Showcase
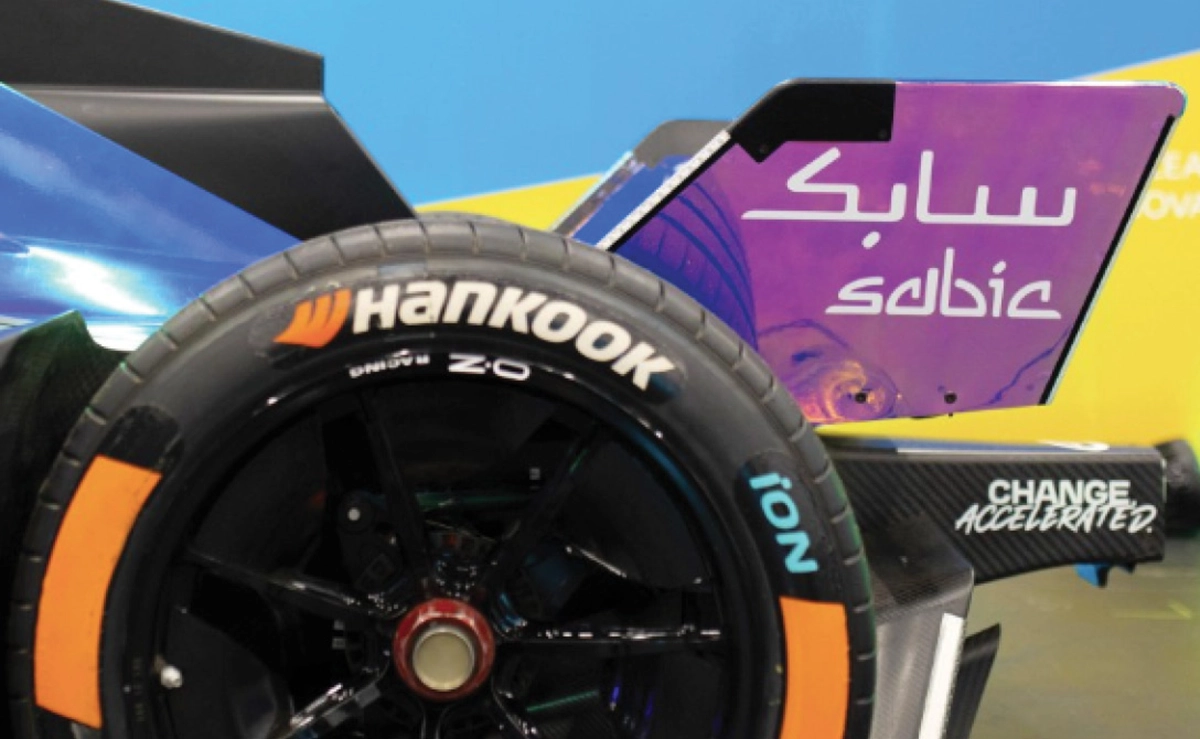
SABIC via LinkedIn
Developments from SABIC include front wing endplates formed with a 3D printing process. These wings help reduce drag and improve the vehicles downforce and stability.
Wind deflectors made with coated thermoplastic sheet produces with an extrusion process using SABIC LEXANTM resin help improve airflow and decrease drag.
SABIC’s CYCOLOYTM (PC/ABS) resin has been implemented in wheel fins to said break cooling and reduce drag for better stopping power.
