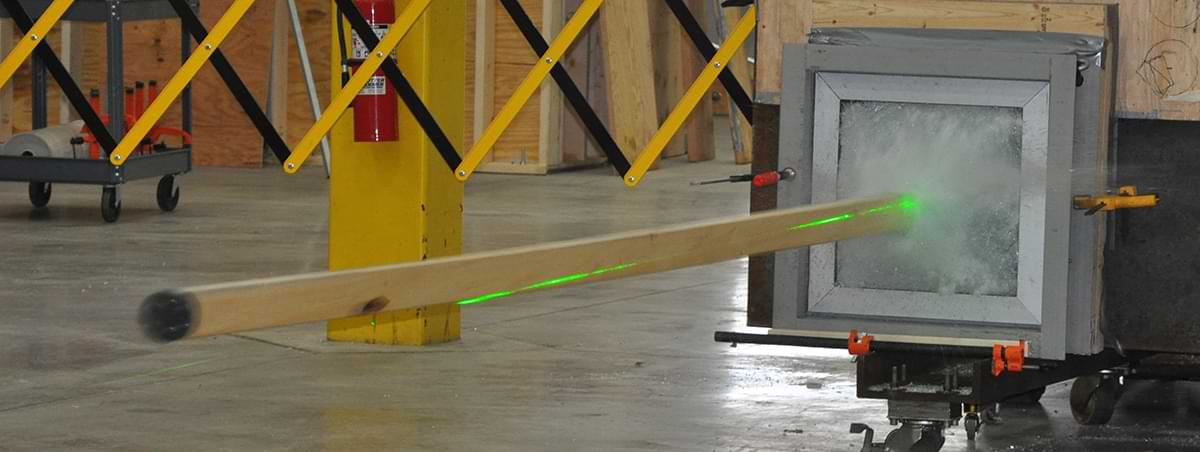
Wood is launched by an air compressed cannon at polycarbonate/glass laminate to simulate tornado debris. (Photo courtesy of Insulgard Security.)
In addition to meeting the storm shelter requirements, these windows also meet UL752 level 3 ballistic protection which consists of 3 shots of a 44-magnum handgun in a triangular pattern. To pass the testing, the bullets cannot penetrate but in addition, just like with the debris impact testing, no glass spall can come to the inside. For an all-glass product to pass UL752 level 3 ballistic testing the makeup would need to exceed 2 inches. By adding polycarbonate to the makeup, the glazing thickness can be reduced to 1 inch. This level of impact control used for weather protection and ballistics is also security protection against forced entry. No human can provide the level of impact (5,000 lbs. per foot) that is being tested for tornado impact.
As extreme weather events continue to increase worldwide, buildings must maintain the most state-of-art protection available to allow uninterrupted work and safety in our most essential buildings. Polycarbonate glazing is thinner, lighter weight, maintains the light transmission clarity of the average commercial window and still stands up to rigorously against the pressure debris impact often found in tornadoes and hurricanes. With all these benefits, it’s easy to see why polycarbonate glazing on glass is the material of choice for so many safe rooms required by IBC-2015 for these essential buildings in areas of 250 mph winds.
Gerry Sagerman leads sales development for Insulgard Security. For more information, contact Insulgard Security at 1291 Rickett Road, Brighton, MI 48116-1832, USA, or by phone at ((810) 844-0776, fax ((810) 844-0920, email info@insulgard.com or www.insulgard.com