oday, there exists a desire — from either a creative or a business perspective — to manufacture products with rigid thermoplastic, using a process commonly referred to as plastic fabrication. This term describes a variety of procedures and processes. This article focuses on describing the process of the joining/welding of rigid thermoplastics using hot air tools, specifically hot air portable extrusion welders. There is another popular fabrication process using hot air hand tools that lends itself to certain situations and applications, but that’s a subject for future consideration.
The temperature of the pre-heat and the melt are controlled with varying levels of precision depending on the capabilities of the extrusion welder, with higher quality welders offering digital and individual controls for each. The speed is limited to:
- The output/size of the welder
- The amount of melt produced
- The physics of the welding process (you cannot go too fast or the pre-heat will not be sufficient to melt the substrate)
- The correct amount of pressure must be applied to force the melted material together, but not so much as to push the melt away from the substrate
The thickness of the material being welded determines the required size and capacity of the extrusion welder, while some thermoplastics such as polyvinylidene fluoride (PVDF) and polyvinyl chloride (PVC) require more precise temperature control and resistance to corrosion of the internal components of the extrusion welder.
The most common types of thermoplastic being welded in the field using hot-air portable extrusion welders are polypropylene (PP), polyethylene (PE), PVC and PVDF. Each one of these chemistries has subgroups of various types, creating an alphabet soup of acronyms, and although I have minimum word count to achieve for publication, I am remaining true to the simplicity theme and limiting this discussion to broad terms such as PP, PE, PVC and PVDF.
Each thermoplastic material has unique welding characteristics and specific temperature ranges required for the preheat and the melt to achieve a proper weld. PP and PE are the most common and the most forgiving with a comparably wide range of melt temperatures and a similar pre-heat temperature. They are also the least corrosive to the internal parts of the hot air extrusion welder.
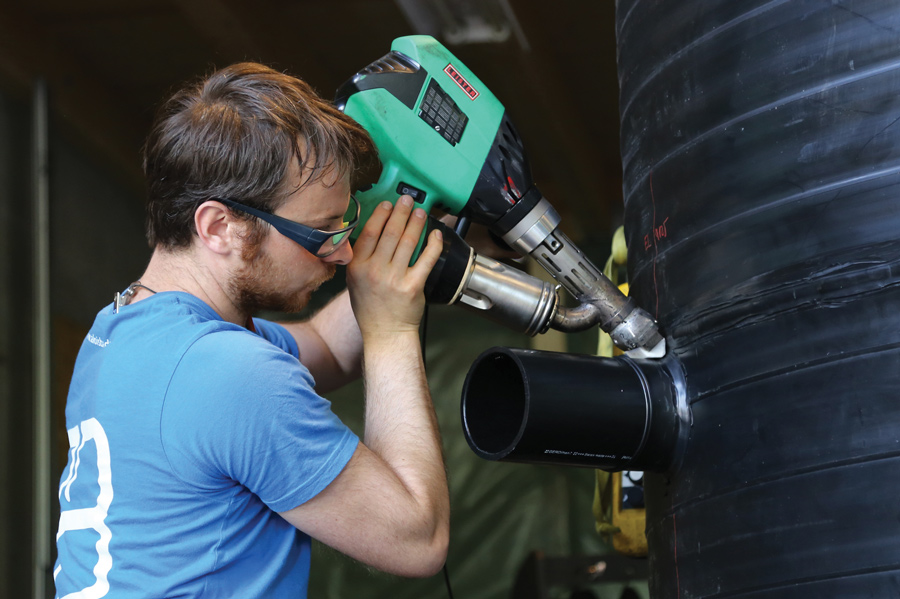
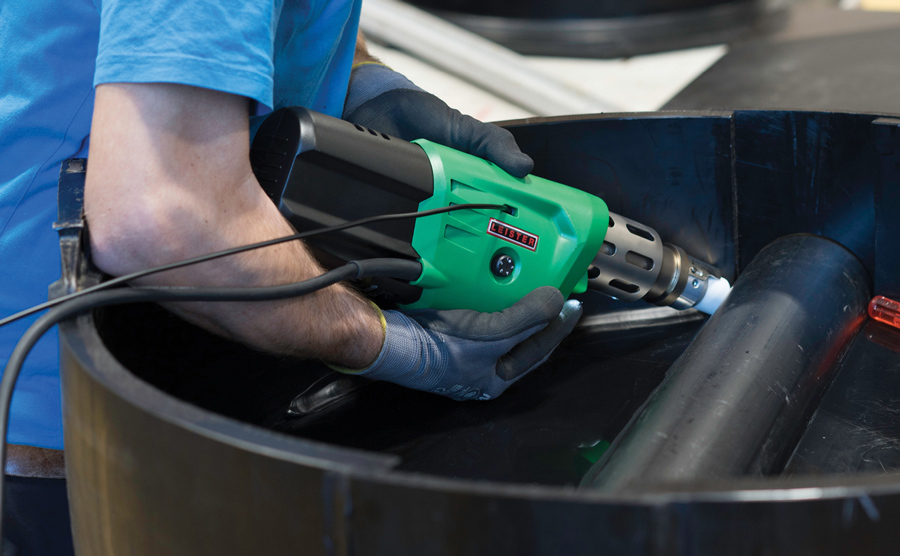
So ends this high-level description of the hot air extrusion welding process. I hope you found it informative and useful.