The GEN3 model of the Formula E car can reach speeds of over 200mph/322kph and offers ultra-high speed charging capabilities, all while utilizing sustainable high-performance materials that are recyclable, lighter and uniquely flame-retardant. www.sabic.com/ff
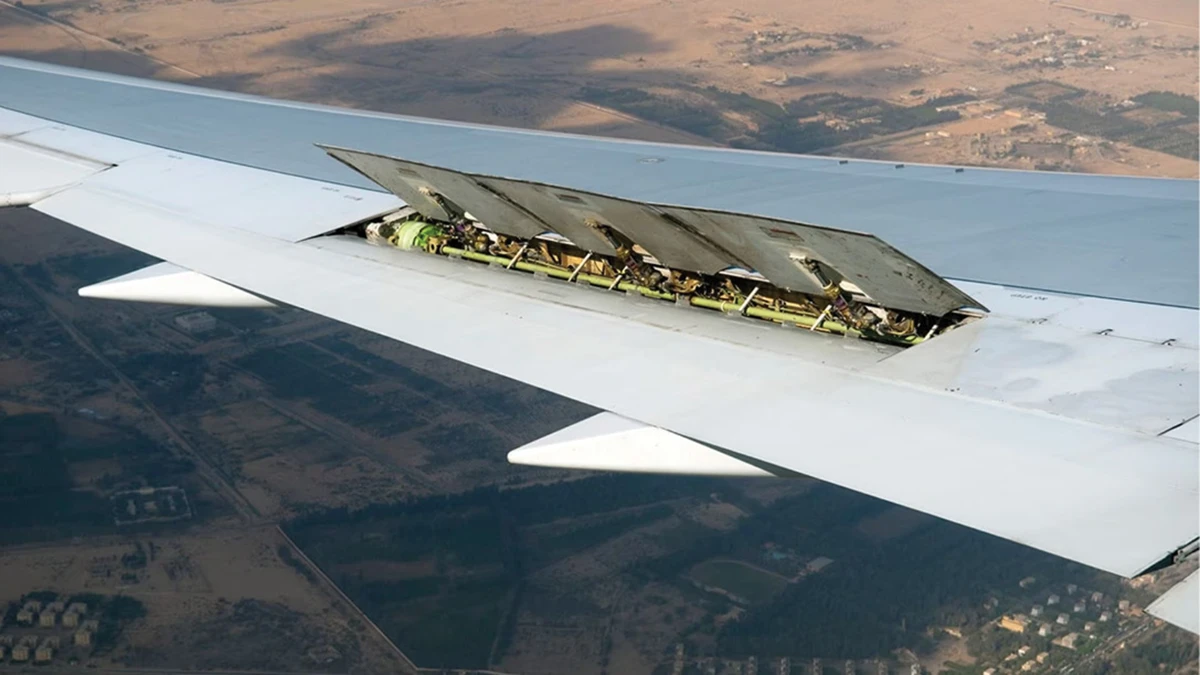
Mitsubishi Chemical Group
An aerospace manufacturer was challenged to reduce fuel consumption and CO2 emissions when developing a new aircraft. The manufacturer selected a flexible, lightweight composite material with an aluminum structure for the wings. To ensure continual wing flexibility and structural integrity, the selected material would require monitoring, lubrication and maintenance regularly.
Mitsubishi Chemical Group found a simplified, self-lubricating plastic solution to replace the need for the previously selected labor-intensive part. Implementing Duraton® T4301 PAI self-lubricating wear strips for wing flaps resulted in a lighter plane with a lower risk of failure and reduced maintenance requirements.
