SpecialFocus
Fabrication
by Allan Harari, PT. Margacipta Wirasentosa
ou can get technical about fabricating see-through substrates, but whatever the process, tools, mechanics, adhesives, compounds or materials, the results are ultimately governed by the aesthetics.
Machine and medical device covers, equipment guards, testing equipment, aquariums, terrariums, emporiums, display stands and boxes for food or cosmetics; each of these must offer a clear view without imperfection. This article focuses on fabricating with the most common see-through substrates.
The Materials
Cell cast acrylic is a harder, higher molecular weight material, that provides superior optical clarity, greater surface hardness and machines cleanly; especially with sharp carbide tooling in the hands of a skilled fabricator. Certain manufacturer’s offer “softer” cell cast formulations without sacrificing its optical characteristics. Cast acrylic is best suited for signs, protection guards requiring durable and clear visibility, water tanks, etc. Cast acrylic’s high optical quality is also ideal for high-end retail displays, especially at ½ inch or greater thicknesses.
Extruded acrylic is softer, heats up and bends faster but during machining may “gum up” the works without more cooling or airflow around the cutting tool. High volume, flat panel, inexpensive items like brochure holders and displays are likely fabricated from extruded material, as well as applications requiring tight thickness tolerances. Extruded acrylic sheet is prone to shrinking along the extruded and expansion lines (sheet orientation). When bending or thermoforming, be aware of the extrusion direction of the acrylic for best results.
Polycarbonate (PC) is tough and found in many applications once made with glass that require higher impact resistance – eye protection, car headlamps, riot shields. However, PC requires high forming temperatures and is sensitive to certain solvents. Moisture content must be considered when forming polycarbonate since during the heating process, the moisture expands and has nowhere to evaporate. Pre-drying at, say 150 degrees, can help avoid unsightly bubbles. Line bending PC very slowly also helps, but adds production time and cost. Like extruded acrylic, be aware of PC’s orientation.
Fabricators will always face inconsistency in different sheet brands and types of materials along with the impact of weather conditions. Testing all aspects of fabricating see-through materials is essential.
The Masking
Paper is more durable for cutting parts on modern routers. Heavier paper is recommended for intense fabrication. You can draw on paper and the masking is held in place by more robust adhesive.
PE masking ages better than paper and is typically attached using static cling — easier to peel off but can melt under a laser. When cutting blanks for light fabrication like sneeze guards or panels, PE works fine as it’s easier to remove, especially if you need to peel back the masking and then reapply. Many fabricators prefer film for forming.