The single self-lubricating plastic wear strip is integrated between mating surfaces in the wing flaps. Extensive testing was conducted to ensure the strip met all industry requirements as well client goals for improved fuel efficiency and reduced emissions. Since its installation on the client’s aircraft the plastic solution has been adopted by other original equipment manufacturers in the aerospace industry. www.mcam.com
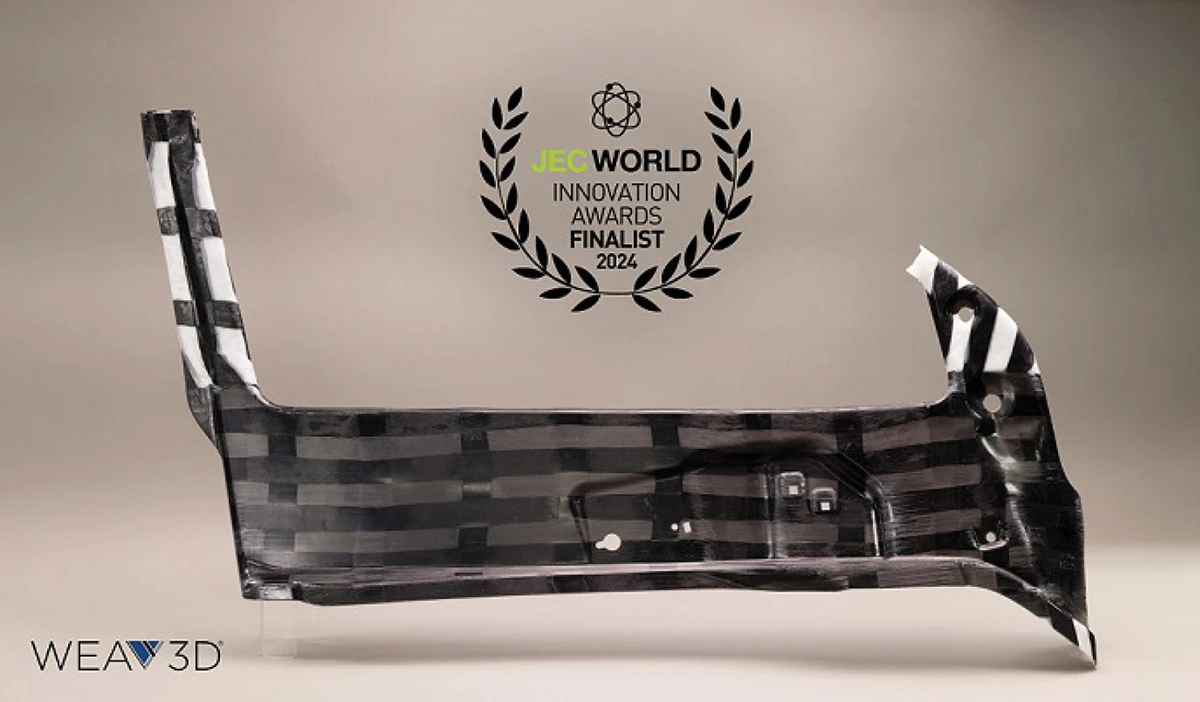
WEAV3D via Braskem
The partners combined WEAV3D composite lattice reinforcement with Braskem polypropylene to craft a lighter, less expensive thermoplastic alternative to conventional organosheet. This innovation opens up new opportunities for the replacement of sheet metal structures with thermoplastics within vehicles.
The benefits of using Braskem and WEAV3D’s door component include a final part weight reduction of approximately 23%, cost reductions of approximately 50% and increased sheet yields from 25-45%, by weight, resulting in a 62% reduction in trim waste.
“We continue to be very excited to offer our clients innovations and partnerships around high-performance polypropylene materials utilizing the WEAV3D lattice technology after launching this project in 2023. We are honored to be recognized as a finalist for the JEC World Innovation Awards. As the automotive industry continues to roll out new electric vehicle designs, it requires automakers to re-think the vehicle design with cutting-edge performance materials and consider more sustainable end-of-life solutions. The initial conversion process focus has been on thermoforming to leverage large parts production; however, the WEAV3D technology can also be applied to injection molding of more complex parts. With significant improvements in lightweighting, reduced costs, and higher material efficiency, combining Braskem’s PP portfolio with WEAV3D composite lattices provides a ‘win-win’ in terms of enhanced material performance and a more sustainable environmental impact, including the integration of natural fiber options,” Amanda Zani, Technology Platform Manager, Braskem commented in a press release.
The Braskem-WEAV3D prototype part was on display in the JEC Innovation Planets section of JEC World in Paris, France from March 5 – 7, 2024. JEC Group is a non-profit organization dedicated to globally promoting composite materials and their many applications. www.braskem.com/utec
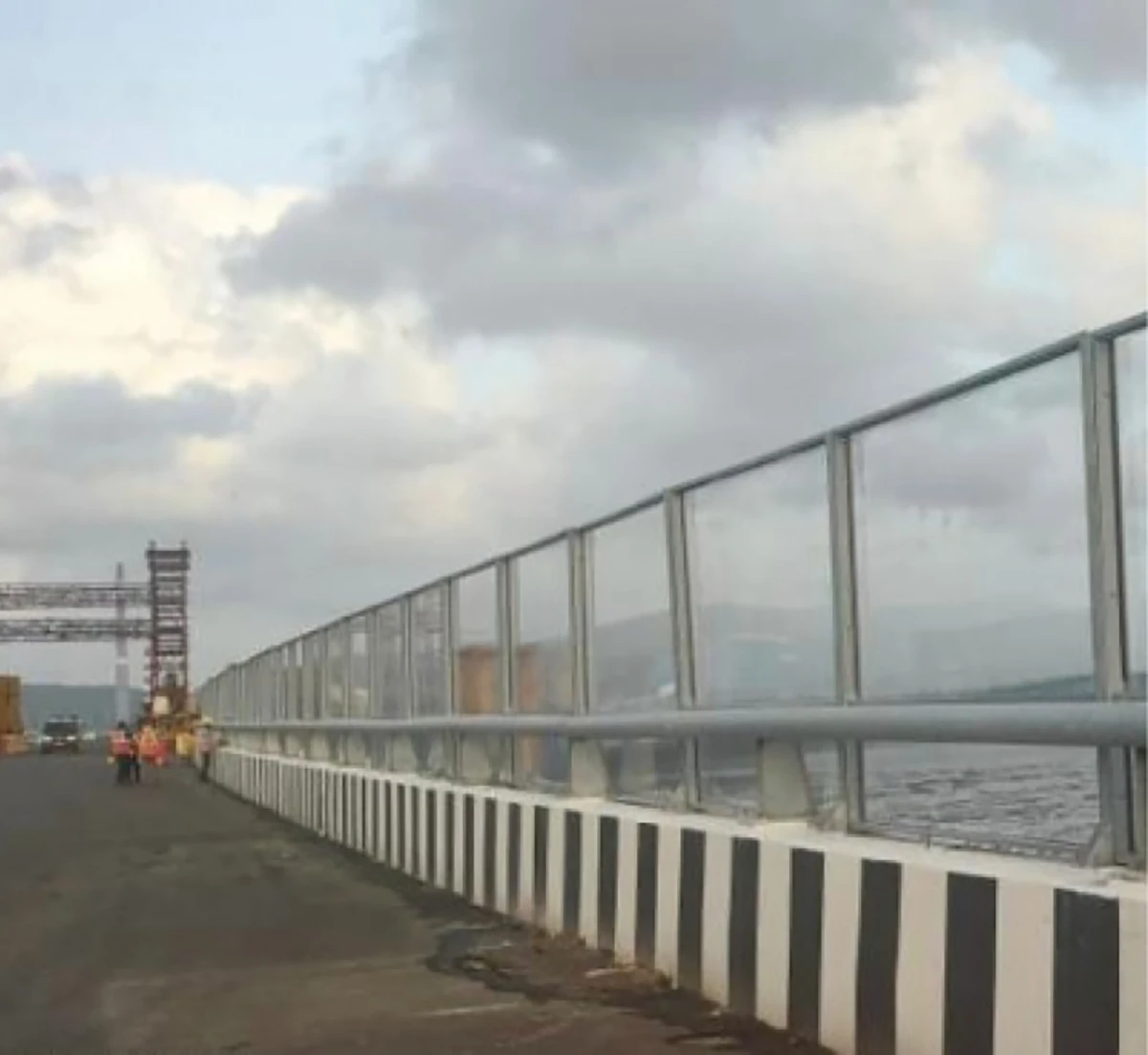
The six-lane sea bridge is the longest in India, stretching more than 13.5 miles/21.8 kilometers long with a 10.25 miles/16.5 klometers long sea-link. The six-lane MTHL is expected to see the transit of more than 70,000 vehicles daily. The high volume of traffic requires a high level of durability and wear resistance for all materials used in the project. www.tilarapolyplast.com