The Sticky
The variety of adhesives and solvents on a variety of materials for a variety of applications requires its own devoted analysis. Fabricators can suffer a lot of “trial and error” depending on their customer’s requirements and budget, which is easily revealed by the seams on a final product.
Acrylics can be easier to work with than PC, but consider cast v. extruded’s characteristics. Extruded acrylic has a lower softening point which accepts solvents quicker and reduces set time. For high quality projects, cast acrylic may require more finesse but generates high end results. Applications that require premium laminated surfaces will favor cell cast acrylic.
Almost anyone can butt two pieces together, but a bubble-free joint is the mark of a quality craftsman and a discerning customer with a budget. Consider a quality 5-sided museum box. Instead of running a bead of glue and holding the pieces together for 30 seconds, this application could require a 2-part epoxy adhesive mix of resin and hardener applied into a scored wedge which is then trimmed and polished.
The “C” (or “B”) Word
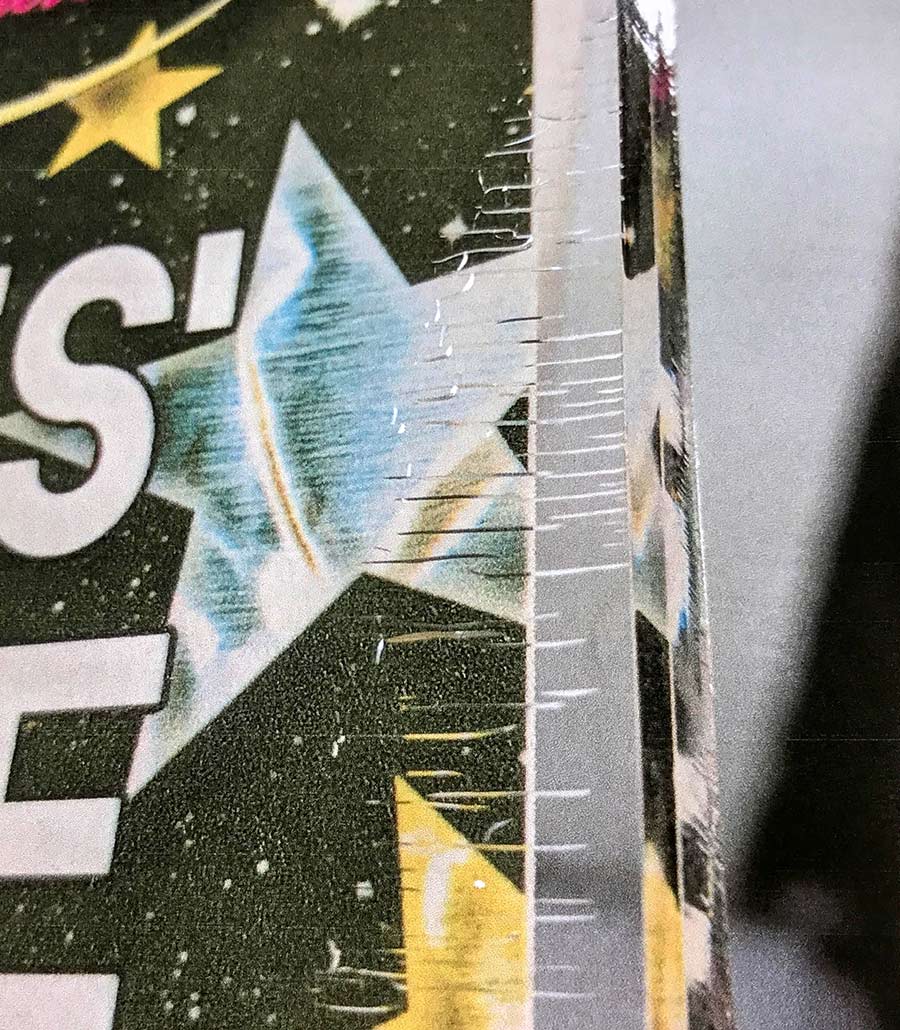
Crazing can be avoided with sharp carbide tooling and airflow to cool cut edges.
Crazing or bubbling looks like tiny hairline cracks and can happen when material is heated during cutting and then exposed to chemicals like alcohols and caustic solvents, or after some intensive thermoforming; especially if the adhesives are applied when the material is still hot.
Fabricators can avoid this unattractive condition with sharp carbide tooling and airflow to cool the edges. When continuous cutting, don’t stop the program while the cutter is spinning.
The Forming & Bending
Heating the sheet evenly is critical when you apply it to a mold that is at a receptive temperature and then cooled at a controlled rate. There are heat transition temperatures which guide the forming range beyond which you lose elasticity or shape holding strength.
The Polish
Keep in mind that the sudden heating of the sheet when flame polishing induces a high degree of stress in the work piece — be sure to anneal the part to decrease the amount of stress and reduce or prevent the chance of crazing.
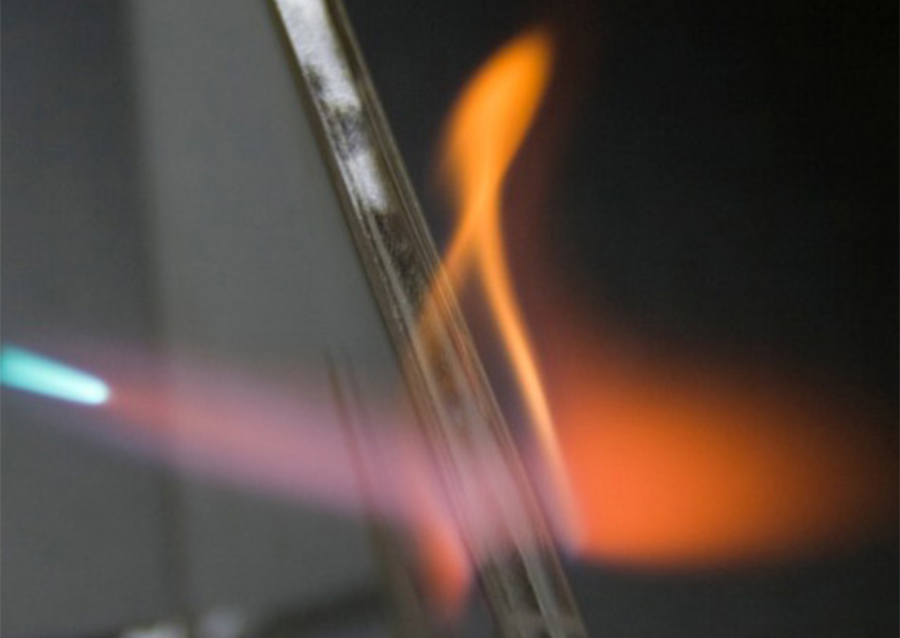
Flame polish is used in conjunction with sanding and buffing to achieve a smooth finish.
The Art
Each job requires creatively strategizing the challenge of the project from the get-go. Anticipate the results of materials, cementing, bonding, laser or table cutting, routing, drilling, edge and surface finishing. Whether you manage a job shop running volumes at high speeds or a more complex facility turning out high end pieces, every successful fabricator will devise their own scalable solutions to run a profitable operation.
Input from Ralph Meyer, Meyer Plastics, Inc., David King, Pacific Polymer Group, Nick Gross and Greg Clark, Regal Plastics and George Southard (Retired plastics peddler).
Webinar: Best Practices for Fabricating See-Through Barriers